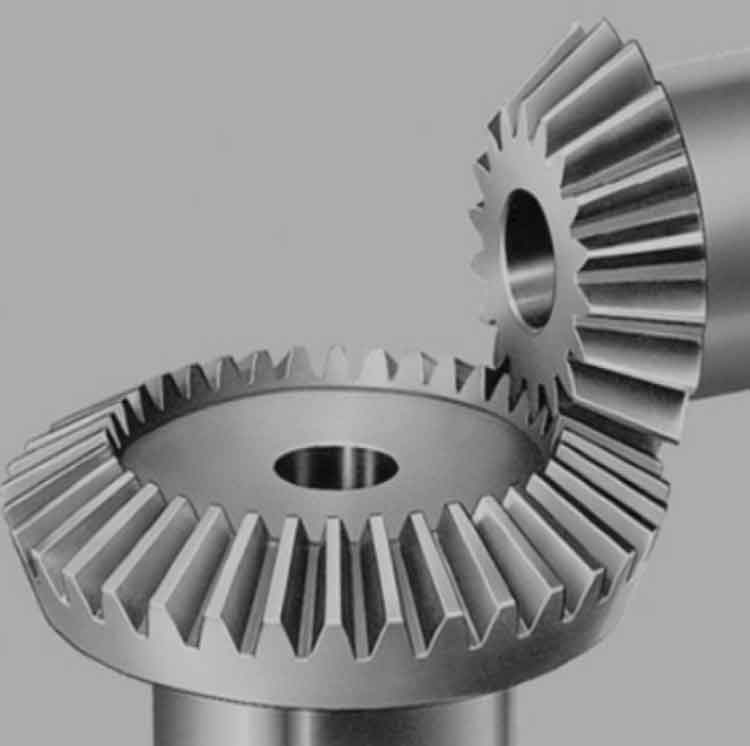
Straight bevel gears are a type of bevel gears used in gear transmission systems to transmit power between two intersecting shafts at right angles. They have straight teeth that are cut along the surface of the gear cone. Here are the basics of straight bevel gears and their gear transmission characteristics:
1. Gear Tooth Profile:
- Straight bevel gears have straight and parallel teeth that run along the cone surface of the gear.
- The tooth profile is identical to spur gears but is distributed along a conical surface rather than a cylindrical surface.
2. Gear Arrangement:
- Straight bevel gears are designed to transmit power between two shafts that intersect at a 90-degree angle.
- They are suitable for applications where the input and output shafts are perpendicular to each other.
3. Gear Ratio:
- The gear ratio of straight bevel gears is determined by the number of teeth on each gear.
- The gear ratio influences the speed and torque conversion between the input and output shafts.
4. Efficiency:
- Straight bevel gears typically have lower efficiency compared to other gear types due to sliding friction between the gear teeth during meshing.
- To improve efficiency, proper lubrication and precision manufacturing are essential.
5. Noise and Vibration:
- Straight bevel gears can produce significant noise and vibration during meshing due to the sliding action of the teeth.
- Gear noise can be reduced through proper tooth profile design and surface finishing.
6. Applications:
- Straight bevel gears are commonly used in automotive differentials, where they transmit power from the drive shaft to the wheels.
- They are also found in various industrial applications, such as machine tools, printing presses, and agricultural machinery.
7. Manufacturing:
- Straight bevel gears are typically cut using specialized machines, such as gear hobbing or gear shaping machines.
- The manufacturing process requires precision to ensure proper tooth meshing and gear performance.
8. Lubrication:
- Adequate gear lubrication is crucial for reducing friction and wear in straight bevel gears.
- Lubricants help prevent metal-to-metal contact and extend the gear’s operational life.
9. Load Distribution:
- Proper load distribution across the gear teeth is essential to avoid localized wear and premature failure.
- Careful gear design and proper alignment contribute to even load distribution.
10. Maintenance:
- Regular inspection and maintenance are necessary to ensure the proper functioning of straight bevel gears.
- Regular gear inspections help detect wear and potential issues before they lead to gear failure.
Straight bevel gears are a fundamental type of gear used in various mechanical systems to transmit power between intersecting shafts at right angles. While they have some limitations in terms of efficiency and noise, they remain an essential choice for applications requiring 90-degree power transmission. Proper design, manufacturing, and maintenance are key to maximizing the performance and longevity of straight bevel gears.