1. Gear Fracture and Analysis
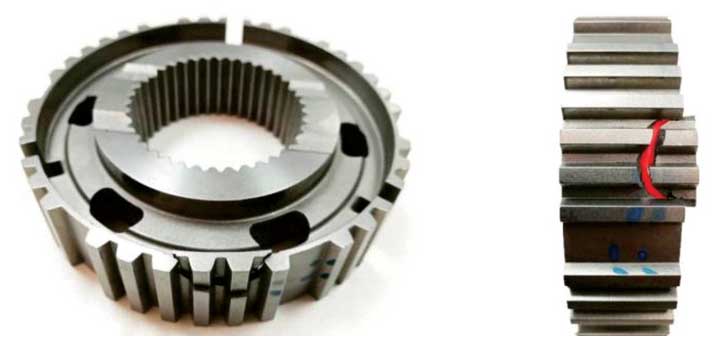
According to user feedback, the gear breaks under heavy load and the fracture occurs in the tooth area as shown in the figure.After removing the fracture, the density is 6.82 g/cm3, and then observed under light microscope and scanning electron microscope. The fracture morphology and metallography are shown in the picture.
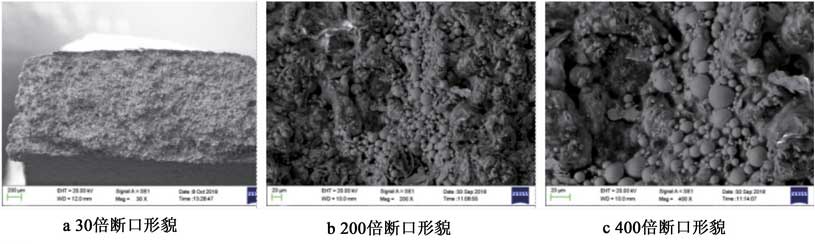
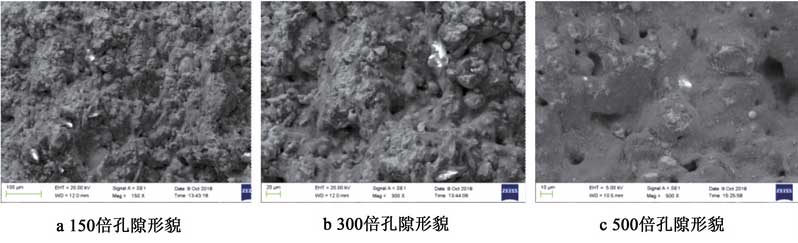
It can be found from the graph that a large number of spherical substances of different sizes are gathered at the fracture location with diameters of 3-20um. Some spherical substances with larger diameters are embedded in the metal matrix and scattered with smaller diameters.From the pore morphology Figure 3c, it can be found that there are a lot of pores in the fracture position of the teeth, and the pore size is about 3-10um, which indicates that the compactness of the powder metallurgical structure is not high.In addition, the metallography in Figure 4 shows that there are few pearlite tissues and a lot of black holes in the tooth area.It can be seen that the fracture location does not fully realize the diffusion, welding and recrystallization of powder particles, resulting in weak bonding force between the powders. Therefore, under the overload condition, fracture will take place preferentially.
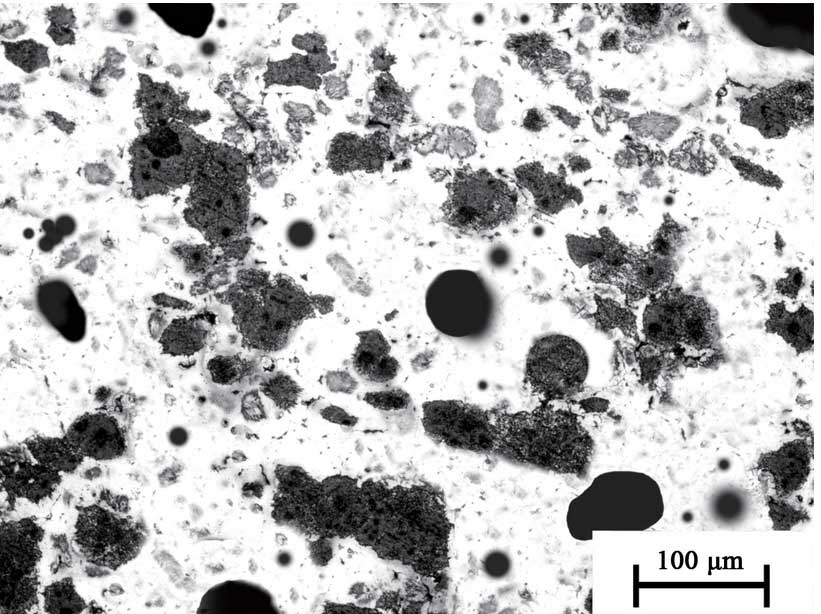
EDS energy spectrum analysis shows that the main elements of spherical material are iron and carbon, of which the content of carbon element is about 44% and that of iron element is 56%. It is an iron-carbon compound formed by sintering, as shown in Fig.EDS results also reflect the problem of insufficient powder diffusion.
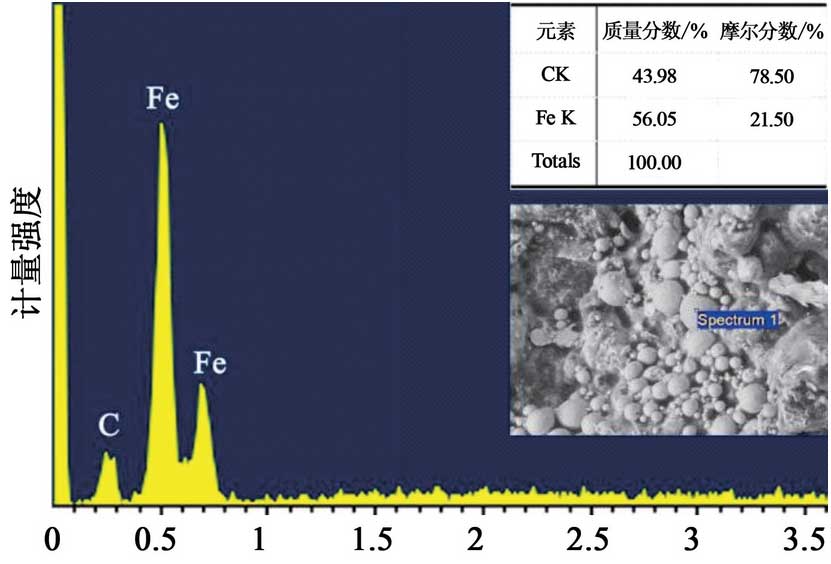
In conclusion, it can be judged that the main reason for the fracture of powder metallurgical gears is improper matching of sintering process. The sintering temperature is too low, which results in insufficient diffusion of powder, melting and recrystallization. The solution to the above problems is to increase the sintering temperature and prolong the sintering time properly.
2. Sintering Process Optimization and Powder Metallurgy Microstructure Analysis
In order to verify the feasibility of the above process improvement measures, the same batch of pre-alloyed powder was taken for verification test.The sintering temperature is increased to 1120 C and the sintering time is increased to 90 min.Compared with the original production process, the temperature is increased by 70 C and the time is increased by 20 min.
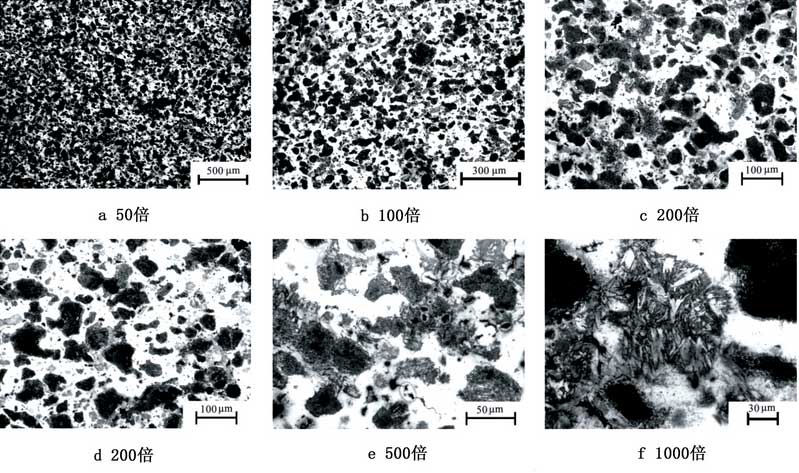
Sampling from the prepared gear teeth shows that the density of the gear prepared by the new process increases to 7.11 g/cm3, reflecting the increase of powder metallurgical density.Then, metallographic analysis is carried out on the tooth area, and the thin layer position organization of the tooth and the tooth edge is mainly observed by different magnifications. The metallographic picture is shown in the figure.In Figure 6, the black part is pearlite structure and the white part is ferrite-martensite mixed crystal structure.Comparing with the metallographic diagram of gear prepared by the original process, it is found that the compactness of powder metallurgical structure has been significantly improved after the improvement of sintering process, no obvious voids and voids have been found, and the pearlite is evenly distributed.The magnified observation shows that the pearlite is a sponge-like fine pearlite with a size of 30-50um um.In addition, needle-like martensite was found to be aggregated with a size of 20-40 um under 500 times of light.According to JB/T 2798-1999 Metallographic Standard for Iron-based Powder Metallurgical Sintered Products, the number level of pearlite in this powder metallurgical gear is Pearl 60.
3. Impact test and fracture analysis
In order to verify the performance of powder metallurgical gears sintered by the improved process, Charpy impact tests were carried out on samples taken from the original broken gears and the newly prepared teeth.Impact samples can not be prepared by GB/T 9096-2002 method due to gear size.Therefore, a complete tooth is taken for impact comparison. As shown in Figure 7, the impact test is carried out by fixing a special fixture on the specimen support of the impact tester.
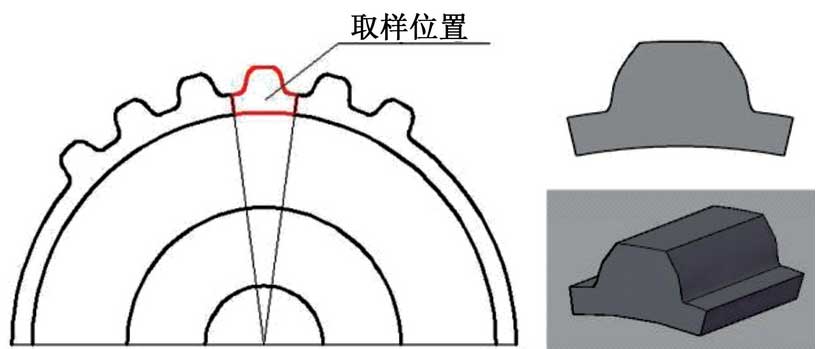
The impact test results show that the impact absorption energy of powder metallurgical gears prepared by the new process is 14.3 J and that of original gears is 9.2 J. The impact toughness of gears is increased from 9.8 J/cm2 to 15.2 J/cm2 by 55% based on the calculation of 0.938 cm2 cross-section area of gears.
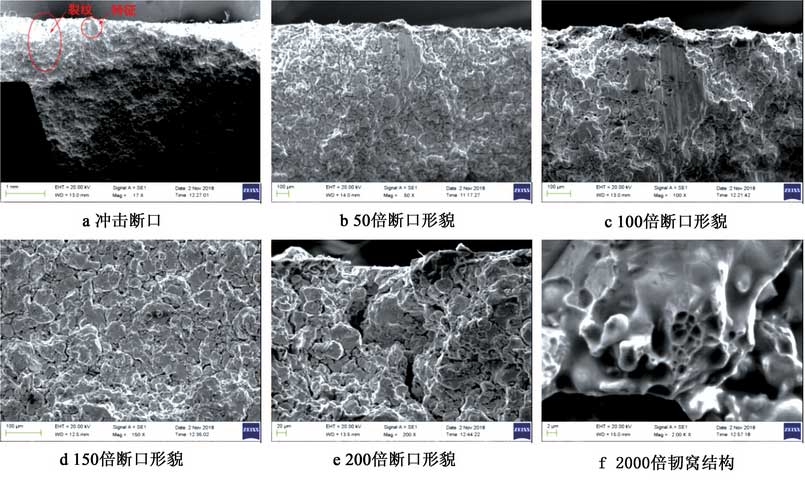
The gear fracture prepared by the new process is observed by SEM and it shows typical impact fracture characteristics with the characteristic size of 100um x 300um as shown in Fig. a-c.Fig. D-E shows that the fracture mode is cleavage fracture. Under impact, the crack propagates along the cleavage surface through transgranular cleavage fracture, resulting in tooth fracture.The presence of micro-dimples at the fracture location, as shown in Fig. 8f, indicates that the new process makes the gear plastic to some extent.