1. Spraying technology of superfine composite materials
In recent years, Chinese and Japanese companies have studied and applied the spraying technology containing MoS2 and ultra-fine metal particle composite materials. As a new construction method in the field of pressure spraying, it has achieved good practice effect in the field of high-strength gear surface strengthening, and its process is shown in the figure.

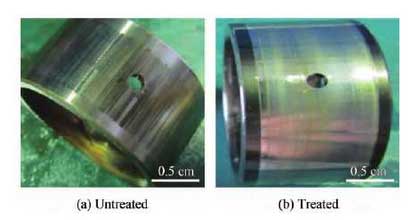
The ball grinding ball and solid lubricant (MoS2) composites are driven by high pressure inert gas to impact the gear surface under high temperature and high pressure, and penetrate into the gear surface 1 ~ 20 μ m deep, making the metal surface 20 The phase structure of μ m depth is changed, and many tiny holes are formed on the tooth surface due to the impact of spherical particles, which reduces the external stress caused by the fine compression of the surface structure and significantly improves the surface hardness. The solid lubricant is attached to the surface to improve the self lubrication of the tooth surface. Reduce the tooth surface roughness, improve the meshing quality and reduce the meshing noise.
As shown in the figure, the inner edge of a transmission gear needle roller bearing is greatly improved after composite material spraying treatment. At the same time, numerous tiny pits are formed on the surface, which is conducive to the formation of oil film, thus improving the adhesion of oil film on the friction surface and enhancing the fatigue limit.
2. Compound strengthening of gear surface
With the continuous improvement of gear requirements and the continuous development of gear surface machining engineering technology, it has become an important means in the field of gear to compound two or more surface strengthening technologies to improve the surface integrity of gear to meet the more demanding use requirements of gear, such as QPQ (quench Salt bath composite treatment technology, thermal spraying and shot peening combined composite coating technology, coating and shot peening composite technology, etc. QPQ salt bath composite treatment technology is a high corrosion resistance and wear resistance metal surface modification technology of low temperature salt bath nitrocarburizing and salt bath oxidation. General Motors uses this technology to improve the wear resistance of cylinder liners of internal combustion engines. QPQ technology is also used for the camshaft of Volkswagen and the internal gear of the reducer of heavy truck of SINOTRUK. The combination of thermal spraying and shot peening makes the gear not only have high bending fatigue resistance, but also have good contact fatigue resistance, and increase the antifriction and lubrication performance of the gear.
3. Drum polishing and abrasive flow machining technology
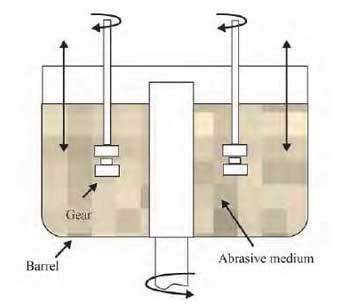
Under certain conditions, barrel grinding can improve the tooth surface roughness and fatigue life of gears with low cost. The figure shows the processing outline of the drum polishing and grinding method, in which the mixture of grinding stone and grinding powder with different materials of several millimeters in diameter and the grinding processing tank rotate in the same direction (100 m / min), the rotation direction of the processed gear is opposite to that of the processed gear, and the processing time is about 15-30 min. Professor suoyama of the University of saga in Japan, together with the author and Sumitomo heavy industry company in Japan, studied the drum polishing and grinding method after the gear peening strengthening treatment, and achieved good experimental results, which attracted the attention of relevant experts in the United States and Japan.
Abrasive flow machining is a new technology of polishing and deburring the workpiece surface with the elastic material composed of polymer carrier and abrasive. Xu et al. [48] carried out abrasive flow treatment on helical gears. Through simulation and experimental research, it was proved that AFM can effectively improve the surface roughness quality of helical gears. The selection and proportion of abrasive media are very important to the machining effect in the technology of roller grinding and polishing and abrasive flow. It is very important to continue to carry out the simulation and experimental research of abrasive on the surface roughness and fatigue strength, as well as the optimal selection and proportion of a variety of abrasive media.