The stress state and fatigue life of hypoid gear in the main reducer of drive axle is one of the most important design requirements in the design of drive axle. Due to the large angle geometric nonlinearity and contact nonlinearity of hypoid gears during meshing, the gear meshing process has strong nonlinear characteristics, which is not easy to be simulated by establishing a simple mathematical model. At present, the finite element method is widely used to analyze the gear meshing and gear bending stress. The finite element analysis of gear tooth root bending stress is mainly divided into static finite element analysis and dynamic finite element analysis. The research shows that the gear meshing speed has little effect on the tooth root bending stress in the meshing process of hypoid gears. Through the change of tooth root bending stress in the static meshing process of gears, the change law of tooth root bending stress in the actual operation process of gears can be reflected.
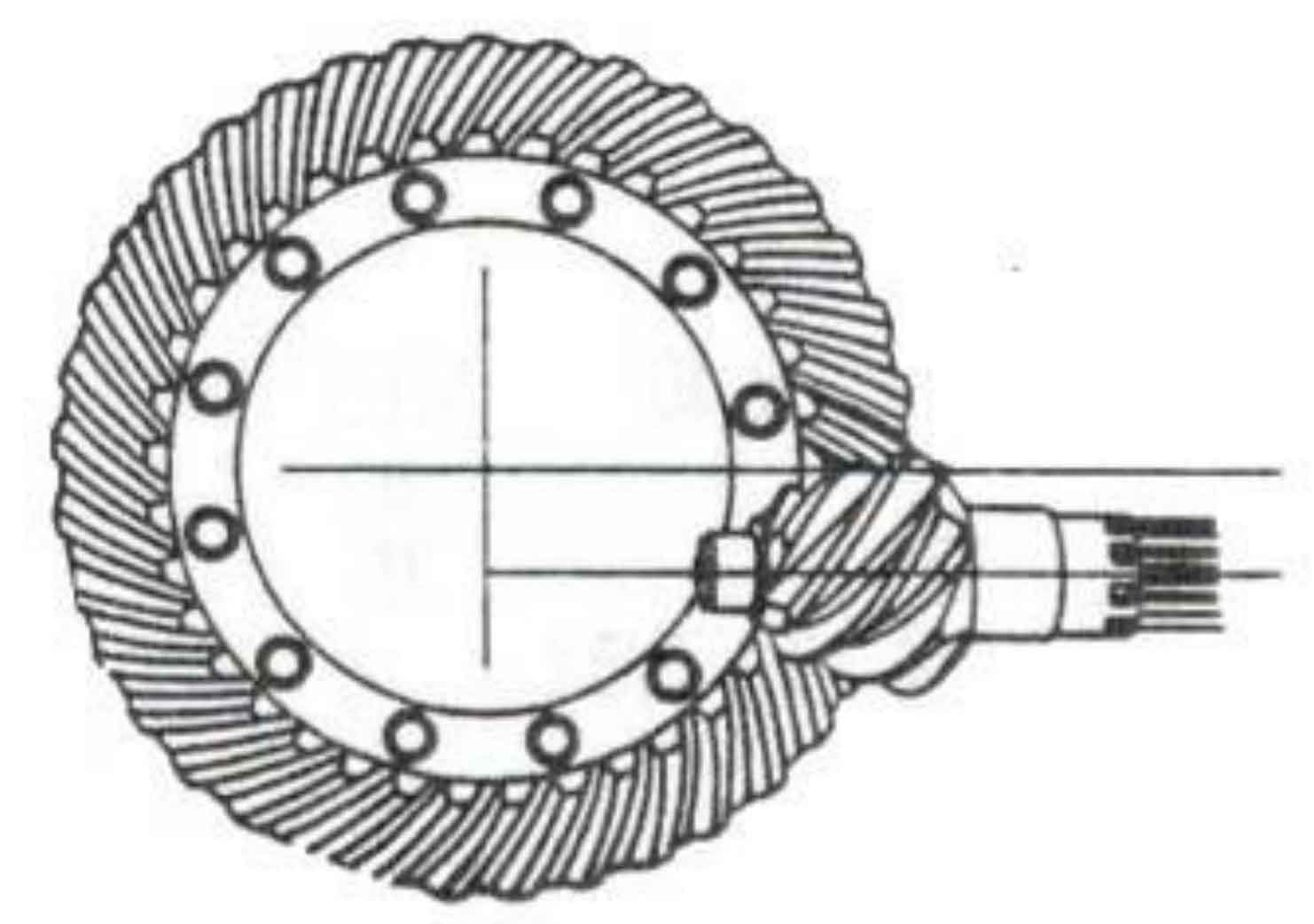
In the process of finite element modeling of hypoid gears, due to the complex spatial structure of gears, it is easy to cause serious distortion of the finite element mesh, which makes the finite element analysis process not convergent or the calculated value inaccurate. Therefore, there are two main methods for the static finite element meshing analysis of hypoid gears. The first method is to fix one gear and load the other gear. The second method is to fix one gear, load the other gear, then rotate the gear a small angle, fix one gear, load the other gear, and so on, so as to obtain the change of root stress of gear teeth in a meshing cycle. These modeling methods cannot simulate the real continuous operation process of gear pair. Moreover, for the drive axle hypoid gear, the above gear tooth root bending stress analysis method does not consider the deformation of the gear system support shell and support bearing. Therefore, it is necessary to establish a static finite element model of the integral drive axle that truly reflects the meshing process of the hypoid gear, so as to provide a basis for the comprehensive analysis of the root stress of the hypoid gear of the drive axle.
The overall finite element model of a light truck drive axle will be established. First, the geometric model of the drive axle will be classified according to the gear transmission system. Secondly, in order to reduce the calculation complexity of the finite element model and improve the calculation speed, the substructure of other components in the drive axle except the bearing and hypoid gear is established by using the ABAQUS substructure method, and the substructure model is assembled with the bearing and gear according to the structural design requirements. Finally, in order to enhance the convergence of the model, the modeling method of bearing contact and hypoid gear contact, as well as the setting of boundary conditions of the overall finite element model, will be introduced in detail.