Bevel gear alignment is a critical process that ensures the proper functioning, longevity, and efficiency of bevel gear systems. It involves aligning the gear teeth and shafts to minimize misalignment, optimize load distribution, and reduce wear and noise. Here is a detailed guide on the art and science of bevel gear alignment:
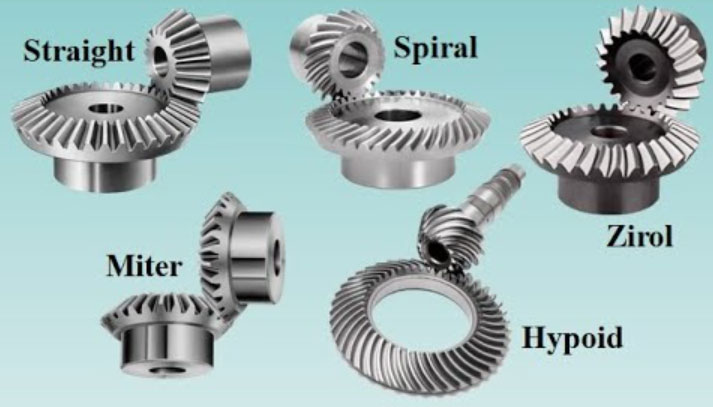
- Understand Gear System Components: Familiarize yourself with the components of the bevel gear system, including the gears, shafts, bearings, housing, and any associated couplings or other transmission elements. Understanding how these components interact and transmit power will help in achieving proper alignment.
- Pre-alignment Preparation: Before starting the alignment process, ensure that the system is clean, free of debris, and properly lubricated. Check for any damages or abnormalities in the gears, shafts, bearings, or housing that could affect alignment. Verify that the gear system is unloaded and properly supported to prevent any unnecessary stress during alignment.
- Establish a Reference Line: Identify a reference line on both the driving and driven gear. This reference line is typically marked on the gear teeth or gear hub and serves as a point of measurement for alignment. The reference line should correspond to the axial centerline of the gear.
- Measure Shaft Centerlines: Accurately measure the centerlines of the driving and driven shafts using precision measurement tools such as dial indicators or laser alignment systems. The centerlines should be parallel for proper alignment. Measure at multiple locations along the shafts to account for any potential shaft runout.
- Check Shaft Angularity: Determine the angular alignment between the driving and driven shafts. Use precision angle measurement tools such as inclinometers or autocollimators to measure the angular offset between the shafts. The goal is to achieve a proper angular alignment to ensure smooth and efficient power transmission.
- Adjust Shaft Position and Angle: Based on the measurements, make adjustments to the shaft positions and angles as necessary. This may involve shimming or adjusting the supports or housings to achieve the desired alignment. Gradually make small adjustments and recheck the measurements until the proper alignment is achieved.
- Check Tooth Contact Pattern: After achieving shaft alignment, check the tooth contact pattern between the driving and driven gears. Apply a suitable marking compound or prussian blue to the gear teeth and rotate the gears through a few revolutions. Inspect the contact pattern to ensure it is evenly distributed across the gear teeth, indicating proper alignment and load distribution.
- Verify Load Distribution: Measure the load distribution across the gear teeth using strain gauges or load cells, if available. The load distribution should be uniform to prevent premature wear and ensure efficient power transmission. If load imbalance is detected, make adjustments to the alignment, shaft positions, or gear modifications as necessary.
- Perform Final Checks and Run Tests: Once alignment adjustments are made, recheck all measurements, including shaft centerlines, angularity, and tooth contact pattern. Conduct a thorough visual inspection of the gear system for any signs of misalignment or abnormalities. Finally, run the gear system under normal operating conditions to verify its performance, noise levels, and load-carrying capacity.
- Document Alignment Data: Maintain accurate records of the alignment process, including initial measurements, adjustments made, and final alignment specifications. This documentation will serve as a reference for future maintenance, troubleshooting, and ensuring ongoing alignment integrity.
Proper bevel gear alignment requires precision, attention to detail, and patience. It is recommended to consult industry standards, equipment manuals, or seek the expertise of alignment specialists when aligning complex or critical bevel gear systems. Regular monitoring and periodic realignment will help maintain the performance and longevity of the gear system.