Gear forging plays a crucial role in streamlining gear manufacturing processes and improving overall efficiency. Here’s how gear forging contributes to efficiency gains:
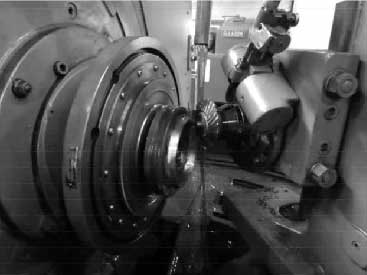
- Near-Net Shape Manufacturing: Gear forging enables the production of gears in near-net shape, which means that the initial forging process shapes the gear blank very close to its final dimensions. This reduces the amount of material that needs to be removed in subsequent machining operations, minimizing material waste and reducing machining time and costs. Near-net shape manufacturing streamlines the overall production process and improves material utilization.
- Reduction in Secondary Operations: Compared to other gear manufacturing methods like casting or powder metallurgy, gear forging often requires fewer secondary operations. The near-net shape forging reduces the need for extensive machining, resulting in reduced processing steps and shorter lead times. This streamlined process eliminates the need for additional operations such as grinding, shaping, or hobbing, leading to improved efficiency and cost savings.
- Faster Production Rates: Gear forging processes are typically faster compared to other manufacturing methods. The ability to shape gears in a single forging operation allows for higher production rates, resulting in increased output and shorter lead times. The high-speed forming capabilities of gear forging, combined with optimized die design and advanced equipment, contribute to efficient production and improved overall productivity.
- Improved Material Utilization: Gear forging maximizes material utilization by utilizing the inherent strength and properties of the forged material. The precise shaping and material redistribution during forging minimize material waste and optimize the use of raw materials. By reducing material scrap and maximizing yield, gear forging contributes to cost-effectiveness and sustainable manufacturing practices.
- Consistent and Repeatable Results: Gear forging processes offer high repeatability and consistency in gear production. The controlled forging environment, precision dies, and advanced process monitoring techniques ensure that each forged gear meets the specified tolerances and quality standards. This consistency reduces the need for rework or rejection of gears, minimizing production delays and enhancing overall manufacturing efficiency.
- Integration with Automation and Robotics: Gear forging processes can be integrated with automation and robotics, further enhancing manufacturing efficiency. Automated systems can handle various tasks, such as material handling, die changeovers, and quality inspections, with precision and speed. By reducing manual labor requirements and increasing process automation, gear forging improves overall production efficiency and reduces human error.
- Continuous Improvement and Optimization: Gear forging manufacturers are continually striving to optimize processes and improve efficiency. Through research, development, and process optimization, manufacturers can identify opportunities for improvement and implement innovative techniques and technologies. This commitment to continuous improvement helps streamline gear manufacturing processes, enhances production efficiency, and drives overall operational excellence.
By leveraging the advantages of near-net shape manufacturing, reducing secondary operations, increasing production rates, optimizing material utilization, ensuring consistent results, integrating automation, and focusing on continuous improvement, gear forging significantly streamlines gear manufacturing processes. These efficiency gains lead to cost savings, shorter lead times, improved productivity, and enhanced competitiveness in the manufacturing industry.