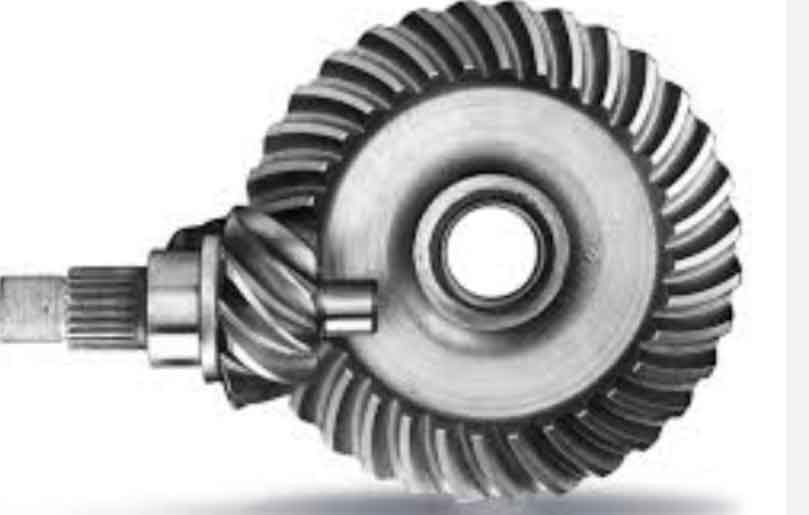
The future of hypoid gear technology holds exciting possibilities, driven by ongoing innovations and advancements in engineering. Here are some key trends and challenges that may shape the development of hypoid gears in the coming years:
1. Enhanced Manufacturing Techniques:
Improvements in manufacturing technologies, such as advanced CNC machining and 3D printing, will likely enhance the precision and efficiency of hypoid gear production. This could result in gears with tighter tolerances, improved surface finishes, and reduced production times.
2. Material Advancements:
The development of new materials and surface treatments will enhance the strength, durability, and wear resistance of hypoid gears. New materials may also provide opportunities for reducing gear weight while maintaining or increasing load-carrying capacities.
3. Simulation and Analysis Tools:
The use of advanced simulation and analysis tools will enable engineers to better understand gear behavior, predict performance under various conditions, and optimize designs for specific applications. This will lead to more efficient and reliable hypoid gear systems.
4. Noise Reduction and Vibration Control:
Engineers will continue to focus on noise reduction techniques in hypoid gears to further minimize gear whine and vibration. By optimizing gear tooth profiles and using advanced lubricants, noise levels can be significantly reduced.
5. Integration with Electric and Hybrid Systems:
As electric and hybrid propulsion systems become more prevalent in automotive and industrial applications, the design and integration of hypoid gears will need to adapt to the specific requirements of these systems. This may include optimizing gear ratios and improving efficiency to meet the demands of electric powertrains.
6. Lightweighting and Sustainability:
In line with global sustainability efforts, the industry may explore methods to lightweight hypoid gears without compromising performance. Utilizing eco-friendly materials and manufacturing processes could become a priority.
Challenges Ahead:
While the future looks promising, there are some challenges that hypoid gear technology may face:
1. Noise and Vibration: Despite significant advancements, minimizing gear noise and vibration remains a challenge. Designing gears that strike the right balance between load-carrying capacity and noise reduction is a complex task.
2. Manufacturing Complexity: The manufacturing process of hypoid gears is more intricate compared to other gear types, leading to higher production costs. Finding ways to reduce manufacturing complexity and costs will be an ongoing challenge.
3. Efficiency Optimization: While hypoid gears offer high torque capacity, there is still room for improvement in terms of efficiency. Optimizing gear tooth profiles and lubrication systems can help address this challenge.
4. Integration with Advanced Systems: As hypoid gears find applications in emerging technologies like robotics and electric vehicles, integrating them seamlessly into these systems will require collaboration and adaptation to new requirements.
The future of hypoid gear technology looks promising, with ongoing advancements in materials, manufacturing techniques, and design methodologies. Overcoming challenges related to noise, vibration, efficiency, and integration will be crucial in ensuring the widespread adoption and success of hypoid gears in various industries.