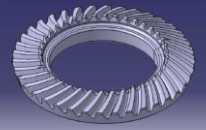
Using traditional manufacturing technology to produce high-performance and complex parts has become a bottleneck restricting the improvement of product quality and production efficiency. The forming process of parts is developing towards the direction of multi process cross compound application and near net forming of directly manufactured products. This paper attempts to introduce the casting forging compound forming process into the production of driven spiral bevel gear, so as to obtain the gear of near final product at one time. The product digital model is shown in Figure.
Through the finite element numerical simulation technology, the casting process and forging process of gear are simulated, and the process parameters are analyzed and improved to guide the actual production. The research and development of the casting forging compound forming process of the automobile rear axle spiral bevel gear can eliminate the defects such as casting porosity and refine the grains by forging, provide a good blank with teeth for forging by casting, and further expand the application of forging. The combination of the two is not simply the superposition of the advantages and disadvantages of each other, which can produce the effect of 1 + 1 > 2.
The risk of casting forging composite forming process is controllable, and the technology foresight is strong. In this paper, taking the product part drawing as the starting point, the forming analysis of each process step is carried out reversely and the workpiece size of each step is determined, which solves the influence of cold precision forging preform tooth shape on the cold finishing process, the influence of hot die forging preform tooth shape and taper on the hot die forging process step, the selection of casting process and the optimization of Pouring Scheme After a series of problems, such as the optimization of casting process parameters, it is completely feasible to develop a whole set of production process which is cost-effective and high-quality.
The main research directions are as follows:
1.The influence of the tooth shape of the preform on the cold precision forging process of spiral bevel gear is studied. In this paper, two kinds of tooth shape schemes, uniform diffusion tooth shape and non-uniform diffusion tooth shape, are put forward. By using DEFORM-3D software, the cold precision forging process of gear blank with different sizes is studied when two kinds of tooth shape schemes are adopted, and the optimized tooth shape of the cold precision forging preform is determined;
2.The influence of the tooth shape and taper of the preform on the forging step of the closed hot die forging was studied. Using DEFORM-3D The software analyzes the forming process of gear blank with different tooth size and different taper, which is similar to trapezoid tooth shape scheme in the hot die forging process. By comparing the metal flow direction and equivalent stress-strain distribution in the forming process of each scheme, the influence rule of tooth shape and gear taper on the hot die forging of gear is studied, and the optimized tooth shape and taper of the preform are determined;
3.Comprehensively analyze the structural characteristics, material composition and quality requirements of spiral bevel gear and the technical requirements of hot die forging steps to determine the casting process and casting drawing; design two casting schemes and calculate the sizes respectively; apply AnyCasting The software analyzes and compares the filling solidification process and defect prediction of two kinds of pouring schemes to determine the best Pouring Scheme; studies the influence of different process parameters (pouring temperature and pouring speed) on the forming quality of the casting and determines the best process parameters.