Gear forging offers several advantages in industrial applications. Here are some key advantages of gear forging:
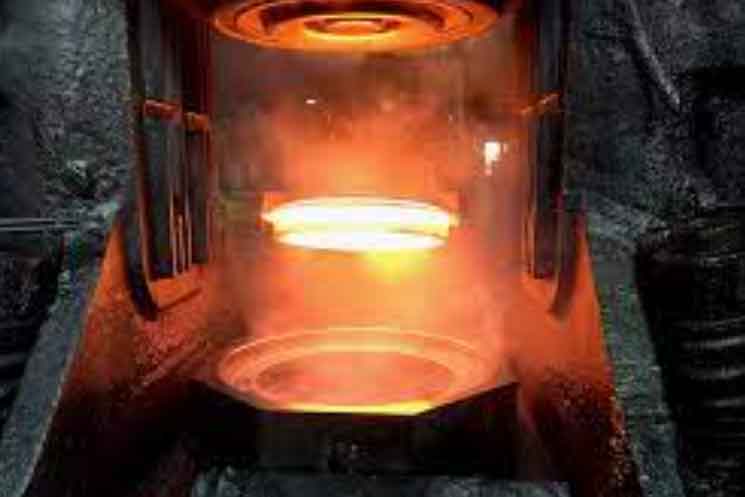
- Strength and Durability: Forged gears exhibit exceptional strength and durability. The forging process aligns the grain structure of the material, resulting in improved mechanical properties, including high tensile strength, toughness, and fatigue resistance. Forged gears can withstand heavy loads, high speeds, and harsh operating conditions, making them suitable for demanding industrial applications.
- Reliability and Performance: The controlled grain flow and absence of internal defects in forged gears contribute to their reliability and performance. The refined grain structure enhances the gear’s resistance to wear, pitting, and fatigue failure, ensuring long service life and consistent performance.
- Improved Material Properties: Gear forging enhances the material properties of the gear. Through the application of heat and pressure, the material is densified, eliminating voids, porosity, and inclusions. This leads to a more uniform and homogeneous material structure, resulting in improved mechanical properties and greater resistance to failure.
- Dimensional Accuracy: Forging allows for excellent dimensional accuracy and consistency in gear manufacturing. The use of precision dies and the controlled deformation process ensure tight tolerances and precise tooth profiles. This enables proper gear meshing, reduced noise, and smooth operation in industrial machinery.
- Cost-Effective Production: Gear forging can be a cost-effective production method, particularly for large-scale manufacturing. The process offers high material utilization, minimizing waste, and shorter production cycles compared to other gear manufacturing methods. This results in cost savings, especially for industries that require a large volume of gears.
- Versatility: Gear forging is versatile and can produce a wide range of gear types, including spur gears, helical gears, bevel gears, and worm gears. It can accommodate various gear sizes, configurations, and application requirements, providing flexibility to meet diverse industrial needs.
- Consistency and Batch-to-Batch Reproducibility: Forged gears offer excellent batch-to-batch reproducibility. The controlled forging process ensures consistent material properties, dimensional accuracy, and tooth profiles across multiple gear production runs. This allows for easier interchangeability and compatibility of gears in industrial machinery.
- Reduced Lead Time: The shorter production cycle of gear forging compared to other manufacturing methods results in reduced lead time. This is particularly advantageous in industries where quick turnaround times and efficient production are critical.
Gear forging is widely used in industries such as automotive, aerospace, heavy machinery, oil and gas, and power generation, where reliable and high-performance gears are essential. The advantages of gear forging contribute to improved equipment reliability, reduced downtime, and enhanced overall productivity in industrial applications.