Based on the design of the process flow, the main purpose of the closed hot die forging step is to change the internal structure of the gear blank from the as cast to the as forged state through the plastic flow of metal, refine the grains and improve the local possible casting defects. Compared with the open die forging, the closed die forging has higher material utilization rate, but more stringent requirements on the flow of forging materials. For the shape and tooth shape design of the preform of the closed hot die forging of the spiral bevel gear, not only the effect of the hot forging of the gear blank, but also the influence of the tooth shape of the spiral bevel gear casting on the casting process should be considered. Based on the above factors, this paper proposes to use the approximate trapezoidal tooth shape scheme in the closed hot die forging process.
If the full tooth height of the trapezoid tooth profile is adopted, the impact of the workpiece on the hot die forging die will be too large to affect the service life of the die; moreover, if the tooth profile groove of the casting is too deep during the casting process, it will also have adverse effects on the filling cavity of the liquid metal and the solidification process of the casting.
In closed die forging, the material can flow freely all the time in the process of workpiece forming by setting the shunting space on the die or billet, which can significantly improve the flow filling performance of metal materials, reduce the pressure of die bore and forming load, effectively reduce the wear of the die in the process of processing, and reduce the requirements for the specific accuracy of blanking. This method is called shunting method The method is called shunt method. Research shows that. Some researches have shown that the application of shunting technology in gear forming can not only effectively solve the problem of insufficient filling at the corner line of gear shape, but also greatly reduce the internal pressure and forming load of the die bore.
Tooth profile design of preform by closed hot die forging
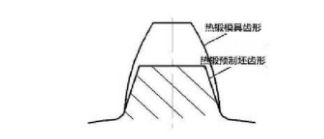
Based on the idea of split flow method, it is decided to adopt the approximate trapezoidal tooth shape scheme with the size of 1 / 2 tooth height and full tooth height to leave a certain split space between gear blank and hot forging die to improve the material flow performance of gear blank, as shown in the figure.
Establishment of finite element model and setting of relevant parameters
Referring to the tooth size of cold precision forging preform, the closed hot die forging die chamber is designed and the 3D solid model is built in CATIA. The die data and the gear blank data of each scheme are imported into the pre processor module of the DEFORM software. Already in the literature block. There has been literature [48] on [48] on the preheating temperature of blank and die speed in the process of gear hot die forging of 20CrMoH material. For the setting of hot die forging process parameters, please refer to the relevant conclusions.
For the setting of preprocessing simulation parameters:
1.Define the type of preform material as aisi4120 and set the material property as plastic body;
2.Because the geometry of the preform of the driven spiral bevel gear in hot die forging is very complex, both the requirements of simulation accuracy and the efficiency of calculation should be taken into account when meshing, so the relative meshing method is adopted and the number of the mesh of the gear blank is determined to be 200000; in order to reduce the volume loss caused by the mesh distortion in the forming process, the FEM + mesh mode is activated;
3.Set the temperature of the workpiece to 1150 ℃, set the lower mold to tooth mold, and set the temperature of the upper and lower mold to 250 ℃ (preheating temperature); the lower mold is fixed, and the moving speed of the upper mold is set to 10 mm / sec;
4.Due to the high forming temperature of hot die forging and the good lubrication between the blank and the die, the friction coefficient is set to 0.3; the heat conduction coefficient between the gear blank and the outside is set to 5.