The manufacturing of spiral bevel gear is a sophisticated process that combines art and precision engineering. This process is critical for producing gears that meet high standards of performance, durability, and efficiency, especially in applications where precise power transmission is essential. Here’s an overview of the key aspects involved in the manufacturing of spiral bevel gear:
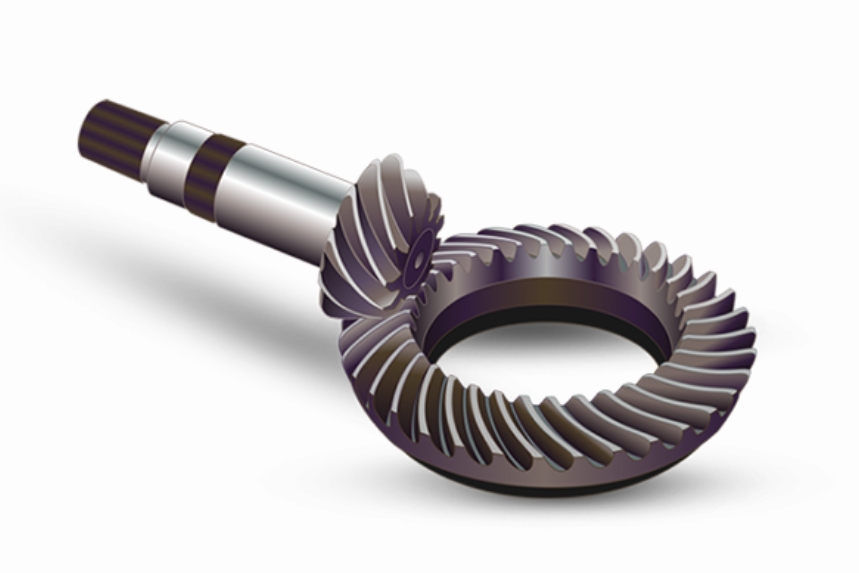
- Design and Modeling: The process begins with detailed design and modeling, often using advanced computer-aided design (CAD) software. Engineers must consider various factors such as the size, tooth geometry, material, and intended application. The design stage is crucial for determining the performance characteristics of spiral bevel gear.
- Material Selection: Choosing the right material is essential for the gear’s performance and longevity. Materials typically used for spiral bevel gear include various grades of steel, aluminum, and even advanced composites. The choice depends on the application’s specific requirements, including strength, weight, and environmental conditions.
- Precision Cutting and Machining: The manufacturing process usually starts with cutting the rough gear shape from the chosen material, often using a milling machine. Precision is key in this stage to ensure that the dimensions are accurate and spiral bevel gear teeth profiles are correctly shaped.
- Tooth Cutting and Gear Grinding: The teeth of spiral bevel gear is then cut to their precise shape. This is typically done using specialized gear-cutting machines. Spiral bevel gear grinding may follow, which refines the tooth surface to a high degree of accuracy and smoothness. This process is critical for reducing noise, vibration, and improving overall efficiency.
- Heat Treatment: After cutting, spiral bevel gear often undergo heat treatment processes like carburizing, hardening, and tempering. These processes enhance the strength and wear resistance of spiral bevel gear, which is essential for ensuring longevity, especially under high-load conditions.
- Surface Finishing: Additional surface treatments, such as coating or shot peening, might be applied to further improve wear resistance, reduce friction, or protect against environmental factors like corrosion.
- Inspection and Quality Control: Quality control is integral throughout the manufacturing process. This includes dimensional checks, material inspections, and testing the gear’s performance characteristics, such as contact pattern, noise level, and vibration.
- Assembly and Integration: In some cases, spiral bevel gears are part of a larger assembly, such as a gearbox. The assembly process must ensure that the gears are perfectly aligned and integrated with other components.
- Lubrication System Integration: For many applications, integrating an effective lubrication system is essential for the gears’ longevity and performance. The design of this system is as crucial as spiral bevel gear themselves.
- Customization: Often, spiral bevel gear is customized for specific applications. This requires flexibility in the manufacturing process to adapt to different designs, sizes, and material requirements.
The art of manufacturing spiral bevel gear lies in the precise balance between technical specifications and the practical application requirements. Every stage, from design to final inspection, requires a high level of expertise and attention to detail, ensuring that the final product performs as intended in its specific application.