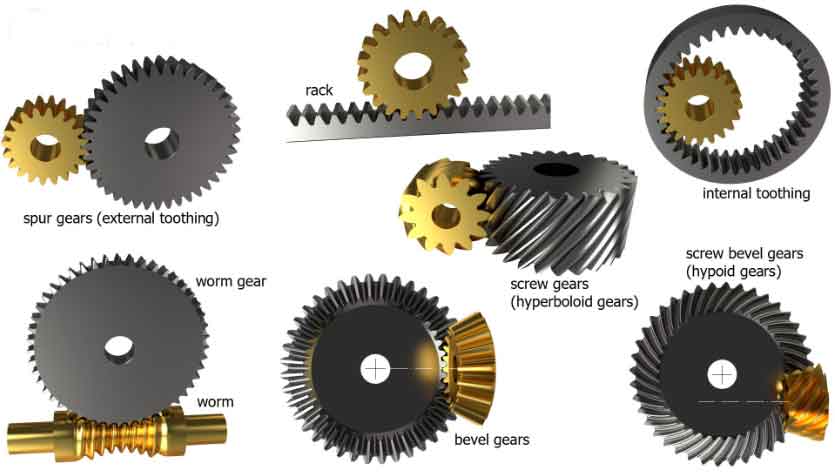
Bevel gears are a type of gear used to transmit power between non-parallel shafts. They have conical-shaped teeth that intersect the gear axis. Bevel gears are classified into several different types based on their specific configurations and applications. Let’s explore the most common types of bevel gears:
1. Straight Bevel Gears:
Straight bevel gears have straight teeth that are cut along the conical surface of the gear. They have the simplest design among bevel gears and are used when the shafts intersect at a 90-degree angle. Straight bevel gears are commonly found in automotive differentials, hand drills, and machine tools.
2. Spiral Bevel Gears:
Spiral bevel gears have curved teeth that are formed in a spiral pattern around the gear. The teeth gradually engage and disengage, resulting in smoother and quieter operation compared to straight bevel gears. Spiral bevel gears are typically used in applications that require high precision and high-speed operation, such as automotive transmissions, aircraft systems, and industrial machinery.
3. Hypoid Gears:
Hypoid gears are a special type of bevel gear that combines the features of spiral bevel gears and offset design. They have curved teeth and an offset between the gear and pinion axes. Hypoid gears are used in applications where the shafts intersect at a non-90-degree angle and high torque transmission is required, such as automotive differentials, heavy machinery, and marine propulsion systems.
Each type of bevel gear offers specific advantages and is suited to different applications based on factors such as load requirements, speed, precision, and noise considerations. Understanding the characteristics and applications of each type of bevel gear is crucial for selecting the appropriate gear for a given system or machinery.