Spur gears are among the most straightforward and commonly used types of gears, crucial in various mechanical systems for transmitting power and motion. These gears are characterized by their cylindrical shape with teeth that are straight and parallel to spur gear’s axis of rotation. Here’s a primer on the basics of spur gears, covering their design, operation, and applications.
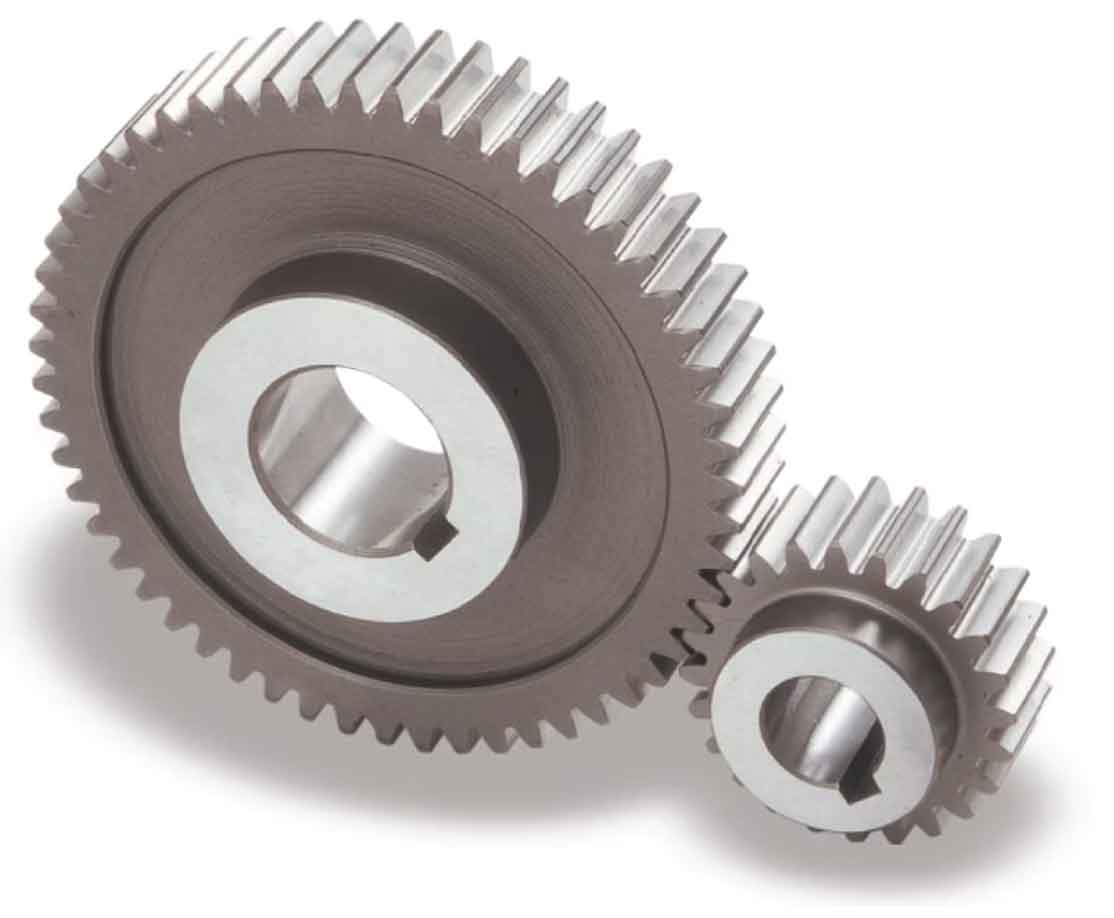
Design
Teeth: The teeth of a spur gears are cut straight and do not angle along the gear’s face. They are designed to fit perfectly with the teeth of another spur gears, allowing for efficient power transmission. The shape of the teeth is often an involute curve, which ensures smooth operation and uniform motion.
Pitch Circle: An important concept in spur gears design is the pitch circle, an imaginary circle that runs through the points where the teeth of two gears effectively engage. The diameter of this circle is used to calculate gear ratios and the mechanical advantage provided by the gear system.
Gear Ratio: The spur gear ratio is determined by dividing the number of teeth on the driven gear by the number of teeth on the driving gear. This ratio is crucial for understanding the mechanical advantage and the speed/torque conversion between spur gears.
Operation
Power Transmission: When two spur gears are meshed, the rotation of the driving gear (input) causes the driven gear (output) to rotate as well. The direction of rotation of the driven gear is opposite to that of the driving gear unless an idler gear is used between them to change direction.
Efficiency: Spur gears are known for their high efficiency, often exceeding 90%. The straight design of the teeth allows for a smooth transfer of power with minimal slippage.
Speed and Torque Conversion: By varying the gear ratio, spur gears can be used to increase torque while reducing speed, or vice versa. This makes them versatile components in machinery requiring precise control over motion and power.
Applications
Machinery: Spur gears are used in a wide range of machinery, including conveyors, pumps, and milling equipment, where straightforward, efficient power transmission is required.
Automotive: In the automotive industry, spur gears are found in transmissions, differential mechanisms, and other systems where reliable power transfer is essential.
Consumer Products: From electric toothbrushes to kitchen appliances, spur gears are integral to the design of many consumer products, enabling compact and efficient mechanisms.
Robotics and Aerospace: In robotics, spur gears are used for precise control of movement. In aerospace, they are used in actuators and control mechanisms, where their efficiency and reliability are crucial.
Advantages and Limitations
Advantages:
- High efficiency and reliability.
- Simple design leading to ease of manufacturing and maintenance.
- Capable of transmitting large amounts of power.
Limitations:
- Can generate noise and vibration, especially at high speeds.
- The straight design of the teeth can lead to stress concentrations and potential failure points.
- Primarily suitable for parallel shafts, limiting their application in systems requiring angular or perpendicular power transmission.
Conclusion
Spur gears are a fundamental element of mechanical engineering, offering a balance between simplicity, efficiency, and versatility. Their straightforward design and the ability to precisely control power transmission make them indispensable in a wide array of applications. Understanding the basics of spur gears is essential for anyone involved in the design or maintenance of mechanical systems.