The helix angle of the forming section of the three working conditions is different. The B2 blank in Table 1 and the 1-3 dies in working conditions are used for rolling experiments. Three test pieces are rolled in each working condition, and the tooth height and pitch error of each working condition are measured and counted. The data is shown in Table 3. The rolling pieces obtained under working conditions 1-3 are shown in Fig. 7 (E), FIG. 9 (a) and Fig. 9 (b), respectively.
From Figure 7 (E), 9 (a), 9 (b) and table 3, it can be seen that the tooth height and pitch error of the workpiece obtained under condition 1 are the largest, a small amount of spiral mark defects appear at the end of the tooth profile, and the tooth height error and pitch error of the workpiece under condition 2 are slightly smaller than those of the workpiece under condition 1; the tooth height and pitch under condition 3 are the most uniform, close to the theoretical value, and there is no spiral mark at the end of the tooth profile section, indicating that the spiral angle of rise under this condition is relatively accurate.
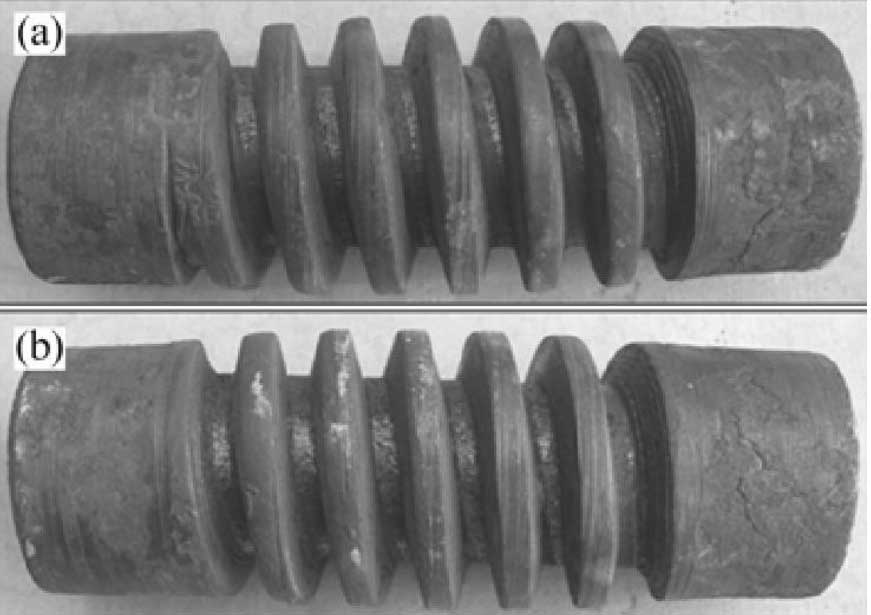
Fig. 7 (E) shows the fixed helix angle raising die. The error of tooth height and pitch of the rolled piece is larger than that of Fig. 9 (a) and Fig. 9 (b), and the spiral mark appears on the rolled piece, which indicates that the helix angle of the die during rolling is not appropriate; FIG. 9 (a) shows full tooth shape, uniform tooth height and pitch, and the spiral mark decreases; FIG. 9 (b) shows the minimum error of tooth height and pitch of the rolled piece, and the improvement of the spiral mark is the best. This is because the profile forming process of rolled piece is the process of metal being pressed in and extruded. The pressing depth is greater than the growth rate of tooth height, the instantaneous radius of profile becomes smaller gradually, and the helix angle changes with the instantaneous radius. The relationship between the instantaneous effective diameter of rolled piece and the profile is as follows:
It can be seen from formula (4): the helix angle is inversely proportional to the diameter, so as the rolling goes on, the helix angle of the rolled piece gradually increases, and finally reaches the helix angle of the rolled piece. That is to say, the helix angle of forming section should be a gradual change curve from 5.2 ° to 5.4 °. The helix angle of working condition 3 changes twice, which is closer to the instantaneous helix curve than the other two working conditions. The obtained rolling piece (Figure 9 (b)) has the smallest error and the smallest defect, meeting the rolling requirements.
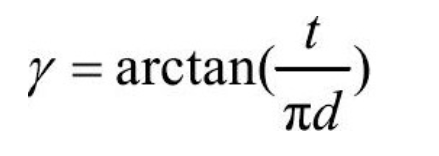
(1) When the round billet is used for cross wedge rolling of spiral gear shaft, the defects of small end tooth height and large pitch are produced due to the outward flow of the metal at the end of the forming section of the rolled piece; when the diameter of the billet is less than the theoretical value, the tooth height of the rolled piece is insufficient; when the diameter of the billet is too large, the distance between the upper and lower dies is not changed, so the amount of die pressing is too large, and part of the metal cannot be contained by the die cavity, Excessive metal is forced out from the edge of the forming section, resulting in serious spiral marks.
(2) When the middle concave billet is used for rolling the spiral gear shaft, the tooth height of the workpiece is relatively uniform. Because the end diameter of the middle concave billet is larger than that of the middle part, and in the spiral tooth forming process, the outward flow of the end metal of the rolled piece is larger than that of the middle metal. When the billet parameters are appropriate, the height of the rolled piece teeth is equal. The experimental results show that when the shape of the blank is concave cone, the tooth height and pitch of the rolled piece are uniform.
(3) The helix angle of the die is an important factor to determine whether there is helix mark at the end of the rolled piece. The helix angle of the rolled piece is inversely proportional to the instantaneous effective radius of the rolled piece. In the process of tooth forming, the instantaneous effective radius of the rolled piece gradually decreases, so the helix angle of the rolled piece gradually increases. When the helix angle corresponding to the instantaneous radius of the rolled piece is adopted, the axial error can be reduced and the helix mark problem can be reduced.