The mechanism of fatigue and noise generation of drive axle hypoid gear is deeply studied, and a method based on finite element method is established to study the meshing parameters of drive axle hypoid gear, such as bending strength, fatigue life, transmission error and meshing stiffness, and the corresponding influencing factors are analyzed. Based on the meshing angle of hypoid gears, a complete prediction model of bending fatigue and noise radiation of drive axle gears is established, which provides a solid theoretical basis for the in-depth and comprehensive study of the reliability of drive axle and the mechanism of vibration and noise radiation.
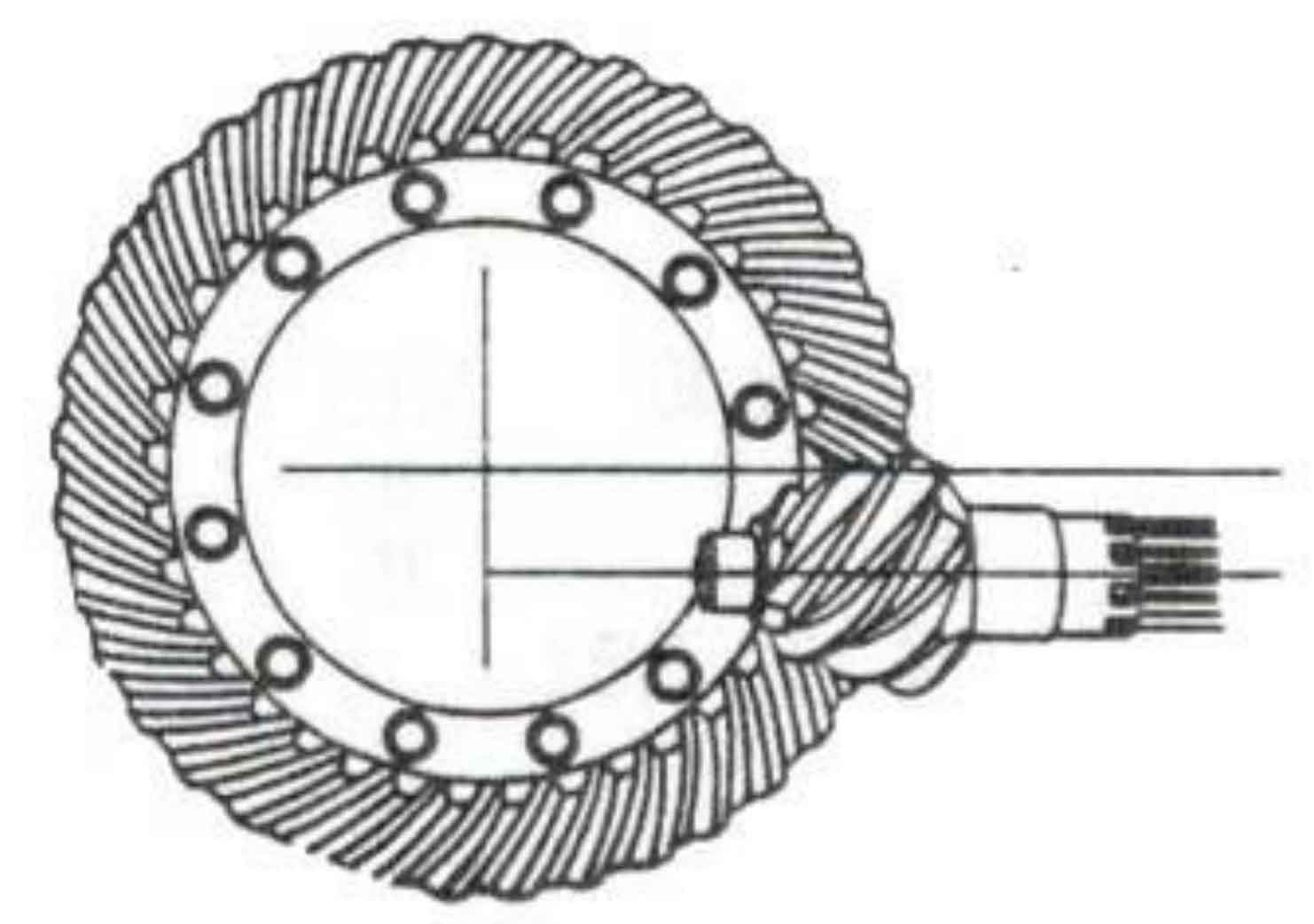
- Aiming at the problem that it is difficult to obtain the geometric model of drive axle hypoid gear, this paper will propose a numerical calculation method to establish the geometric model of HFT hypoid gear tooth surface. By analyzing the gear processing process of Gleason machine tool, the method of estimating the midpoint of gear meshing is obtained. Taking this point as the initial value, the coordinates of other points on the tooth surface are solved, and the program for solving the coordinates of hypoid gear tooth surface based on MATLAB will be established. Finally, the coordinates of the gear tooth surface are obtained and imported into CATIA software to obtain the three-dimensional model of the gear set. This three-dimensional solid model can be used for gear meshing analysis based on finite element method.
- In order to accurately simulate the real working boundary conditions of the hypoid gear of the automobile drive axle, an overall finite element modeling method of the drive axle will be established. This modeling method uses ABAQUS software to establish the substructure model of other components in the drive axle except the bearings and gears that have contact, and maps the internal degrees of freedom of the components of the substructure to the constrained node positions. The established model will be used to predict the tooth root stress of hypoid gear.
- The whole finite element model of the drive axle established above will be used to establish the prediction model of the bending stress of the hypoid tooth root of the drive axle, and the stress change history at the dangerous point in the meshing process of the hypoid gear will be obtained. At the same time, a test bench was built to measure the root stress of the hypoid gear teeth of the drive axle. This paper will compare the influence of different installation deviations of gears on the bending stress of the tooth root. Based on the change history of gear root stress, a prediction method for fast prediction of bending fatigue of drive axle gears will be established, and the Fatigue Bench test will be carried out on the drive axle. Using this method, the influence of different types of installation deviation on bending fatigue of drive axle gears will be analyzed. Through the above methods, the bending stress state and bending fatigue life of the tooth root of hypoid gears can be predicted, and provide guidance for the reliability design of gears.
- In order to analyze the transmission error and time-varying meshing stiffness caused by the meshing process of the hypoid gear of the drive axle, a finite element model of the load meshing analysis (LTCA) of the hypoid gear wheel will be established to calculate the static transmission error and dynamic transmission error of the gear, and the relationship between the two will be discussed, as well as the influence of load and installation deviation on the static transmission error, as well as the influence of speed fluctuation on the dynamic transmission error, It provides guidance for the design and optimization of drive axle hypoid gear transmission error. Finally, a method of calculating the meshing stiffness of gears by using finite element method will be established, and the influence of different loads on the meshing stiffness of gears will be analyzed. The stiffness calculation results provide a basis for the dynamic analysis of hypoid gear system.
- Vehicle drive axle noise is one of the main noise sources affecting vehicle interior noise. Therefore, the generation mechanism of drive axle noise will be comprehensively studied, and a drive axle noise radiation prediction model based on the mutual coupling of hypoid gear pair system and drive axle housing dynamic effect will be established. The 14 degree of freedom coupling model of the drive axle gear is established, and the parameters of the gear system are identified. The gear meshing direction is obtained through gear meshing. At the same time, build a test bench to measure the vibration and noise level of the drive axle. This chapter will establish a complete drive axle noise prediction model, which can provide guidance for the control and optimization of drive axle noise.