Abstract: This article provides an in-depth exploration of the advanced manufacturing techniques employed in the production of spur gears. Spur gears play a crucial role in various mechanical systems, and the continuous advancement in manufacturing technologies has significantly enhanced their quality, performance, and efficiency. This comprehensive study covers a wide range of manufacturing processes, materials, and their associated advantages and limitations.
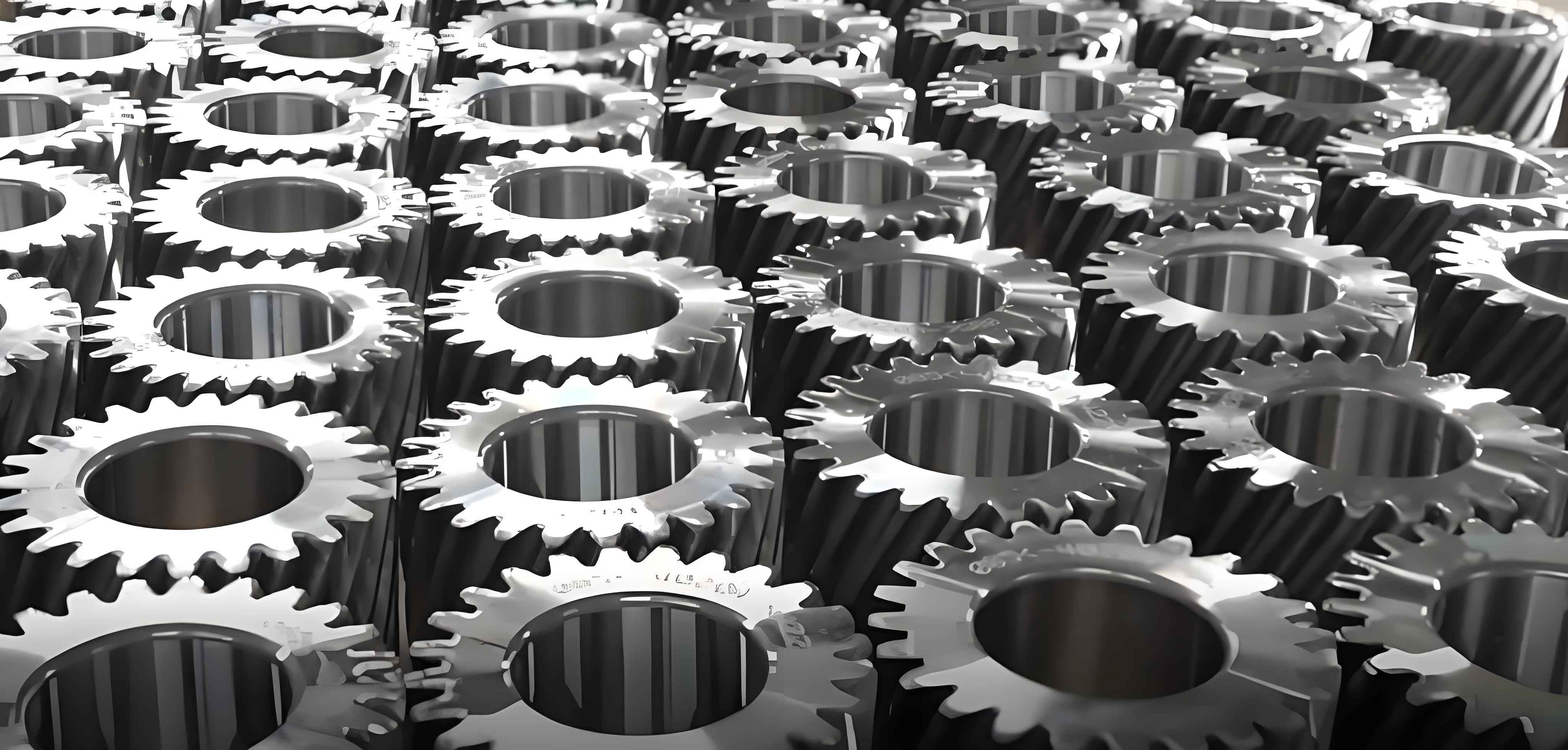
Introduction
Spur gears are one of the most common types of gears used in mechanical power transmission systems. They are characterized by their straight teeth that are parallel to the axis of rotation. The quality and performance of spur gears directly impact the efficiency, reliability, and longevity of the entire mechanical system. Therefore, the development and application of advanced manufacturing techniques are of utmost importance.
Materials Used in Spur Gear Manufacturing
- Steel
- Carbon steel: Commonly used due to its affordability and moderate strength.
- Alloy steel: Offers improved strength and hardness for high-load applications.
- Cast iron
- Gray cast iron: Good damping properties and wear resistance.
- Ductile cast iron: Higher strength and toughness compared to gray cast iron.
- Non-ferrous metals
- Brass: Excellent corrosion resistance and low friction.
- Aluminum alloys: Lightweight and suitable for certain lightweight applications.
Traditional Manufacturing Techniques
- Hobbing
- Principle: A hob cutter is used to generate the gear teeth by rotating the workpiece and the hob simultaneously.
- Advantages: High production efficiency, suitable for mass production.
- Limitations: Limited to certain tooth profiles and sizes.
- Milling
- Principle: The gear teeth are milled using a milling cutter.
- Advantages: Can be used for gears with complex tooth profiles.
- Limitations: Slower production rate and lower accuracy compared to hobbing.
- Shaping
- Principle: A shaping tool reciprocates along the gear blank to form the teeth.
- Advantages: Suitable for small batch production and gears with special tooth shapes.
- Limitations: Lower production efficiency and accuracy.
Advanced Manufacturing Techniques
- Gear Grinding
- Principle: The gear teeth are ground using abrasive wheels to achieve high precision and surface finish.
- Advantages: Excellent accuracy, low surface roughness, and improved gear performance.
- Limitations: Higher cost and longer processing time.
- Electron Beam Melting (EBM)
- Principle: Uses an electron beam to melt and fuse powdered metal layer by layer to create the gear.
- Advantages: Allows for complex geometries, high material utilization, and excellent mechanical properties.
- Limitations: High equipment cost and limited build size.
- Additive Manufacturing (3D Printing)
- Principle: Builds the gear layer by layer using various additive manufacturing processes such as powder bed fusion or material extrusion.
- Advantages: Design freedom, rapid prototyping, and potential for lightweight structures.
- Limitations: Limited material options, surface finish, and mechanical properties compared to traditional methods.
Comparison of Manufacturing Techniques
Technique | Accuracy | Surface Finish | Production Rate | Cost |
---|---|---|---|---|
Hobbing | High | Good | High | Moderate |
Milling | Moderate | Moderate | Low | Moderate |
Shaping | Low | Poor | Low | Low |
Gear Grinding | Very High | Excellent | Low | High |
EBM | High | Good | Low | High |
Additive Manufacturing | Moderate | Poor | Low | High |
Quality Control in Spur Gear Manufacturing
- Dimensional Inspection
- Using coordinate measuring machines (CMM) to measure the gear dimensions.
- Checking tooth profiles, pitch, and tooth thickness.
- Surface Finish Inspection
- Measuring surface roughness using profilometers.
- Ensuring compliance with specified surface finish requirements.
- Material Testing
- Conducting hardness tests to verify material properties.
- Performing tensile and fatigue tests for material strength and durability.
Applications of Advanced Spur Gears
- Automotive Industry
- Transmission systems for improved fuel efficiency and performance.
- Aerospace Industry
- Lightweight and high-precision gears for aircraft engines and control systems.
- Robotics
- Precision gears for robotic joints and actuators.
Future Trends in Spur Gear Manufacturing
- Integration of Multiple Manufacturing Techniques
- Combining traditional and advanced methods to achieve optimal results.
- Development of New Materials
- Research on advanced alloys and composites for enhanced gear performance.
- Smart Manufacturing and Automation
- Use of artificial intelligence and machine learning for process optimization and quality control.
Conclusion
The advanced manufacturing techniques of spur gears have revolutionized the gear production industry. The continuous development and innovation in these techniques have enabled the production of high-quality, high-performance gears that meet the demanding requirements of various applications. However, each manufacturing technique has its own advantages and limitations, and the selection of the appropriate technique depends on factors such as the gear specifications, production volume, and cost constraints. As technology continues to advance, we can expect further improvements and new developments in spur gear manufacturing, opening up new possibilities for mechanical engineering and related fields.
It is important to note that the successful implementation of these advanced techniques requires a combination of skilled operators, advanced equipment, and effective quality control measures to ensure the reliability and performance of the produced spur gears.
The future of spur gear manufacturing holds great promise, and continued research and development in this area will undoubtedly contribute to the advancement of mechanical systems across a wide range of industries.