Generally, the heat treatment distortion of the controlled workpiece is focused on “quenching distortion”. The reason is that the quenching cooling takes place in the instantaneous sharp temperature reduction and structure transformation, accompanied by a large volume expansion and stress generation; while the heating process is much slower, and with the temperature rising, the plastic resistance of the metal decreases, and various stresses are released. On the other hand, the workpiece has been finished after quenching and is in cold state, its distortion needs to be measured or can be measured; while the workpiece in heating is in the middle process, its distortion does not need to be measured or can not be measured, so little is known about the distortion of heating process. In fact, in the process of heating, not only the thermal stress causes distortion, but also the release of internal stress causes distortion.
Before the final heat treatment and quenching of gears, there are two important processes closely related to the heating distortion: (1) heat treatment of rough preparation; (2) machining. Some people have carried out the test of gear carburizing without quenching and cooling, carburizing after hobbing, and measuring its distortion after carburizing,. The data show that there is no severe cooling in the carburizing stage, but there is a large distortion. This kind of distortion is related to the structure state, processing stress and heating state of gear blank.
1. Release and distortion of processing stress
In the process of gear cutting, the metal is cut on the macro level, and the tool on the micro level produces plastic deformation and work hardening on the metal, and at the same time produces residual stress. Figure 2 shows the hardness distribution caused by work hardening during steel cutting, and figure 3 shows the residual stress distribution caused by cutting [4].
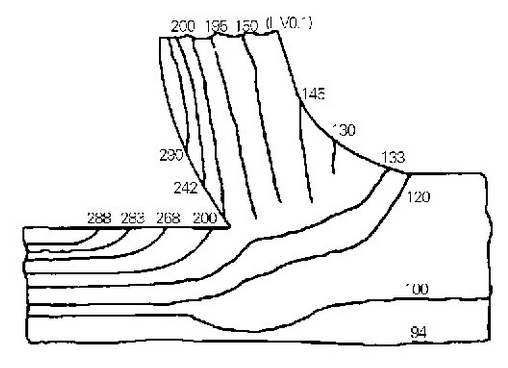
In order to observe the distortion caused by the release of cutting stress in the process of heating, a reverse sliding gear was used to test and measure the distortion of a-end with thin gear wall. The gear diagram is shown in Figure. The cutting gear is recrystallized and annealed at 650 ℃× 2 h, and the influence of machining residual stress on the distortion is observed by the change increment of the bottom diameter of the gear spline hole before and after annealing.
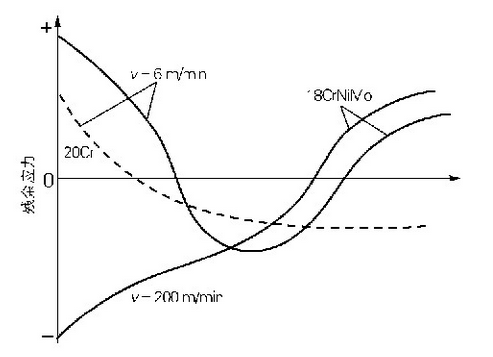
90 data are measured from the bottom diameter of 30 thin-walled a-end spline holes of recrystallized annealed gear, and the size change data are arranged in the form of frequency histogram, as shown in Figure 5. It can be seen from Figure 5 that after recrystallization annealing, with the elimination of processing stress, the bottom diameter of spline hole tends to increase, and the relative frequency of increment in the range of 0.005-0.020 mm exceeds 70.
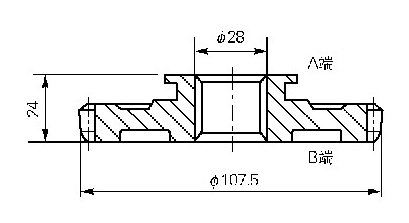
It is generally believed that the stress relief annealing of gear after machining can also eliminate the mechanical conditions that cause distortion due to the elimination of residual stress. However, the test shows that in the process of stress relief annealing at 650 ℃, along with the recovery of distorted lattice and the release of internal stress, the result is “stress relief, leaving distortion”.
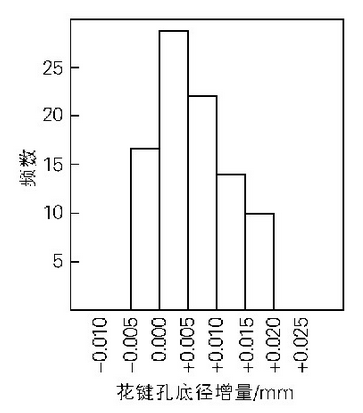
2. Tissue transformation and distortion in heating
Gear blanks are usually normalized to obtain ferrite + pearlite structure. On the one hand, it is easy to process, and on the other hand, it is also prepared for the later heat treatment.
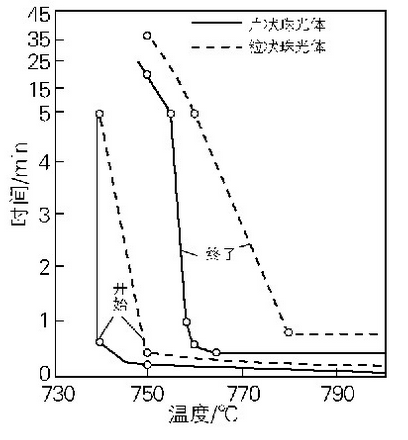
1) Effect of ferrite and pearlite structure on austenite transformation rate
During the heating process, the normalized structure is affected by the original structure state when it transforms to austenite. The transformation speed to austenite is also different when the structure state of ferrite + pearlite is different, as shown in Figure 6. Because the specific volume of ferrite + pearlite is different from that of austenite, if the original structure of gear blank normalizing is uneven, the uneven volume change will be caused due to the different speed of transformation during the heating process, resulting in distortion.
2) Effect of heating temperature on the transformation rate of ferrite pearlite austenite
The effect of heating temperature on the transformation rate from ferrite to pearlite to austenite. When the heating temperature is 740 ℃, it takes 100 s to transform 50%, while when the temperature is 800 ℃, it takes only 1 s, which is quite different. When the gear is heated in the carburizing furnace of 925 ~ 950 ℃, a large temperature difference is generated in each part due to various reasons. This temperature difference makes the transformation speed of ferrite + pearlite → a in each part different, so the volume difference in each part of the gear causes distortion.
3. Heating nonuniformity and distortion
In the heating of gears, due to the influence of structural shape, clamping, placement and furnace loading, the heating of gears is uneven, especially at 925 ~ 950 ℃ high temperature carburizing temperature, some parts will be mainly heated by radiation, while others are mainly heated by convection, because the heating speed of radiation heating is much faster than that of convection heating, It will form a large temperature difference between the parts of the gear workpiece and generate thermal stress.
The high temperature plastic resistance of alloy steel 34crnimo6 has been measured. The results are shown in the table, which can be used as a reference for analysis. According to the thermal stress calculation formula σ th ≈ 0.34 Δ T, the thermal stresses relative to various temperature differences are listed in the table.
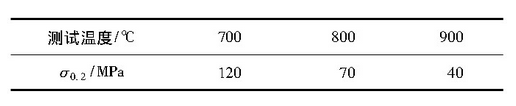

According to the data in Table 3 and table 4, it can be predicted that in many production cases, the temperature difference of the clamped gear is large at the initial stage of entering the furnace, and the generated thermal stress is enough to cause the plastic deformation and distortion of the first high temperature part.