Precision forging is a manufacturing process used to shape metal components with high accuracy and precision. It involves applying extreme forces to deform and shape a heated metal billet into a desired shape. The process offers several benefits over other conventional metalworking techniques such as casting or machining. Let’s explore the science behind precision forging and understand its process and benefits.
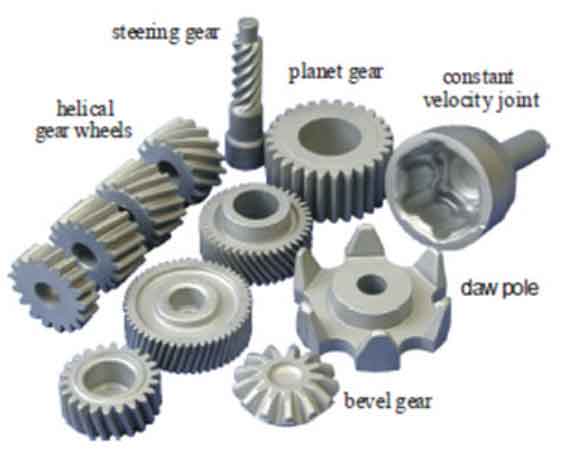
Process of Precision Forging:
- Billet Heating: The first step in precision forging is heating the metal billet to an optimal temperature. Heating ensures the material becomes more ductile and easier to deform.
- Die Preparation: Precision forging requires a specially designed die, which is the tool used to shape the metal. The die is prepared to match the desired final shape of the component.
- Billet Placement: The heated billet is positioned within the die, usually using a hydraulic press or hammer. The pressure applied during forging is critical for shaping the metal accurately.
- Forging: The press or hammer exerts immense force on the billet, causing it to deform and take the shape of the die. The applied pressure exceeds the yield strength of the metal, resulting in plastic deformation.
- Cooling and Finishing: After forging, the component is allowed to cool. Sometimes, additional heat treatments may be applied to improve the mechanical properties of the forged part. Finally, any excess material is trimmed, and the component is finished to meet the required specifications.
Benefits of Precision Forging:
- Enhanced Mechanical Properties: Precision forging results in a component with improved mechanical properties. The grain structure of the metal is refined, leading to increased strength, toughness, and fatigue resistance. This makes precision-forged components highly durable and reliable.
- Complex Geometries: Precision forging allows the creation of complex shapes and intricate geometries that may be challenging to achieve using other methods. The process provides excellent dimensional accuracy and repeatability, ensuring consistent quality in mass production.
- Material Savings: Compared to traditional machining processes, precision forging reduces material wastage. It achieves near-net shape manufacturing, minimizing the need for excessive material removal. This leads to cost savings and efficient use of resources.
- Cost-Effective: Although precision forging may require upfront investment in tooling and equipment, it offers long-term cost benefits. The high production rates, material savings, and improved component quality contribute to overall cost-effectiveness.
- Improved Material Integrity: Precision forging eliminates internal defects such as porosity and inclusions, which are common in cast components. The forging process refines the microstructure, improving the overall integrity and reliability of the final product.
- Weight Reduction: Precision forging allows the design of lightweight components without compromising strength and performance. By optimizing the shape and eliminating excess material, it contributes to weight reduction in applications such as aerospace and automotive industries.
- Increased Productivity: Precision forging is a highly efficient process, capable of producing components at high production rates. The combination of advanced automation, shorter cycle times, and minimal secondary operations results in increased productivity.
In summary, precision forging utilizes controlled deformation of heated metal to create high-quality components with superior mechanical properties. The process offers numerous benefits, including enhanced strength, complex geometries, material savings, cost-effectiveness, improved material integrity, weight reduction, and increased productivity. These advantages make precision forging a preferred choice in various industries, including automotive, aerospace, and energy.