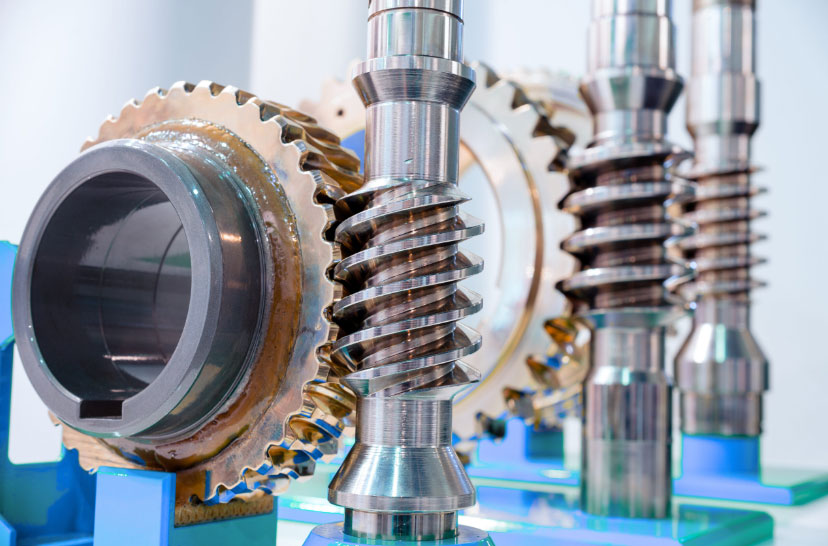
Using custom worm gears in specialized applications offers several advantages that cater to the specific requirements and challenges of those applications. Customization allows engineers to tailor the worm gears to match the unique needs of the machinery, resulting in enhanced performance, efficiency, and reliability. Here are the advantages of using custom worm gears in specialized applications:
1. Precise Motion Control:
Custom worm gears can be designed to achieve specific gear reduction ratios and backlash values, ensuring precise motion control in specialized applications. This level of precision is critical in equipment that requires accurate positioning and controlled movement.
2. High Gear Reduction Ratios:
Worm gears are known for their high gear reduction ratios, and custom worm gears can be optimized to achieve even higher ratios to meet the specialized application’s requirements. This is especially advantageous in machinery that demands significant torque multiplication.
3. Low Backlash:
Minimizing backlash is crucial in specialized applications, and custom worm gears can be designed with low backlash to ensure minimal play between the gear mesh. Low backlash enhances the accuracy and repeatability of the machinery.
4. Optimal Material Selection:
Custom worm gears can be made from materials best suited to the specific application’s demands, considering factors such as load capacity, wear resistance, and environmental conditions. This ensures the gears can withstand the unique operating conditions.
5. Custom Lubrication Solutions:
The lubrication requirements of specialized applications can vary, and custom worm gears can be designed with specific lubrication solutions to ensure smooth operation and extend gear life.
6. Noise and Vibration Reduction:
Custom worm gears can be engineered with features to reduce noise and vibration during operation, making them suitable for machinery where noise levels must be minimized.
7. Compact Design:
Custom worm gears can be designed with a compact footprint, making them ideal for applications with limited space or tight constraints.
8. Integration with Existing Systems:
Custom worm gears can be tailored to match the specifications of existing systems, allowing for seamless integration and compatibility during replacements or upgrades.
9. High Load-Carrying Capacity:
Custom worm gears can be optimized to handle specific loads and torque requirements, ensuring reliable performance in heavy-duty specialized applications.
10. Application-Specific Shaft Arrangements:
Custom worm gears can be designed with specific shaft arrangements to suit the specialized application’s installation and mounting requirements.
11. Application Versatility:
Custom worm gears are versatile and find applications in a wide range of industries, including aerospace, defense, robotics, medical devices, and more.
By utilizing custom worm gears in specialized applications, engineers can fine-tune gear performance to match the precise needs of the machinery. This level of customization results in improved efficiency, reliability, and overall performance, making custom worm gears a valuable choice for specialized and critical applications.