For the measurement of large gears, there are many shortcomings in the off position measurement and in position measurement, which can not fully meet the development needs of large gears; to solve the measurement problems of large gears, especially large gears, will still be the main challenge of gear measurement technology.
The traditional analytical measurement based on the measurement of tooth profile, helix and pitch belongs to the measurement of characteristic line, which is a simplified measurement method, including two meanings. One is to simplify the representation of gear error, and to use a few characteristic lines to represent the whole tooth surface error of gear, which is a statistical method; the other is to simplify the measurement, which belongs to the two-dimensional measurement and the three-dimensional measurement of relative tooth surface, It can greatly improve the measurement efficiency and obtain high measurement accuracy. This simplified measurement method is closely related to gear processing technology. Gear machining mainly includes generating method and forming method. Gear hobbing and gear shaping are typical generating method, gear milling and forming grinding are typical forming methods. For small and medium gears, each step of cutting or grinding feed time is very short. During this period, the machine temperature, tool wear or external environment temperature are relatively stable, and ultimately ensure the consistency of each gear tooth. Therefore, measuring the characteristic lines of these gears can reflect the machining error of the whole gear.
However, for the machining of large gears, especially large gears, considering many factors, especially the milling forming method, the machining cycle is long, the tool wear and external environmental conditions will develop and change in the process of gear machining, and there are also local thermal deformation of gears, which will affect the consistency of teeth. If the gear teeth are still assumed to be consistent, and then only the specific characteristic lines of 3 or 4 teeth in the circumference are measured according to the traditional measurement technology, the overall machining error of the gear cannot be correctly reflected . At the same time, considering that the big gear is mainly used to transmit power, in order to make its operation stable, it will carry out various shape modification processes such as end thinning, drum shape trimming, etc. Based on the 3D representation of gear accuracy with full information , a new parameter reflecting the overall quality of the big gear is proposed to realize the global representation and rapid measurement of the quality of the big gear. This is the general requirement and development direction of the theory and measurement technology of large gear accuracy.
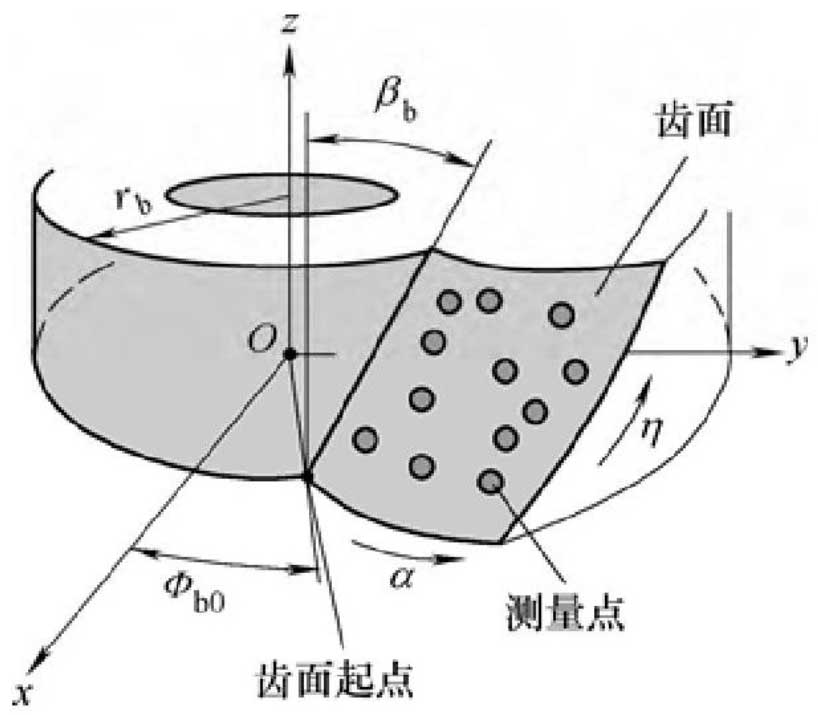
With the application of sensor, information, advanced manufacturing and other technologies in the field of gear measurement, large gear measurement also presents a new development trend in new principles, new methods, measurement traceability and other aspects.