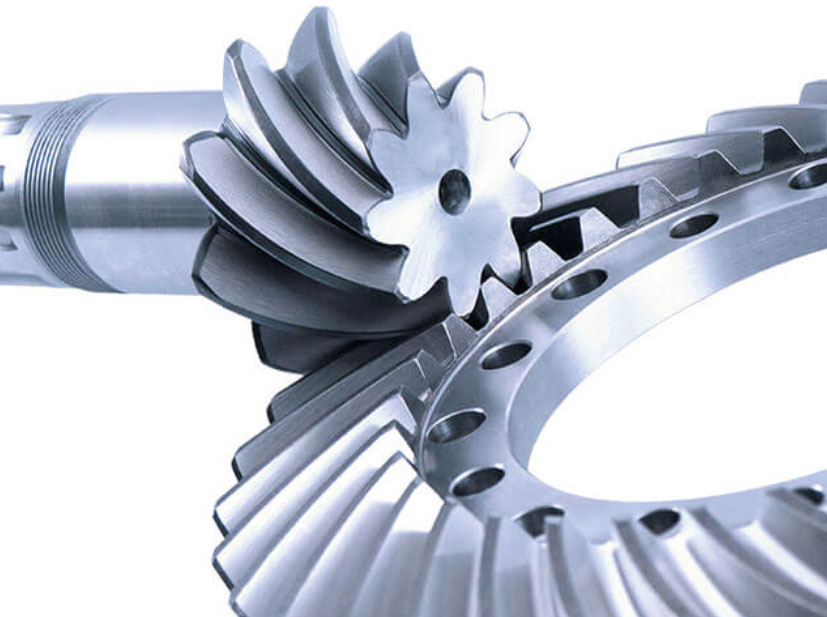
Understanding gear tooth contact patterns is essential in the science of spiral bevel gears. The contact pattern refers to the area of tooth contact between two mating gears during operation. Analyzing and optimizing the contact pattern is crucial to ensure smooth, efficient, and reliable gear performance. Let’s explore the key aspects of understanding gear tooth contact patterns in spiral bevel gears:
- Ideal Contact Pattern: In an ideal scenario, the gear tooth contact pattern should be a point or a line. This would mean that the load is distributed uniformly along the entire width of the gear tooth. However, in real-world applications, it is practically impossible to achieve this perfect point or line contact. Therefore, engineers aim to achieve the closest possible approximation of an ideal contact pattern.
- Tooth Surface Modifications: Achieving a desirable contact pattern often involves tooth surface modifications. Tooth surface modifications include crowning, profile shifting, and lead crowning. These modifications are done during the gear design phase to ensure that the actual contact pattern aligns with the desired contact pattern.
- Checking Contact Patterns: During gear development, engineers use various techniques to check and validate the contact pattern. Two commonly used methods are the “dye penetrant method” and the “contact pattern method.” The dye penetrant method involves applying dye on the tooth surface, and when the gears mesh, the dye transfers onto the mating gear, revealing the contact pattern. The contact pattern method uses a meshing test under load, and the contact pattern is inspected visually or using specialized equipment.
- Interpreting Contact Patterns: The contact pattern reveals important information about gear meshing behavior. Engineers examine the position, shape, and size of the contact pattern to identify any irregularities, such as edge contact, center contact, or off-center contact. The goal is to ensure that the contact pattern is centered, with uniform load distribution across the tooth width.
- Optimizing Contact Patterns: Achieving the desired contact pattern involves a careful design and manufacturing process. Engineers may adjust gear parameters such as tooth profile, spiral angle, gear spacing, and tooth surface modifications to optimize the contact pattern. Finite Element Analysis (FEA) and computer simulations are used to aid in this optimization process.
- Importance of Correct Contact Patterns: A well-optimized contact pattern is essential for several reasons:
- Even load distribution: A centered and uniform contact pattern ensures that the load is evenly distributed across the gear teeth, reducing the risk of tooth damage or premature wear.
- Noise reduction: An optimized contact pattern contributes to smoother gear meshing, reducing noise and vibration during operation.
- Efficiency: A proper contact pattern helps maximize gear efficiency by minimizing friction and power losses.
Understanding gear tooth contact patterns is crucial for ensuring the performance, reliability, and efficiency of spiral bevel gears. Engineers use various methods to analyze and optimize contact patterns during the gear design process, ultimately aiming to achieve a well-centered and uniform contact pattern for smooth and reliable gear operation.