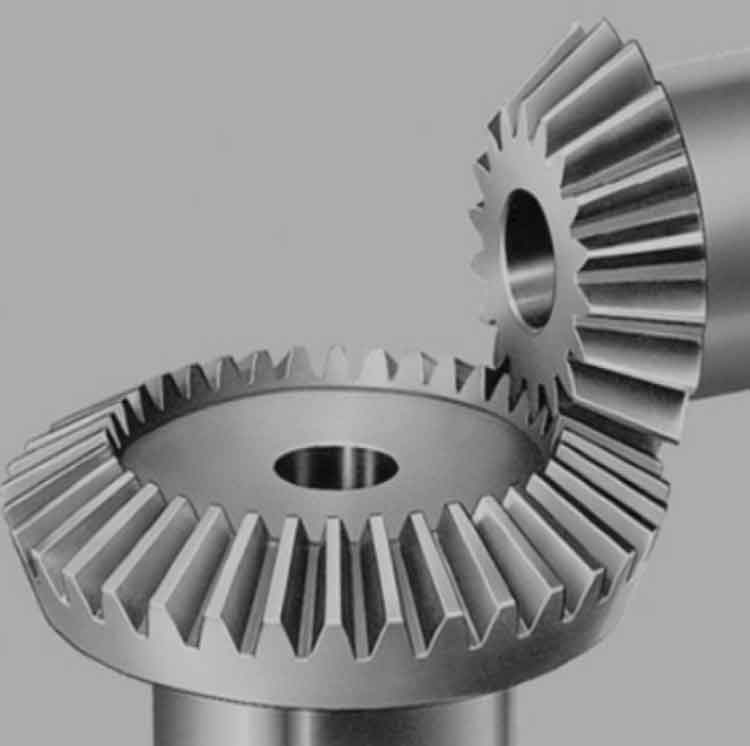
Straight bevel gears are a type of gears commonly used in various mechanical systems and machines. They have straight teeth that are cut along the surface of a cone, and they transmit power and motion between intersecting shafts. In this response, I will provide an overview of the design considerations and operation principles of straight bevel gears.
Design Considerations:
- Gear Ratio: The gear ratio determines the speed and torque relationship between the input and output shafts. It is defined as the ratio of the number of teeth on the driven gear (output gear) to the number of teeth on the driving gear (input gear). The gear ratio affects the speed and direction of rotation.
- Tooth Profile: Straight bevel gears have straight-cut teeth, which means the tooth profile is a straight line along the tooth width. The shape and size of the teeth, including the tooth thickness and profile angle, should be carefully designed to ensure smooth engagement and efficient power transmission.
- Pitch Diameter and Cone Angle: The pitch diameter is the theoretical diameter at which the gear tooth engages with another gear. The cone angle determines the shape and position of the gear tooth. These parameters affect the contact pattern, load distribution, and gear meshing characteristics.
- Backlash: Backlash is the clearance between the mating teeth when the gears are not engaged. It is necessary to consider the appropriate amount of backlash to allow for thermal expansion, lubrication, and minimize the risk of jamming. However, excessive backlash can result in reduced accuracy and increased noise.
- Materials and Heat Treatment: Straight bevel gears are commonly made from alloy steels to ensure strength, durability, and wear resistance. The selection of materials and appropriate heat treatment processes is crucial to achieve the desired hardness and surface finish, which impacts gear performance and longevity.
- Lubrication: Proper lubrication is essential to minimize friction, wear, and noise. The gear design should incorporate adequate space for lubricant circulation and ensure efficient lubrication of the gear teeth.
Operation Principles:
- Power Transmission: When the input shaft rotates, the driving gear transfers the rotational motion to the driven gear. The teeth of the driving gear mesh with the teeth of the driven gear, causing the driven gear to rotate in the opposite direction (for straight bevel gears with intersecting shafts).
- Contact Pattern: The contact pattern is the area of contact between the gear teeth during operation. It should be optimized to ensure even load distribution and minimize stress concentrations. Proper tooth alignment and gear meshing are critical to achieving a desirable contact pattern.
- Efficiency: Gear efficiency is influenced by various factors, such as tooth profile, lubrication, backlash, and material quality. Well-designed straight bevel gears can achieve high transmission efficiency, typically ranging from 95% to 98%.
- Noise and Vibration: The design and meshing characteristics of straight bevel gears can affect noise and vibration levels. Proper tooth profiling, gear alignment, and lubrication help reduce noise and vibration, ensuring smooth and quiet gear operation.
- Strength and Durability: Straight bevel gears must be designed to withstand the transmitted torque and loads without failure. The gear design should consider factors such as bending stress, tooth strength, and contact stress to ensure long-term durability and reliability.
It is important to note that the design and operation principles of straight bevel gears can vary depending on specific applications and requirements. Advanced computer-aided design (CAD) software and simulation tools are often used to optimize gear geometry and performance.