Heat treatment plays a crucial role in preventing bevel gear failure by improving the mechanical properties and durability of the gear. Bevel gears are commonly used in various applications, including automotive differentials, industrial machinery, and aerospace systems. The heat treatment process enhances the gear’s strength, toughness, and resistance to wear, thereby reducing the risk of failure. Here are some key ways in which heat treatment contributes to bevel gear failure prevention:
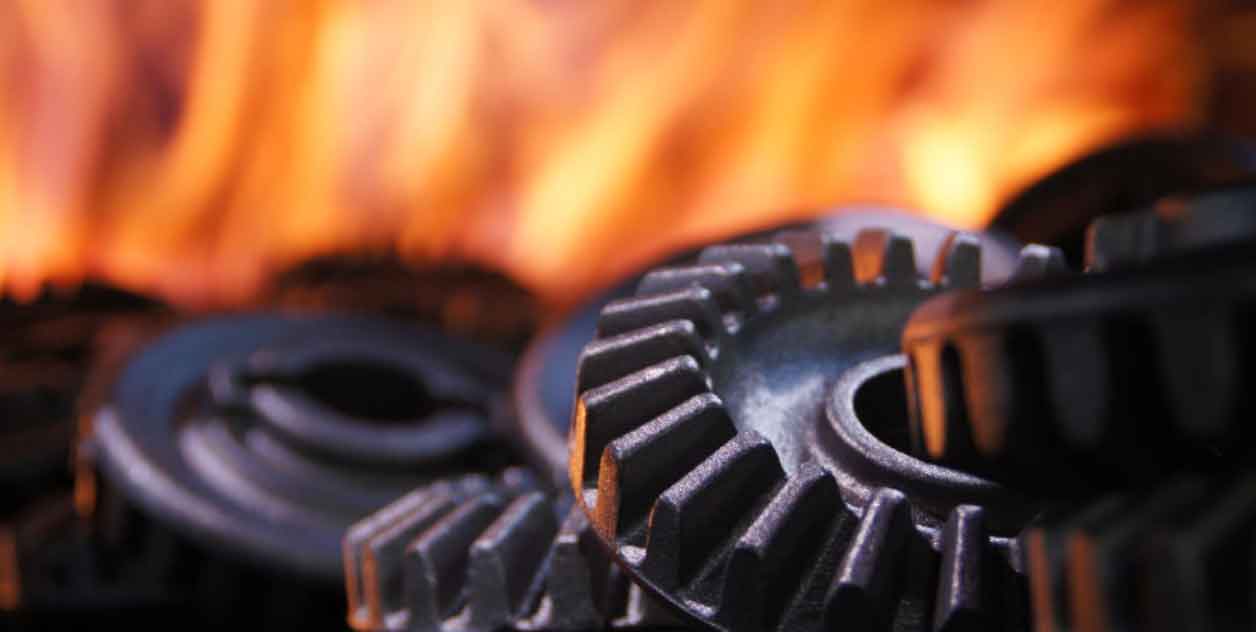
- Surface hardening: Bevel gears undergo a surface hardening process, typically carburizing or nitriding. Carburizing involves diffusing carbon into the gear material’s surface, forming a high-carbon layer that increases hardness. Nitriding, on the other hand, introduces nitrogen into the surface, forming a hardened nitride layer. Both processes significantly improve the wear resistance and fatigue strength of the gear teeth, reducing the likelihood of surface failure.
- Core toughness: Heat treatment not only hardens the gear’s surface but also improves the toughness of the gear’s core. Through appropriate tempering, the gear’s hardness is balanced with sufficient toughness, ensuring it can withstand heavy loads, shocks, and cyclic stresses without catastrophic failure. This is particularly important in bevel gears that experience high loads and bending stresses.
- Residual stress relief: Heat treatment helps relieve the residual stresses induced during the manufacturing process. Machining and forming operations can introduce residual stresses in the gear material, which can lead to premature failure if not addressed. Heat treatment, especially tempering, reduces these stresses and improves the gear’s dimensional stability and resistance to stress-related failures.
- Metallurgical structure refinement: Heat treatment refines the microstructure of the gear material, enhancing its mechanical properties. Through controlled heating and cooling cycles, the grain size and distribution of phases in the gear material are optimized. This results in improved strength, hardness, and toughness, reducing the susceptibility to fatigue, bending, and contact-related failures.
- Wear resistance: Bevel gears often operate under conditions of high contact stress and sliding friction. Heat treatment can increase the gear’s wear resistance by forming a hardened surface layer or introducing wear-resistant alloying elements during the heat treatment process. This helps minimize wear, pitting, and surface fatigue, leading to extended gear life.
It is important to note that the heat treatment parameters and techniques used for bevel gears may vary depending on factors such as the gear material, application, and design requirements. Proper control and optimization of the heat treatment process are essential to ensure that the gear exhibits the desired properties and performance, thereby reducing the risk of failure and ensuring reliable operation in heavy-duty and high-load environments.