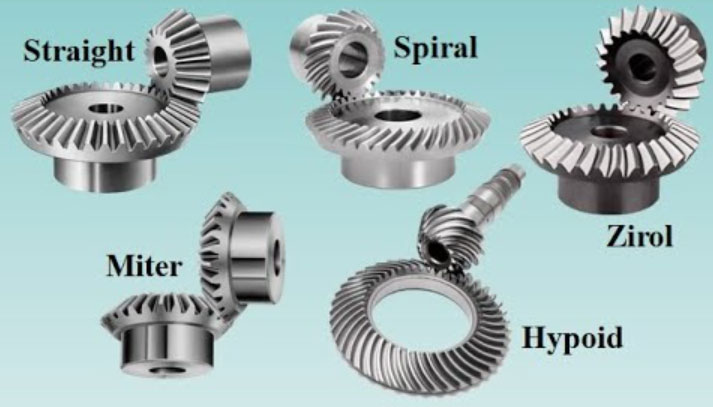
The science behind bevel gears involves a geometrical analysis of their design and tooth profiles, which determines their performance characteristics and capabilities. The geometry and tooth profiles of bevel gears play a crucial role in efficient power transmission, smooth operation, and load-carrying capacity. Let’s delve into the science behind bevel gears:
1. Tooth Geometry:
Bevel gears have conical shapes and intersecting axes, allowing them to transmit motion and torque between non-parallel shafts. The tooth geometry of bevel gears involves parameters such as the number of teeth, pitch diameter, pitch angle, tooth thickness, and helix angle. These parameters are critical for determining the gear ratio, contact pattern, and overall performance of the gears.
2. Pitch Diameter and Pitch Angle:
The pitch diameter of a bevel gear is the imaginary circle around which the gear teeth are defined. It determines the gear ratio and is crucial for maintaining proper tooth engagement and motion synchronization. The pitch angle is the angle between the pitch diameter and the gear axis. It influences the force distribution, load-carrying capacity, and contact characteristics of the gear teeth.
3. Tooth Profiles:
The tooth profiles of bevel gears define the shape of the gear teeth and play a vital role in efficient power transmission and smooth operation. The most common tooth profiles for bevel gears are straight, spiral, and hypoid. The tooth profile affects the gear’s contact pattern, load distribution, noise generation, and efficiency.
4. Straight Bevel Gears:
Straight bevel gears have straight tooth profiles that intersect with the gear axis. They are commonly used in applications with low to moderate speed and torque requirements. Straight bevel gears provide efficient power transmission but may generate more noise and vibration compared to other tooth profiles.
5. Spiral Bevel Gears:
Spiral bevel gears have curved tooth profiles that spiral around the gear axis. The spiral shape allows for gradual tooth engagement, resulting in smoother operation, reduced noise, and improved load distribution compared to straight bevel gears. Spiral bevel gears are suitable for applications that require higher speeds, heavier loads, and quieter operation.
6. Hypoid Bevel Gears:
Hypoid bevel gears have curved tooth profiles similar to spiral bevel gears but with an offset in the gear axes. This offset enables a larger contact area and improved load-carrying capacity. Hypoid bevel gears are commonly used in applications with high torque requirements and where the axes of the input and output shafts are not intersecting.
7. Tooth Contact Pattern:
The tooth contact pattern is the specific area where the teeth of two bevel gears come into contact during operation. A well-distributed and properly aligned contact pattern ensures efficient power transmission, even load distribution, and minimal wear. Achieving a proper contact pattern requires accurate tooth geometry, precise manufacturing, and proper alignment of the gear axes.
Geometrical analysis and tooth profile design are crucial in optimizing the performance of bevel gears. Engineers use mathematical calculations, computer-aided design (CAD) software, and simulation tools to analyze and optimize the gear geometry, tooth profiles, and contact patterns. By understanding the science behind bevel gears and applying precise geometrical analysis, engineers can design bevel gears that provide efficient power transmission, smooth operation, and reliable performance in various applications.