The future of spiral bevel gear design is filled with exciting innovations and trends driven by advancements in technology, materials, and manufacturing processes. Some of the key developments and trends shaping the future of spiral bevel gears include:
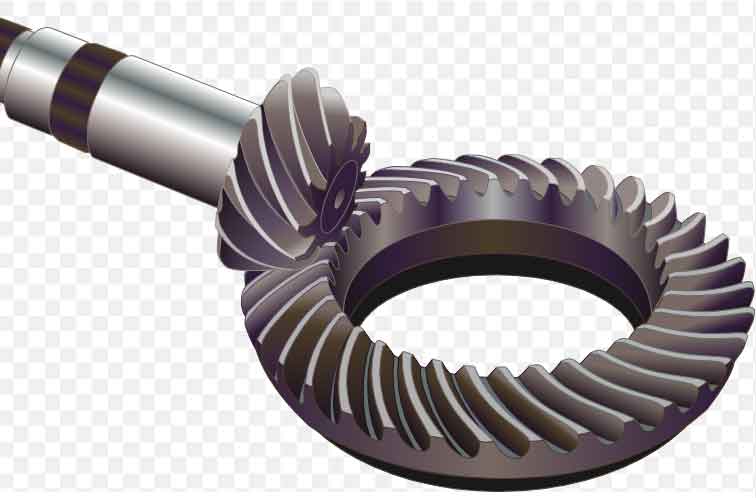
1. Digital Twin and Simulation: Digital twin technology and advanced simulation tools will become more prevalent in spiral bevel gear design. These tools enable engineers to model and analyze gear performance under various operating conditions, optimizing gear design for specific applications and predicting potential issues before physical prototypes are manufactured.
2. Additive Manufacturing (3D Printing): Additive manufacturing, or 3D printing, offers new possibilities for complex gear geometries and customized designs. It allows for the production of spiral bevel gears with unique tooth profiles, optimizing gear performance for specific applications and reducing the need for complex machining operations.
3. Material Advancements: The development of new materials with enhanced strength, durability, and wear resistance will impact spiral bevel gear design. Advanced materials, such as superalloys, composites, and nanomaterials, can lead to more robust and efficient gear systems.
4. Gearbox Compactness: As industries demand more compact and space-efficient gearboxes, spiral bevel gears will continue to be optimized for higher power density while maintaining performance and reliability.
5. Industry 4.0 Integration: Spiral bevel gears will increasingly be integrated into smart and connected systems as part of Industry 4.0 initiatives. This integration will enable real-time monitoring and predictive maintenance, leading to improved gear system performance and reduced downtime.
6. Customization and Rapid Prototyping: The demand for custom-designed gears for specific applications will grow. Rapid prototyping techniques and digital manufacturing will facilitate quick and cost-effective production of customized spiral bevel gears.
7. Noise and Vibration Reduction: Ongoing research and innovation in gear design will focus on further reducing noise and vibration in spiral bevel gears, leading to quieter and more comfortable operation in various applications.
8. Sustainable Gear Design: Sustainability will play a more significant role in gear design. Efforts to reduce energy consumption and improve gear life will be emphasized to achieve environmentally friendly and economically viable gear solutions.
9. Automation in Gear Manufacturing: Automation and robotics will be increasingly integrated into the gear manufacturing process, enhancing precision, consistency, and efficiency in producing spiral bevel gears.
10. Gear Health Monitoring: The implementation of sensor technologies and condition monitoring systems will enable real-time gear health monitoring. This will help identify potential issues and optimize maintenance schedules, ensuring longer gear life and minimizing downtime.
In conclusion, the future of spiral bevel gear design is bright, with an emphasis on digitalization, advanced materials, and sustainable practices. As technology continues to evolve, the development of innovative gear designs and manufacturing techniques will enable the creation of high-performing and reliable spiral bevel gears, meeting the demands of diverse industries and applications.