At present, miniaturization, high speed and low consumption are the important development direction of gear transmission parts. Compared with other types of gears, the hypoid gear with super reduction ratio has the characteristics of large transmission ratio, large coincidence, stable transmission and strong bearing capacity, and is lower in processing cost and higher in transmission efficiency than the general worm gear. Therefore, super reduction ratio hypoid gear can gradually replace the traditional worm gear device, and is widely used in CNC machine tool servo systems, industrial robots, electromechanical integration and other products.
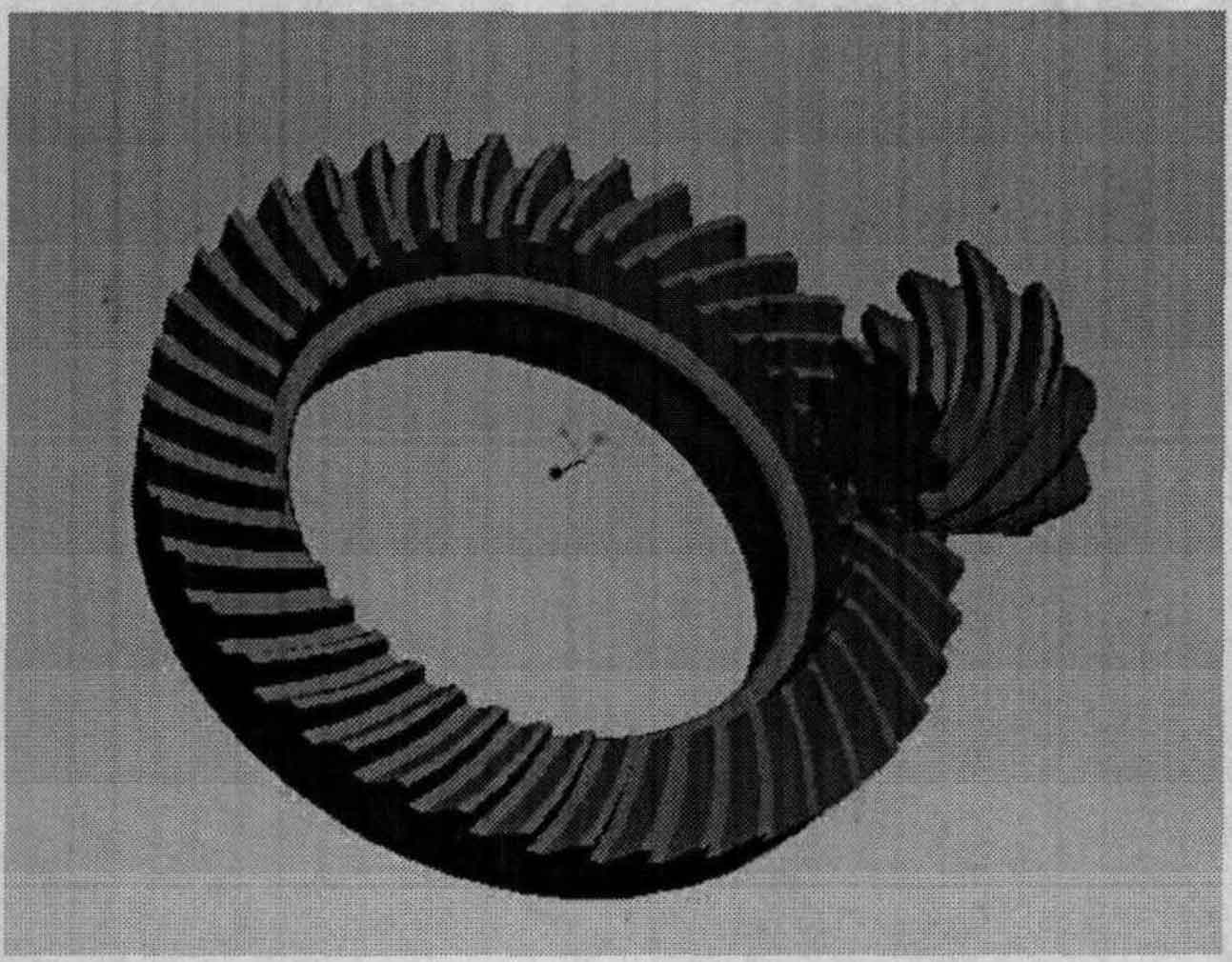
Wei Bingyang et al. discussed the evolution of pitch cone of hypoid gear with high reduction ratio and the evolution process of arc contour teeth in the direction of tooth height and tooth thickness, and determined the pitch cone of large gear and small gear with the goal of maximizing the volume of small gear through optimization solution method. Using Matlab and UG software, three-dimensional simulation and tooth cutting experiments were carried out on hypoid gear with a tooth ratio of 3 ∶ 60. Zhang Yu et al. discussed the design, manufacturing principle and method of machining spiral bevel gears and hypoid gears with the full process method. Tong Angxin determined the pitch cone of the big gear and the small gear by optimizing the solution method, and obtained the processing parameters and tooth surface coordinate points of the small gear by using Matlab programming. He carried out the assembly and motion simulation of the three-dimensional model of the two pairs of gears with a tooth ratio of 3 ∶ 60 and 4 ∶ 48 respectively, and carried out the gear cutting test for the gear pair with a tooth ratio of 3 ∶ 60, which verified the correctness of the designed gear pair. In order to reduce production cost and improve production efficiency, Dangyugong et al. predicted the life of cold rotary forging die and analyzed the process optimization; The stress and strain of the die in the rotary forging process were obtained through the thermal mechanical coupling finite element numerical simulation, and the die life was estimated with the aid of the mathematical model of die life estimation under specific process parameters;
According to the life calculation results, the die life under different process parameter combinations is compared and analyzed to find out the influence rule of each process parameter on the die life, and the reasonable process parameter combination is determined. Based on the gear fatigue failure theory, Chen Xingbin et al. established the gear CAE model using Workbench and Ncode methods, completed the gear contact dynamics and fatigue life prediction, and analyzed the static and transient characteristics of the gear pair with the main influencing factors of fatigue durability as the characterization parameters.
(1) A calculation method is derived to calculate the design parameters of the small wheel from the design parameters of the big wheel, and the basic parameters of the gear blanks of the big wheel and the small wheel are calculated.
(2) The coordinates of discrete points on the tooth surface are calculated, and the three-dimensional model of hypoid gear with super reduction ratio of 2 ∶ 60 is established. According to the meshing relationship, the finite element simulation model is obtained.
(3) Increasing the speed and reverse torque will reduce the minimum fatigue life of hypoid gears with super reduction ratio. When different tool tip fillets are used for machining the gear root, the minimum fatigue life of hypoid gears with super reduction ratio will increase with the reduction of stress concentration.
The research on hypoid gears has been carried out, but the failure mechanism of hypoid gears with super reduction ratio is still lacking. The parameters of hypoid gear blank with super reduction ratio are optimized in, and the failure mechanism of hypoid gear with super reduction ratio under different working conditions is explored in the ANSYS Workbench finite element software to provide design basis for improving the strength of hypoid gear with super reduction ratio.