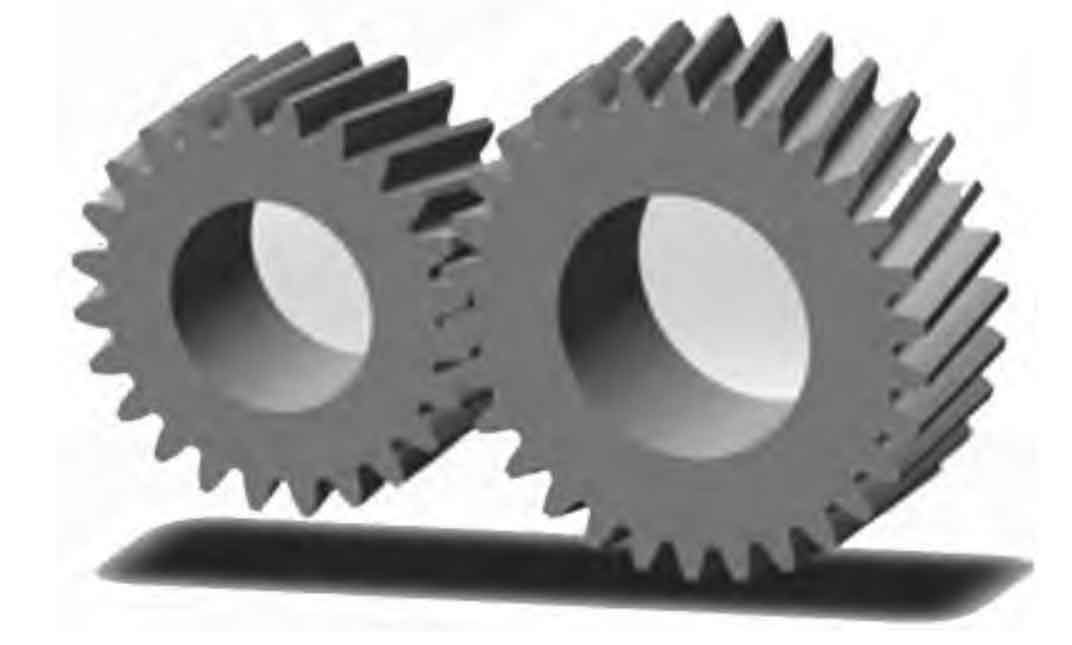
Helical gear is type of cylindrical gear with teeth that are cut at an angle to the gear’s axis, unlike spur gear which have teeth parallel to the axis. This design difference gives helical gear several advantages and some unique characteristics. Let’s explore their design, function, and applications in depth.
Design Features
- Tooth Angle (Helix Angle): The key feature of helical gear is their helix angle, which is the angle between the gear’s teeth and the gear’s axis. This angle affects the gear’s performance, including its load capacity and noise level.
- Handedness: Helical gear come in either right-handed or left-handed configurations, depending on the direction in which the teeth are angled. Some applications use pairs of helical gear with opposite handedness.
- Overlap Ratio: Unlike spur gear, the teeth of helical gear overlap for a part of their rotation, which means more than one tooth is in contact during operation. This overlap reduces the load on individual teeth, leading to quieter operation and increased load capacity.
- Pressure Angle: This is the angle at which the gear teeth exert force onto each other. A larger pressure angle can increase the helical gear’s load capacity but may also increase stress and noise.
Function and Advantages
- Smooth Operation: The overlapping of teeth allows for smoother and quieter operation compared to spur gear. This is crucial in applications where noise reduction is important.
- Higher Load Capacity: The load is distributed over multiple teeth, which reduces the stress on each tooth and allows helical gear to handle more power.
- Reduced Vibration: The gradual engagement and disengagement of the teeth cause less vibration, enhancing the longevity of helical gear and the machinery.
- Thrust Forces: Helical gears produce axial thrust forces. This requires bearings that can handle these forces, and this is an important consideration in their design.
- Orientation Flexibility: Helical gear can be used in both parallel and crossed gear arrangements, unlike spur gear which can only be used in parallel arrangements.
Applications
- Automotive Transmissions: They are commonly used in car transmissions for their smooth operation and high load capacity.
- Machinery: In machines where noise reduction is critical, like printing presses and industrial equipment.
- High-Speed Applications: Due to their smoother operation, they are preferred in high-speed applications.
Design Considerations
- Material Selection: The material used for helical gear must be chosen based on the application, considering factors like strength, wear resistance, and environmental conditions.
- Lubrication: Proper lubrication is crucial for helical gear, especially since they generate axial thrust.
- Manufacturing Precision: The precision in manufacturing helical gear impacts their efficiency and noise level. High precision is required for optimal performance.
Challenges
- Complex Manufacturing: The angled teeth make manufacturing more complex and expensive than spur gear.
- Axial Thrust: The design must account for the axial thrust generated by the helical design, which can increase the load on bearings.
Conclusion
Helical gear offer several advantages over spur gear, including smoother operation, higher load capacity, and versatility in application. However, their design and manufacturing are more complex, and they require careful consideration of the axial forces they generate. They are widely used in various industries, particularly where noise reduction and high load capacity are essential.