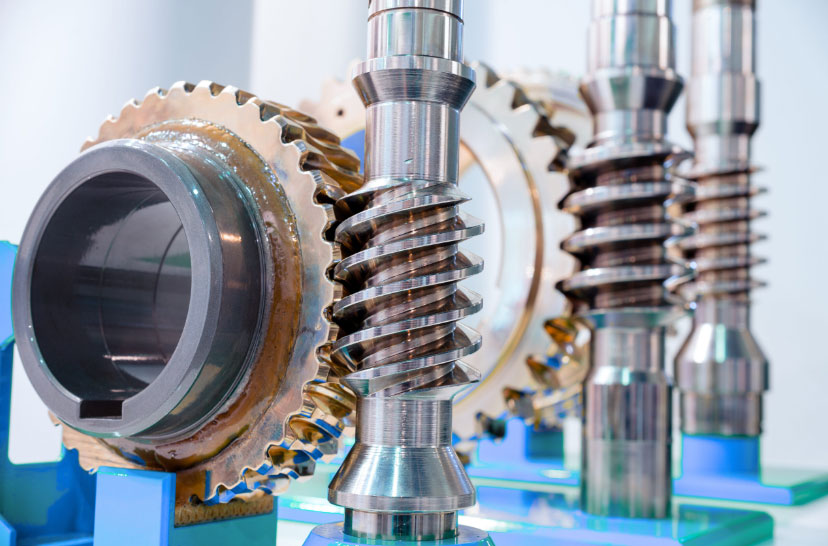
Worm gears are an essential component in various mechanical systems, translating rotational motion between non-parallel shafts. Conventionally, worm gears are manufactured using standard designs, limiting their adaptability to specific applications. However, recent advancements in manufacturing technologies have enabled the production of custom worm gears with unparalleled design flexibility. This article delves into the vast possibilities of custom worm gear design, exploring the benefits, challenges, and applications of tailoring these precision-engineered components to perfection.
The advent of additive manufacturing and computer-aided design tools has revolutionized gear manufacturing. Custom worm gears are meticulously designed to meet precise specifications, addressing challenges posed by complex motion transmission requirements. This paper investigates the advantages of custom worm gears over traditional off-the-shelf options and highlights the novel applications enabled by this technological leap.
1.Design Flexibility:
Unlike standard worm gears, custom worm gears offer an unprecedented level of design flexibility. Engineers can fine-tune gear parameters such as helix angle, pitch diameter, pressure angle, and lead angle to optimize efficiency, reduce backlash, and enhance load-bearing capabilities. The article examines how this adaptability allows for smoother and more efficient motion transmission.
2.Materials and Manufacturing Techniques:
Custom worm gears can be crafted from a broad spectrum of materials, ranging from traditional alloys to high-performance composites. The paper analyzes the impact of material selection on gear durability, weight reduction, and thermal management. Furthermore, it discusses various manufacturing techniques like additive manufacturing, CNC machining, and hobbing, showcasing their influence on gear performance.
3.Noise Reduction and Vibration Damping:
Custom worm gears can be engineered to reduce noise and vibration, addressing concerns common in conventional worm gear applications. The article explores methods to optimize gear profiles, tooth profiles, and lubrication strategies to achieve quieter operation and improved gear longevity.
4.Performance Optimization:
This section examines how custom worm gear design can enhance system performance in specific applications, such as robotics, automotive transmissions, aerospace systems, and precision machinery. By tailoring worm gears to suit unique demands, engineers can achieve higher efficiency, accuracy, and reliability.
5.Challenges and Considerations:
While custom worm gears present numerous advantages, they also come with certain challenges. The article discusses the implications of complex design processes, manufacturing costs, and potential limitations in achieving extreme gear ratios. It also addresses how to strike the right balance between customization and practicality.
6.Future Perspectives:
As technology continues to evolve, the article contemplates the future of custom worm gears. This includes the integration of smart materials, advanced simulations, and artificial intelligence in gear design, manufacturing, and maintenance.
The design flexibility of custom worm gears unlocks boundless possibilities for tailored precision in mechanical systems. The paper emphasizes the importance of understanding gear requirements and optimizing the design process to reap the full benefits of this transformative technology. Custom worm gears hold the potential to revolutionize motion transmission, enabling machinery to operate at its best and revolutionizing various industries.