Gear hobbing is a crucial process in the production of industrial gears, serving a pivotal role in various industries where precise and efficient power transmission is essential. This article explores the significant role of gear hobbing in industrial gear production, highlighting its advantages, applications, and impact on the overall performance of machinery and equipment.
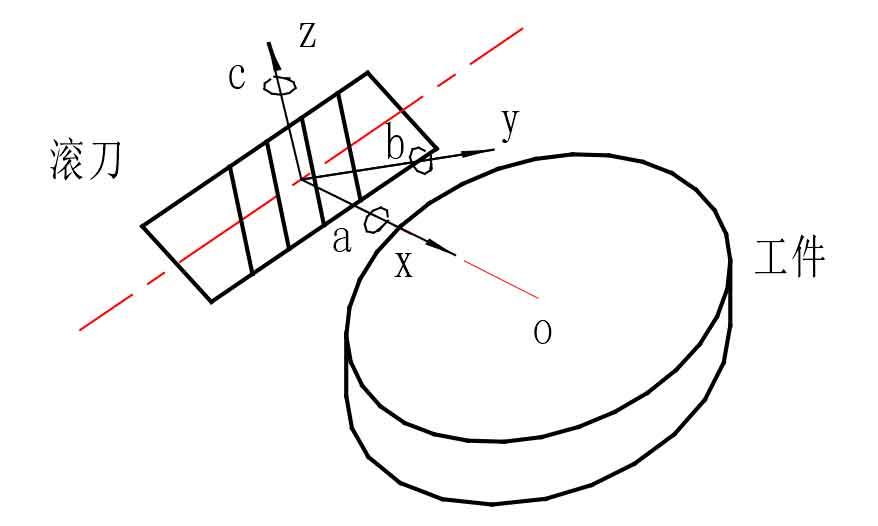
- Advantages of Gear Hobbing:
- Precision: Gear hobbing allows for the production of gears with high precision and accuracy, ensuring proper tooth profiles and consistent gear quality. This precision is vital for smooth gear meshing and reliable power transmission.
- Efficiency: Gear hobbing is an efficient process that enables the production of multiple gear teeth simultaneously. This results in reduced machining time and increased productivity, making it ideal for large-scale gear manufacturing.
- Versatility: Gear hobbing can produce various types of gears, including spur gears, helical gears, and worm gears, making it a versatile manufacturing method suitable for different applications and industries.
- Applications in Various Industries:
- Automotive Industry: Gear hobbing plays a critical role in automotive gear production, used in applications such as transmissions, differentials, and steering systems. The high precision and efficiency of gear hobbing ensure optimal performance and durability of automotive gears.
- Aerospace Industry: Gear hobbing is vital in the aerospace sector for producing gears used in aircraft engines, landing gear systems, and auxiliary power units. The reliability and precision of gear hobbed aerospace gears are crucial for safe and efficient aircraft operation.
- Industrial Machinery: Gear hobbing finds extensive use in industrial machinery, including heavy machinery, construction equipment, and machine tools. It is employed in gears used for power transmission, speed reduction, and torque generation, ensuring smooth operation and increased equipment efficiency.
- Wind Power Industry: Gear hobbing is instrumental in the production of gears used in wind turbine systems. These gears, such as those found in the gearbox, enable the conversion of wind energy into electricity. The precision and durability of gear hobbed wind turbine gears are essential for maximizing energy generation and minimizing maintenance requirements.
- Gear Performance and Reliability:
- Load Distribution: Gear hobbing ensures accurate tooth profiles and proper load distribution across the gear teeth. This enables efficient power transmission, minimizing stress concentration and wear, and increasing gear longevity.
- Gear Tooth Strength: Gear hobbing allows for the creation of gear teeth with optimal strength and geometry, ensuring resistance to bending, fatigue, and tooth breakage. This results in reliable gear performance and extended gear life.
- Noise and Vibration Control: Gear hobbing produces gears with precise tooth profiles, minimizing gear meshing noise and vibration. The smooth and accurate gear engagement reduces noise levels and enhances the overall comfort and performance of machinery.
Gear hobbing plays a vital role in industrial gear production, offering precise and efficient manufacturing of gears for various industries. Its advantages, including precision, efficiency, and versatility, make it a preferred method for producing high-quality gears used in automotive, aerospace, industrial machinery, and wind power applications. The precise tooth profiles, optimal load distribution, and reliable gear performance achieved through gear hobbing contribute to the efficiency, durability, and overall performance of machinery and equipment. As technology advances, gear hobbing techniques and equipment will continue to evolve, further enhancing the role of gear hobbing in industrial gear production.