The influence of billets on the forming of rolled pieces is studied. The rolling experiments are carried out on the working mode 1 mould in Figure 3 with the 6 kinds of billets in Table 1, and 3 pieces of each kind of billets are rolled. According to the shape quality of rolled piece, the influence rule of blank on tooth shape is analyzed.
It can be seen from Figure 1 that the tooth height and pitch of the blank are 8.5mm and 12mm respectively. As shown in Figure 7, there are 5 complete tooth profiles and 6 cogs for each rolled piece in the experimental part. The tooth height and pitch of each rolled piece are measured from one end to make the curve of tooth height and pitch change, as shown in Figure 8. The maximum error, the minimum error and the average error of the tooth height and the pitch of each rolling piece are calculated by formula (2).
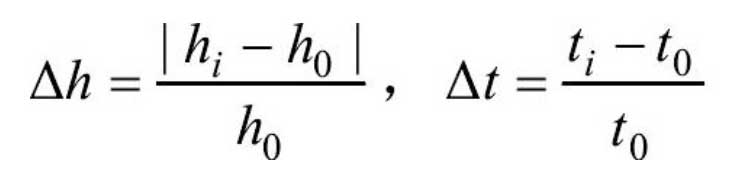
Where: H0 is the theoretical pitch; hi is the actual pitch; t0 is the theoretical pitch; Ti is the actual pitch.
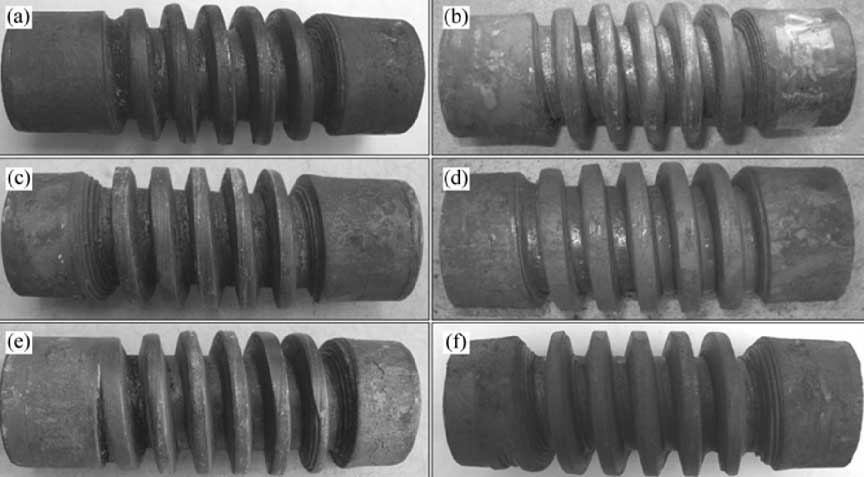
It can be seen from Fig. 8 that the common characteristics of A1 ~ A3 rolling piece under working condition are: the tooth height of the end teeth 1 and 5 of the tooth profile segment is lower than the middle tooth height, and the end pitch is greater than the middle pitch. This is because the blank of three working conditions is round, the die hole at the edge of the tooth section is closed inside, the outer layer is open, the end metal is squeezed by the die tooth wall and flows out more, resulting in the end tooth height is significantly lower than the middle tooth height, and the end screw pitch becomes larger.
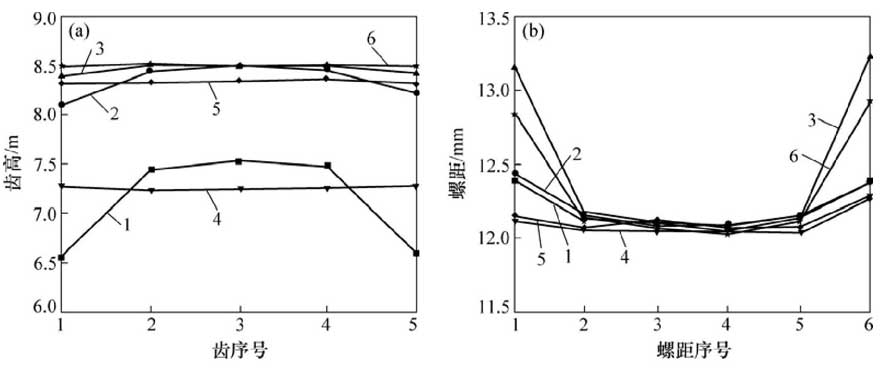
Combined with Figure 7 and figure 8, it can be concluded that the tooth height under condition A1 is quite different from the design value. Table 2 shows that the maximum error, minimum error and average error of tooth height under condition A1 are 25.29%, 9.31% and 16.12% respectively. This is because the diameter of the billet is too small, less material is pressed in and extruded, and the tooth profile is not rolled out high enough. In case A2, the tooth height becomes larger and the error of tooth height becomes smaller, but the end tooth height is significantly lower than the middle tooth height. The diameter of the billet basically meets the size requirements. The maximum error is 4.47%, and the average error is 1.23%. It can be seen from Fig. 7 that there is obvious spiral mark defect in the tooth profile of the rolling piece. This is because the billet of the rolling piece is too large. When the spiral tooth is formed, the volume of the rolled piece pressed by the die is larger than the volume of the cavity for metal flow, so that part of the metal cannot be contained by the cavity of the die. This part of the metal is forced out along the axial direction of the die, resulting in obvious spiral mark defect at the end of the tooth profile, And the end pitch becomes larger, and the pitch error reaches 13.75%.
The results of the above three working conditions show that: when rolling round billets with spiral teeth, the edge tooth height of the rolled piece is low and the pitch is large; when the diameter is too small, the tooth height is not formed enough, and the pitch of the tooth segment edge becomes larger and the spiral mark defects are produced.
It can be seen from Fig. 7, FIG. 8 and table 2 that when the blank adopts the concave cone blank and the die adopts working conditions B1, B2 and B3, the tooth height of the rolled piece is relatively uniform, the tooth height error of working condition B1 is relatively large, the tooth height error is close to 15%, and the tooth height error of working conditions B2 and B3 is very small, indicating that the concave cone blank can improve the uneven tooth height defect of the rolled piece. At the same time, the pitch error of the rolled piece is small, because the diameter of the two ends of the billet is larger than the middle diameter when the concave cone billet is used for rolling, because the outward flow of the metal end is larger than the flow of the internal metal during rolling, the defects of unequal end tooth height caused by the uneven metal flow can be compensated by the concave cone shape of the billet, and finally the uniform tooth height is formed.

The blank diameter is too small, and the height of tooth profile is not filled fully; the blank diameter is too large, resulting in the surplus material which can not be contained by the mold cavity, and the defects such as too large pitch and spiral mark appear at both ends of the tooth profile section of the rolled piece. Only by choosing the appropriate billet diameter, can the workpiece with relatively balanced tooth height and pitch be rolled. By analyzing the experimental results, the empirical formula (3) of billet diameter D for rolling ideal workpiece is obtained. The diameter of such billet is between condition 2 and condition 3. The profile and pitch of the workpiece are uniform and the quality of the workpiece is good.