Spiral bevel gears play a crucial role in modern engineering across various industries due to their unique characteristics and capabilities. Here’s a breakdown of their significance:
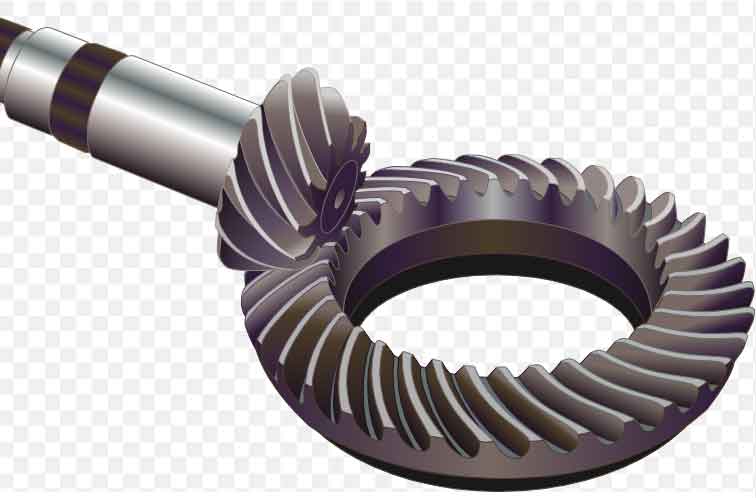
1. Power Transmission Efficiency:
- 90-Degree Angle Transmission: Spiral bevel gears are commonly used to transmit power between shafts that intersect at a 90-degree angle, which is a common requirement in many mechanical systems.
- High Efficiency: Their tooth geometry allows for smoother engagement and reduced friction compared to straight bevel gears, leading to higher efficiency in power transmission.
2. Quiet and Smooth Operation:
- Curved Tooth Profile: The spiral-shaped teeth of these gears enable gradual engagement, resulting in quieter and smoother operation compared to straight-toothed counterparts.
- Reduced Vibration: The improved contact ratio and gradual tooth engagement help in minimizing vibration and noise, making them suitable for applications where noise reduction is essential, such as automotive differentials and industrial machinery.
3. Versatility and Adaptability:
- Variable Gear Ratios: Spiral bevel gears can be designed to achieve a wide range of gear ratios, making them adaptable to different speed and torque requirements in various applications.
- Customizable Designs: They can be manufactured in a variety of sizes, configurations, and materials to suit specific application needs, offering flexibility in design and integration.
4. High Load Capacity and Durability:
- Uniform Load Distribution: The spiral tooth geometry allows for a higher contact ratio compared to straight bevel gears, distributing the load more evenly across the teeth. This results in increased load capacity and better resistance to wear and fatigue.
- Suitable for Heavy-Duty Applications: Their robust design and ability to handle high loads make spiral bevel gears suitable for heavy-duty applications such as industrial machinery, mining equipment, and aerospace systems.
5. Precision Engineering and Manufacturing:
- Advanced Manufacturing Techniques: Precision machining and computer-aided manufacturing (CAM) technologies allow for the production of high-quality spiral bevel gears with tight tolerances and excellent surface finishes.
- Quality Control: Strict quality control measures ensure the dimensional accuracy, tooth profile integrity, and material properties of spiral bevel gears, enhancing their reliability and longevity.
6. Wide Range of Applications:
- Automotive Industry: Spiral bevel gears are commonly used in automotive differentials, transfer cases, and rear axle drives due to their efficiency, durability, and compact design.
- Aerospace and Defense: They are utilized in aircraft engines, helicopter rotor systems, and military vehicles for their high-load capacity, reliability, and performance under extreme conditions.
- Industrial Machinery: Spiral bevel gears find applications in various industrial machinery such as machine tools, printing presses, and packaging equipment, where precise power transmission and smooth operation are critical.
In summary, spiral bevel gears are indispensable components in modern engineering, offering efficient power transmission, quiet operation, durability, and adaptability across a wide range of applications in automotive, aerospace, industrial, and other industries. Their versatility and performance make them integral to the functioning of numerous mechanical systems and equipment.