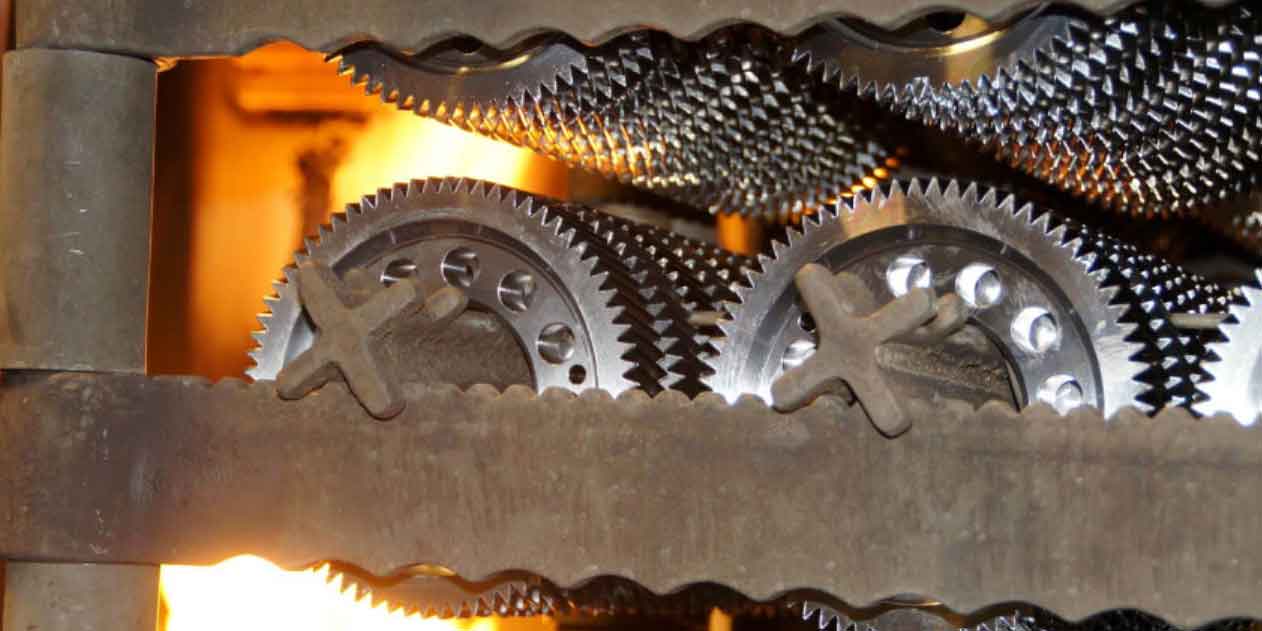
Gear forgings offer several advantages in industrial applications compared to gears produced by other manufacturing methods. Let’s explore some of the key benefits of using gear forgings:
1.Strength and Durability:
As mentioned earlier, gear forgings are known for their exceptional strength and durability. The forging process results in a refined grain structure that enhances the mechanical properties of the gears, making them capable of withstanding high loads, shocks, and cyclic stresses without deformation or failure. This strength and durability are crucial in industrial applications where gears are subjected to heavy-duty operations and harsh environments.
2.Reliability and Performance:
The metallurgical integrity achieved through forging ensures consistent and reliable performance of gear forgings. They exhibit excellent dimensional stability, minimizing the risk of gear misalignment or tooth failure. The absence of internal defects, such as porosity or shrinkage cavities, common in other manufacturing processes, further enhances the reliability of gear forgings. This reliability translates into improved overall performance and reduced downtime in industrial applications.
3.Cost-Effectiveness:
While gear forgings may have higher upfront costs compared to gears produced by casting or machining, their long-term cost-effectiveness becomes evident in industrial applications. The superior strength and durability of gear forgings result in extended service life, reducing the frequency of gear replacements and associated maintenance costs. Additionally, the precise dimensional control achieved through forging reduces the need for secondary machining operations, saving time and expenses.
4.Customization and Design Flexibility:
Gear forgings offer greater design flexibility, allowing for the production of customized gear profiles, tooth forms, and features tailored to specific industrial applications. The forging process enables the creation of complex geometries and intricate shapes that may be challenging to achieve through other manufacturing methods. This customization capability allows gear forgings to be optimized for specific load requirements, efficiency, and noise reduction, resulting in improved overall system performance.
5.Enhanced Fatigue Resistance:
Gears in industrial applications often experience cyclic loading, which can lead to fatigue failure over time. Gear forgings exhibit superior fatigue resistance due to their refined grain structure and absence of internal defects. The controlled deformation during forging ensures a uniform distribution of stress, reducing the likelihood of fatigue cracks and extending the gear’s fatigue life. This enhanced fatigue resistance is particularly beneficial in applications with high cyclic loading or continuous operation.
6.Reduced Lead Times:
Gear forgings can be manufactured with shorter lead times compared to other manufacturing methods. The forging process is generally faster, especially for standard or commonly used gear profiles. This reduced lead time allows for quicker gear production and faster response to industrial demands, minimizing downtime and production delays.
In summary, gear forgings offer advantages such as exceptional strength, durability, reliability, cost-effectiveness, customization, enhanced fatigue resistance, and reduced lead times in industrial applications. These benefits make gear forgings a preferred choice for industries where reliable and high-performance gears are essential for efficient and robust operations.