Proper installation and maintenance are crucial for ensuring the optimal performance and longevity of straight bevel gears. Here are some practical tips to consider:
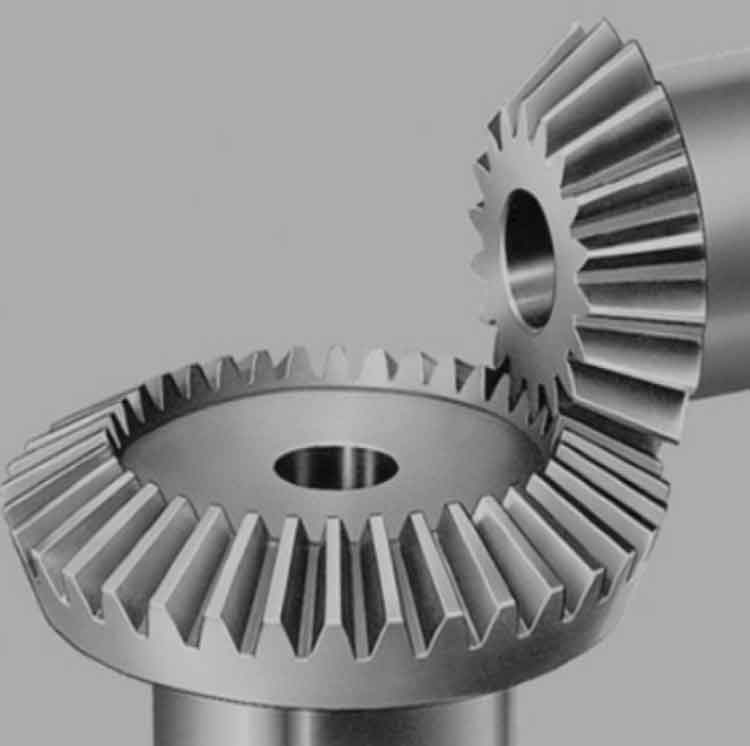
- Proper Alignment: Ensure accurate alignment of the mating shafts and gears during installation. Misalignment can cause premature wear, increased noise, and reduced efficiency. Follow the manufacturer’s specifications for alignment tolerances and use alignment tools such as dial indicators or laser alignment systems.
- Torque and Preload: Apply the recommended torque and preload values during gear assembly. Under-tightened or over-tightened bolts can lead to gear misalignment, excessive backlash, or bearing failure. Refer to the manufacturer’s guidelines for the correct torque specifications and preload values.
- Lubrication: Adequate lubrication is essential for smooth gear operation and to prevent wear and overheating. Use the recommended lubricant specified by the gear manufacturer. Follow the lubrication schedule and ensure proper oil levels and quality. Regularly monitor the condition of the lubricant and replace it at recommended intervals.
- Inspection and Maintenance: Regularly inspect the gears for signs of wear, damage, or abnormal noise. Check for any leaks, misalignment, or loose bolts. Perform routine maintenance tasks such as cleaning, greasing, and re-tightening as required. Address any issues promptly to avoid further damage.
- Gear Meshing and Backlash: Monitor the gear meshing and backlash during operation. Excessive backlash can result in reduced accuracy and performance. If necessary, adjust the gear meshing by shimming or repositioning the gears to achieve the desired backlash within the manufacturer’s recommended limits.
- Temperature and Environment: Maintain suitable operating temperatures and environmental conditions for the gears. Extreme temperatures, contaminants, or corrosive substances can affect gear performance and longevity. Ensure proper ventilation, temperature control, and protection against dust, moisture, and chemical exposure.
- Training and Expertise: Ensure that the personnel responsible for installation and maintenance have the necessary training and expertise in working with straight bevel gears. They should be familiar with the gear specifications, installation procedures, and maintenance requirements. Consult with gear manufacturers or industry experts if needed.
- Record-Keeping: Maintain a record of installation dates, maintenance activities, and inspections. This record helps track the gear’s performance over time, identify any recurring issues, and schedule preventive maintenance effectively.
Remember to consult the specific guidelines provided by the gear manufacturer for the installation, maintenance, and troubleshooting of straight bevel gears. Adhering to these practical tips and following manufacturer recommendations will help optimize the performance, reliability, and lifespan of straight bevel gears in your application.