The manufacturing process of straight bevel gears involves several steps to produce the desired gear geometry and ensure the gears meet the required specifications. Here’s a closer look at the typical manufacturing process of straight bevel gears:
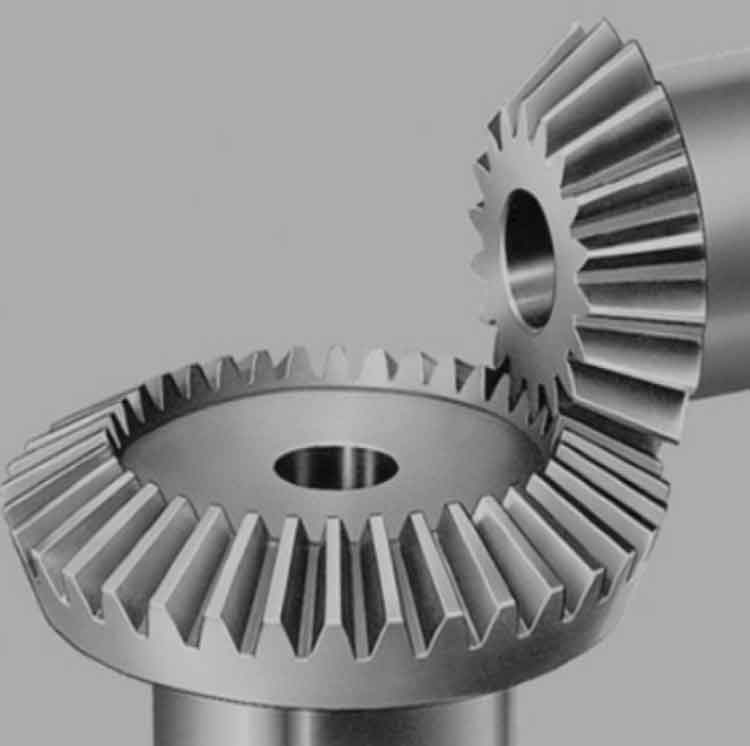
- Gear Design and Modeling:
- The process begins with the design of the straight bevel gears using computer-aided design (CAD) software. Engineers create the gear profile, tooth geometry, and determine other critical dimensions based on the application requirements.
- Material Selection:
- Choose the appropriate material for the gears based on the application’s operating conditions, load requirements, and other factors. Common materials for straight bevel gears include alloy steels, carbon steels, and stainless steels.
- Blank Cutting:
- Start with a blank piece of gear material, typically in the form of a cylindrical or conical shape. The blank is cut to the required dimensions and prepared for further machining.
- Tooth Cutting (Gear Hobbing or Gear Shaping):
- The most common methods for cutting straight bevel gear teeth are gear hobbing and gear shaping:
- Gear Hobbing: In gear hobbing, a specialized tool called a hob is used to cut the gear teeth by generating them gradually as the blank and the hob rotate relative to each other.
- Gear Shaping: In gear shaping, a gear cutter with the negative tooth profile is used to create the gear teeth by removing material from the blank.
- The most common methods for cutting straight bevel gear teeth are gear hobbing and gear shaping:
- Heat Treatment:
- After the tooth cutting process, the gears undergo heat treatment to improve their mechanical properties. Heat treatment involves processes like carburizing, quenching, and tempering to achieve the desired hardness and toughness.
- Tooth Finishing:
- After heat treatment, the gear teeth may undergo finishing operations like grinding or honing to ensure precise tooth profiles and surface quality.
- Backlash Adjustment:
- Proper backlash adjustment is crucial for ensuring smooth meshing between the mating gears. The gear assembly is adjusted to achieve the desired clearance between the gear teeth.
- Inspection and Quality Control:
- The completed straight bevel gears undergo thorough inspection to verify their dimensional accuracy, tooth profile, and other critical parameters. This ensures that the gears meet the required specifications and quality standards.
- Surface Treatment (Optional):
- Depending on the application and gear material, additional surface treatments like coating or plating may be applied to enhance corrosion resistance or reduce friction.
- Assembly:
- Once the gears pass inspection, they are ready for assembly into the gear system or gearbox, where they will transmit power and motion in the intended application.
The manufacturing process of straight bevel gears requires precision engineering, skilled craftsmanship, and adherence to strict quality control measures to produce gears that meet the demanding requirements of various industrial applications. Advanced machining technologies and computer-controlled processes have significantly improved the accuracy and efficiency of manufacturing straight bevel gears.