The pre forging die and final forging die need to be designed for the precision forging of the half shaft gear of “one heat, two forgings”. The horizontal parting surface of the two sets of dies is moved from the tip of the big end gear to the joint of the outer diameter of the inverted wheel crown and the back cone, so as to increase the friction force between the tooth die and the workpiece and facilitate the positioning of the trimming die. Because the working condition of the die is very bad, in order to improve the life of the die, the combination die structure is adopted for the tooth die and the half axis die.
Fig. 1 shows the structure diagram of the pre forging die for the half axle gear. The tooth die of the pre forging die is the upper die, the contact time between the tooth die and the high-temperature billet is short, and the temperature rise of the die is small, which is conducive to improving the life of the tooth die. In addition, it can also make the half axle concave die difficult to accumulate oxides in the tooth model cavity as the lower die, and the unilateral gap between the billet and the concave model cavity is the knife, In order to ensure the accuracy of the upper and lower die guide, the guide post and guide sleeve are used to guide the die.
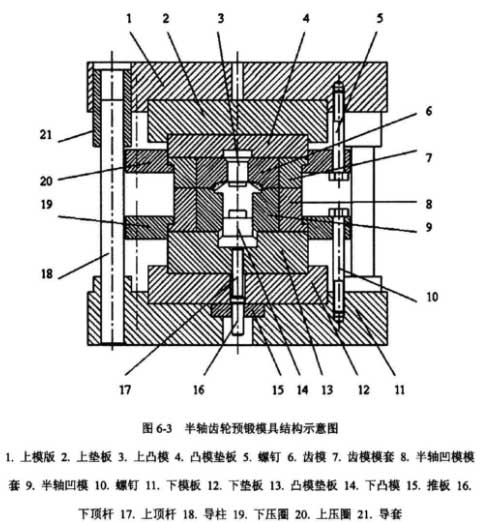
The upper base plate and the lower base plate are respectively fixed on the upper template and the lower template with screws. In order to make the figure clear, the screws connecting the upper and lower base plates and the upper and lower templates are not shown in Figure 1. The tooth mold and the tooth mold sleeve are prestressed, and the screw uses the upper pressing ring to fix the tooth mold sleeve on the upper template. The half axle concave mold and the half axle mold sleeve are prestressed combined, and the screw uses the pressing ring to fix the half axle mold sleeve on the lower formwork. At the beginning of forging, the upper die goes down, the guide post is first led into the guide sleeve, and then the upper die contacts with the blank. After the blank starts forging, the upper die goes up, and the forging is left in the half axle die. The forging is ejected by the lower ejector of the friction press.
Figure 2 shows the structure diagram of the final forging die for the half shaft gear. Because the final forging temperature is lower than the pre forging temperature, the tooth die is designed in the lower die, and the temperature rise of the tooth die will not be too high. At the same time, it is convenient for the forging to use the tooth shape to place the final forging, the deformation of the blank is small, and the stroke of the slider is far less than the guide length of the lock, so the lock guide is adopted for the die because the friction force of the half shaft cavity on the workpiece is large, After the forging, the workpiece stays in the half shaft die. In order to facilitate the smooth demoulding of the workpiece, the elastic ejector is designed for the upper die.
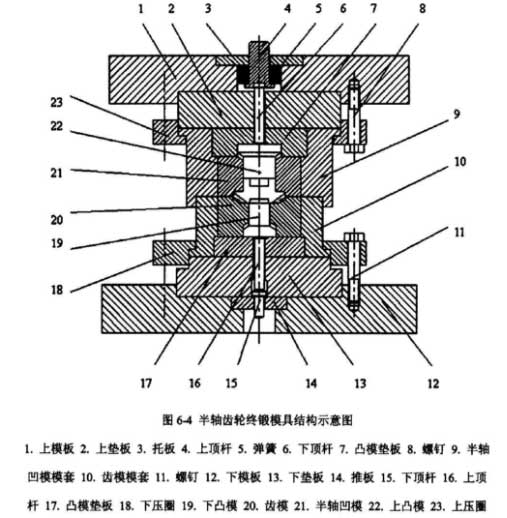
The upper base plate and the lower base plate are respectively fixed on the upper template and the lower template with screws. In order to make the figure clear, the screws connecting the upper and lower base plates and the upper and lower templates are not shown in Figure 1. The tooth mold and the tooth mold sleeve are prestressed, and the screw uses the lower pressing ring to fix the tooth mold sleeve on the lower template. The half axle concave mold and the half axle mold sleeve are prestressed, and the screw uses the upper pressing ring to fix the half axle mold sleeve on the upper formwork.
At the beginning of forging, the upper punch is at the lower limit position under the action of the spring, and the upper die moves downward. The lock catch of the tooth die sleeve and the half axle concave die sleeve is first led into the upper die and continues to move downward. The upper punch contacts with the blank, and the spring is compressed. After the forging of the blank begins to forge, the upper die moves upward. The forging deformation force is eliminated, and the tension of the spring makes the forging break away from the half axle concave die, The forging is ejected by the lower ejector of the friction press.