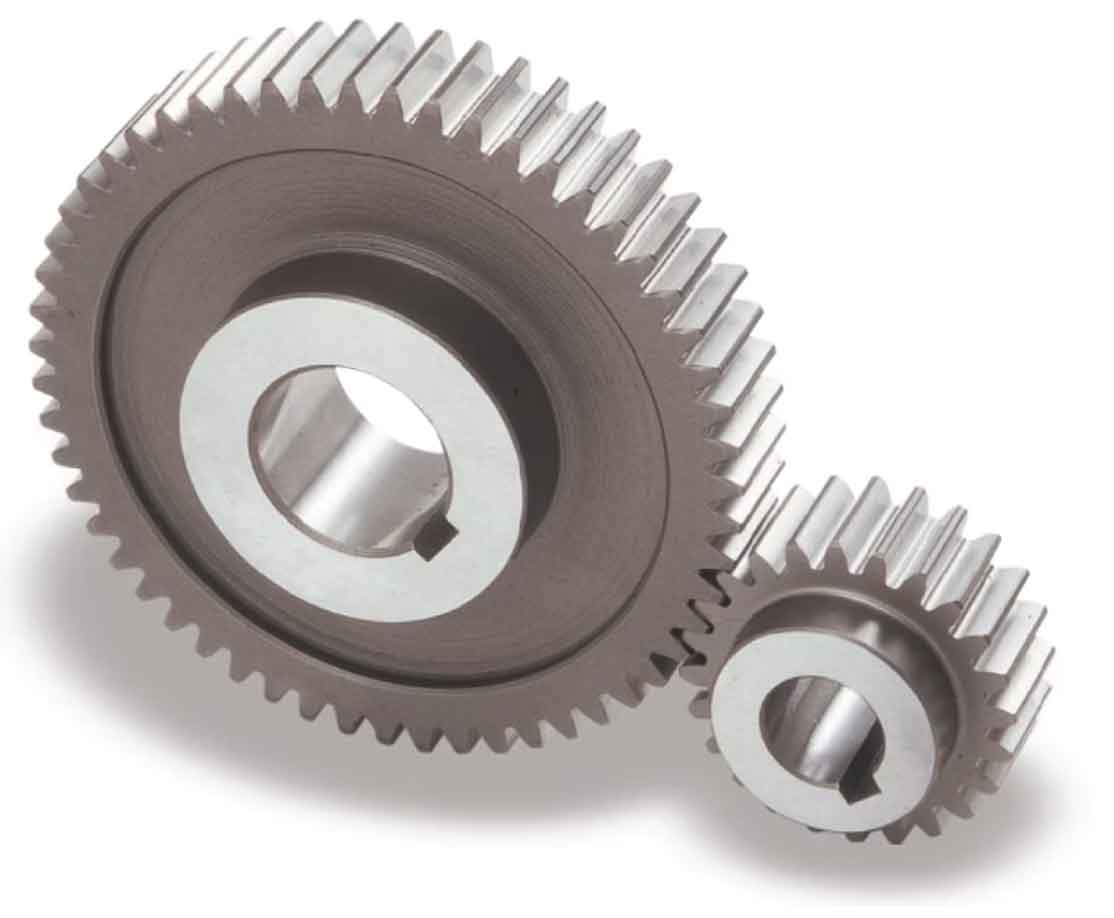
Spur gears are one of the most common types of gears used in various mechanical systems. They consist of cylindrical toothed wheels, also known as gears, with straight teeth that mesh together to transmit power and motion between parallel shafts. The science of spur gears involves understanding their design considerations and how they operate. Let’s explore these aspects in more detail:
- Gear Design Considerations:
- a. Pitch Diameter: The pitch diameter is the theoretical diameter where the gear teeth mesh. It determines the gear ratio and affects the speed and torque transmission between gears.
- b. Module or Diametral Pitch: These are the parameters used to define the size of the gear teeth. The module is the metric measurement, whereas the diametral pitch is the ratio of the number of teeth to the pitch diameter in inches.
- c. Pressure Angle: It is the angle between the tangent to the tooth profile and the line joining the gear centers. Common pressure angles are 14.5° and 20°, with 20° being more prevalent.
- d. Number of Teeth: The number of teeth on a gear affects the gear’s strength, smoothness of operation, and contact ratio. Higher tooth counts generally result in smoother operation.
- e. Material Selection: Gears are typically made from materials such as steel, cast iron, bronze, or plastics, depending on the application’s requirements for strength, wear resistance, and noise reduction.
- Gear Operation:
- a. Meshing: Spur gears mesh by their teeth engaging with each other. The teeth profiles are designed such that they provide a smooth transfer of motion and power. The gears must be aligned properly for effective and efficient operation.
- b. Gear Ratio: The gear ratio is determined by the number of teeth on the driver gear (input gear) and the driven gear (output gear). It represents the relationship between the speeds and torques of the two gears. Gear ratio = (Number of teeth on driven gear) / (Number of teeth on driver gear).
- c. Speed and Torque Transmission: Spur gears transmit rotational motion and power from one shaft to another. The speed of the driven gear is inversely proportional to its gear ratio, while the torque is directly proportional.
- d. Efficiency: The efficiency of gear transmission depends on factors such as gear quality, lubrication, alignment, and load distribution. Well-designed and properly maintained spur gears can achieve high efficiency, typically around 95-98%.
- Design Considerations for Optimal Performance:
- a. Tooth Profile: The shape of the gear tooth profile plays a vital role in smooth gear operation. Common tooth profiles include involute, cycloidal, and trochoidal. The involute tooth profile is widely used due to its favorable characteristics.
- b. Lubrication: Proper lubrication is crucial for reducing friction, wear, and noise. Lubricants such as oils or greases should be selected based on the gear material, operating conditions, and speed.
- c. Noise Reduction: Spur gears can generate noise during operation due to meshing action. To reduce noise, techniques such as tooth profiling, precision manufacturing, and surface treatments can be employed.
- d. Backlash: Backlash is the amount of play or clearance between meshing gears. It can affect the accuracy and precision of motion transmission. Minimizing backlash is important in applications that require precise positioning.
It is worth noting that spur gears have limitations, such as a potential for higher noise levels, lower load-carrying capacity compared to other gear types, and a lack of self-alignment capability. However, they are still widely used due to their simplicity, cost-effectiveness, and suitability for various applications where these limitations are not critical factors.
When designing or operating spur gears, it is essential to consider these factors to ensure optimal performance, efficiency, and longevity of the gear system. Consulting gear design manuals, standards, or seeking expert advice can help in creating robust and reliable gear systems tailored to specific applications.