The manufacturing process of hypoid gears involves several stages, starting from the initial design and ending with the final production. Here is an overview of the typical steps involved in manufacturing hypoid gears:
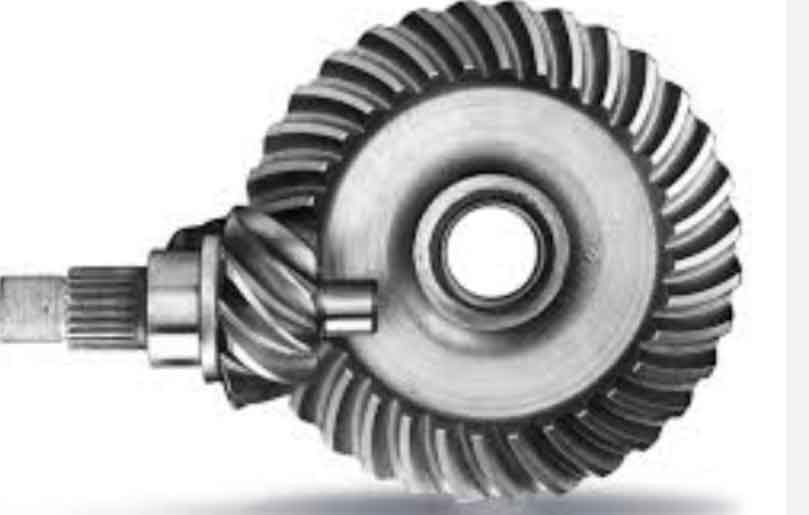
- Design: The process begins with the design of the hypoid gear. This includes determining the gear specifications such as tooth profile, size, ratio, and load requirements. Computer-aided design (CAD) software is commonly used to create a 3D model of the gear.
- Gear Cutting: Once the design is finalized, the gear cutting process begins. Hypoid gears are typically produced using specialized gear cutting machines such as Gleason or Klingelnberg machines. These machines use a cutting tool with a specific shape to generate the gear teeth.
- Gear Blank Production: Before the gear cutting process, gear blanks need to be produced. Gear blanks are typically made from steel or other suitable materials. The gear blank is a cylindrical piece of material that will eventually be shaped into the final gear.
- Roughing: In the roughing stage, the gear cutting machine removes excess material from the gear blank to bring it closer to the final shape. This process is done to reduce the machining time required for the finishing stage.
- Finishing: In the finishing stage, the gear teeth are precisely machined to achieve the desired tooth profile and surface finish. The gear cutting machine generates the exact shape and dimensions of the teeth based on the design specifications.
- Heat Treatment: After the gear teeth are machined, heat treatment is often performed to enhance the hardness and strength of the gear. This involves heating the gears to a specific temperature and then rapidly cooling them through processes such as quenching.
- Gear Inspection: Once the gears are heat-treated, they undergo a thorough inspection process to ensure they meet the required quality standards. Various inspection techniques, such as coordinate measuring machines (CMM), gear analyzers, and visual inspection, are used to check the dimensions, tooth profile, and other critical parameters.
- Gear Finishing Operations: After inspection, the gears may undergo additional finishing operations, such as grinding, honing, or lapping, to achieve even higher precision and improve the surface finish.
- Gear Assembly: In some cases, hypoid gears are assembled into gearboxes or other mechanical systems. This involves fitting the gears with bearings, shafts, and other components to create the complete gear assembly.
- Quality Control: Throughout the entire manufacturing process, quality control measures are implemented to ensure the gears meet the required specifications. This includes regular inspections, measurements, and testing to verify the gear’s performance, durability, and reliability.
- Packaging and Distribution: Once the gears pass the quality control checks, they are packaged and prepared for distribution to customers or other manufacturers for further integration into end products.
It’s important to note that the specific details of the manufacturing process can vary depending on the manufacturer, equipment used, and the intended application of the hypoid gears. The steps mentioned above provide a general overview of the typical process involved in manufacturing hypoid gears.