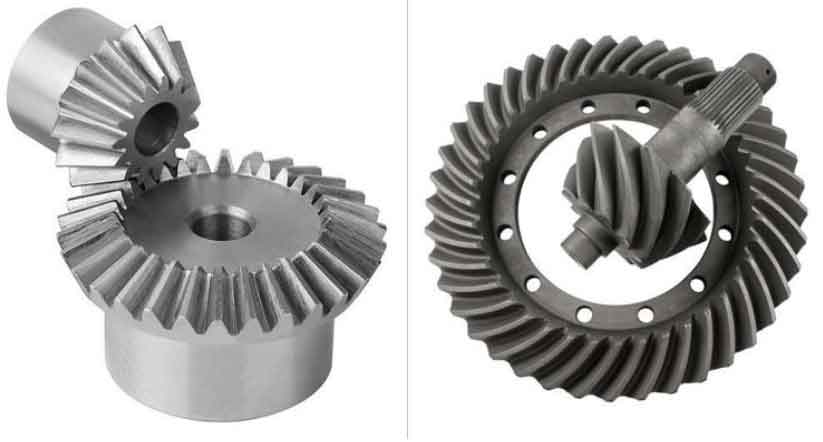
Straight bevel gears and spiral bevel gears are two common types of bevel gears used in various applications. While both have their advantages and disadvantages, their performance characteristics differ significantly. Let’s conduct a comparative analysis of their performance:
1. Tooth Engagement:
- Straight Bevel Gears: In straight bevel gears, the teeth engage abruptly and have a point contact during meshing. This can lead to higher impact and noise during operation.
- Spiral Bevel Gears: Spiral bevel gears have a curved tooth design, resulting in gradual tooth engagement during meshing. This provides a smoother and quieter operation with reduced impact and vibration.
2. Efficiency:
- Straight Bevel Gears: Due to their point contact tooth engagement, straight bevel gears may have higher friction losses and lower efficiency compared to spiral bevel gears.
- Spiral Bevel Gears: The smoother tooth engagement and larger contact area of spiral bevel gears contribute to higher efficiency and reduced energy losses.
3. Load Carrying Capacity:
- Straight Bevel Gears: Straight bevel gears are generally not as strong as spiral bevel gears and may have limitations in handling high torque and heavy loads.
- Spiral Bevel Gears: Spiral bevel gears can handle higher torque loads and have better load-carrying capacity, making them suitable for heavy-duty applications.
4. Misalignment Tolerance:
- Straight Bevel Gears: Straight bevel gears are more sensitive to misalignments, which can result in increased noise and wear during operation.
- Spiral Bevel Gears: Spiral bevel gears are more forgiving to misalignments due to their curved tooth design, resulting in smoother operation and reduced wear.
5. Manufacturing Complexity:
- Straight Bevel Gears: Straight bevel gears are generally easier to manufacture compared to spiral bevel gears, as they require simpler tooth profiles.
- Spiral Bevel Gears: Spiral bevel gears have a more complex tooth profile, requiring specialized manufacturing processes like gear grinding, which can increase production costs.
6. Noise and Vibration:
- Straight Bevel Gears: Due to their point contact tooth engagement, straight bevel gears can generate more noise and vibration during meshing.
- Spiral Bevel Gears: The gradual tooth engagement and curved tooth design of spiral bevel gears lead to quieter and smoother operation, reducing noise and vibration.
7. Applications:
- Straight Bevel Gears: Straight bevel gears are commonly used in applications where simplicity and cost-effectiveness are prioritized. They are often found in low to medium-load applications.
- Spiral Bevel Gears: Spiral bevel gears are preferred in applications that demand higher performance, efficiency, and durability. They are commonly used in heavy-duty machinery, automotive differentials, aerospace systems, and other precision applications.
Both straight bevel gears and spiral bevel gears have their strengths and weaknesses. Straight bevel gears are simpler to manufacture but may have limitations in performance and noise reduction. On the other hand, spiral bevel gears offer superior performance, efficiency, and load-carrying capacity, making them ideal for demanding applications. The choice between the two depends on the specific requirements of the application and the desired trade-offs between performance, complexity, and cost.