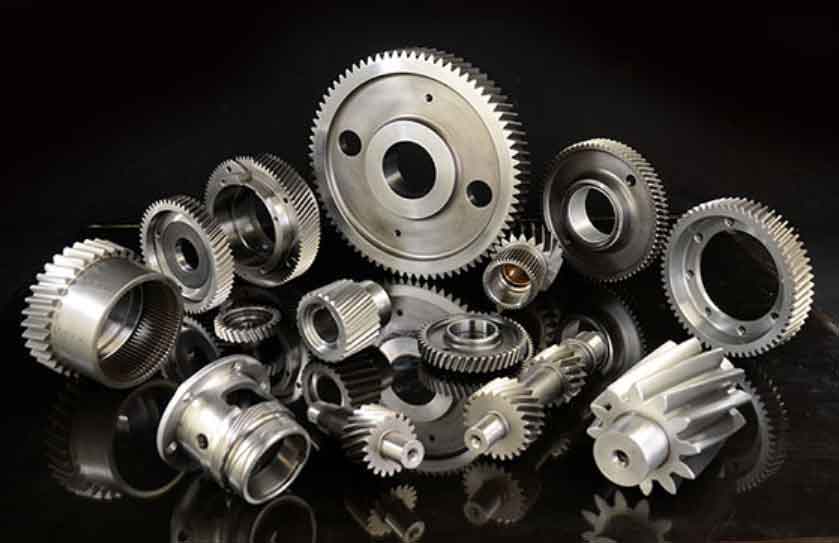
Helical gears play a crucial role in industrial machinery and are widely used in various applications due to their unique design and performance characteristics. They are a type of cylindrical gears with teeth that are cut at an angle to the gear axis in a helix shape. This helical arrangement of teeth offers several advantages over other gear types, making them suitable for a wide range of industrial applications.
- Smooth and Quiet Operation: One of the primary advantages of helical gears is their ability to provide smooth and quiet operation. The gradual engagement of helical teeth results in a more gradual and continuous transfer of power, reducing noise and vibration compared to spur gears.
- High Load-Carrying Capacity: The helix angle of the teeth allows for greater tooth engagement at any given time, which enhances the load-carrying capacity of helical gears. This makes them suitable for applications where heavy loads and high torque transmission are required.
- Efficiency: Helical gears generally have higher efficiency than other types of gears, such as worm gears. The greater tooth engagement and smooth operation contribute to lower frictional losses and increased power transmission efficiency.
- Versatility and Adaptability: Helical gears can be used for various applications, including parallel shaft, crossed shaft, and even right-angle drives with the use of helical bevel gears. This versatility makes them a popular choice in a wide range of industrial machinery.
- Reduced Wear and Tear: The gradual tooth engagement and larger contact area of helical gears distribute the load more evenly, leading to reduced wear on the gear teeth and prolonged gear life.
- Angular Misalignment Tolerance: Helical gears can tolerate a certain degree of angular misalignment between shafts, making them more forgiving in real-world applications where perfect alignment might be challenging.
Applications of Helical Gears in Industrial Machinery:
- Gearboxes and Transmissions: Helical gears are commonly used in gearboxes and transmissions for various industrial machinery, such as automobiles, construction equipment, and industrial power plants.
- Rotary Equipment: Helical gears are employed in various rotary equipment, including pumps, compressors, and turbines, to transmit power and control rotational speed.
- Printing Machinery: Printing presses often use helical gears for smooth and precise paper feeding and print roll movement.
- Mining Equipment: Heavy-duty mining machinery, such as crushers and conveyors, utilize helical gears for their robustness and load-carrying capabilities.
- Steel Rolling Mills: Helical gears are used in steel rolling mills to drive and control the rolling process.
Performance Analysis of Helical Gears:
- Load Analysis: Engineers analyze the applied loads on the gear teeth to ensure that they stay within the allowable limits to prevent premature failure.
- Stress Analysis: Finite Element Analysis (FEA) is commonly used to determine the stress distribution in the gear teeth and ensure they are within the material’s limits.
- Noise and Vibration Analysis: Helical gears are analyzed for noise and vibration levels to ensure smooth and quiet operation, especially in precision machinery and applications with strict noise requirements.
- Efficiency Analysis: Engineers evaluate the efficiency of helical gear pairs to optimize power transmission and minimize energy losses.
- Wear Analysis: Wear patterns on the gear teeth are studied to optimize gear design and material selection for improved gear life.
- Temperature Analysis: Thermal analysis helps understand heat generation and dissipation in the gear system, which is crucial for high-speed or heavy-load applications.
Overall, helical gears play a vital role in industrial machinery, providing efficient and reliable power transmission while minimizing noise and wear. Proper design, analysis, and maintenance are essential to ensuring their optimal performance and longevity in various industrial applications.