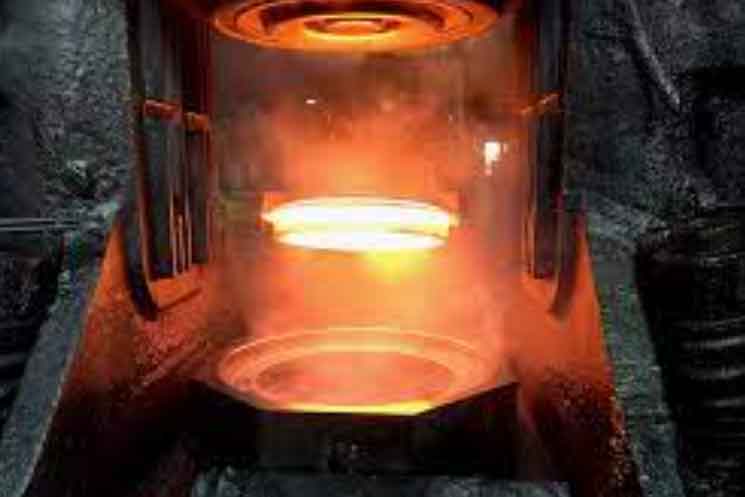
The Superiority of Gear Forgings emphasizes the exceptional qualities and advantages of gear forgings over other manufacturing methods. Gear forgings offer unmatched strength, durability, and performance, making them the preferred choice for critical applications that demand reliability and longevity.
- Exceptional Strength: Gear forgings are renowned for their superior strength. The forging process aligns the grain structure of the metal, resulting in increased mechanical properties, including higher tensile and yield strengths. This ensures that forged gears can withstand heavy loads, shocks, and stresses without failure or deformation.
- Enhanced Durability: The robustness of gear forgings enables them to withstand harsh operating conditions and repeated use over an extended lifespan. Their resistance to fatigue and wear ensures reliable performance even in high-demand applications. Forged gears are less prone to cracks, fractures, and surface damage, ensuring long-lasting durability.
- Consistent Quality: Gear forgings offer exceptional dimensional accuracy and uniformity. The controlled forging process ensures tight tolerances, precise gear profiles, and consistent mechanical properties across multiple gears. This uniformity enhances gear meshing, reduces noise, and minimizes vibration, resulting in smoother operation and improved efficiency.
- Optimal Material Utilization: The forging process allows for optimal material utilization, minimizing waste and maximizing the strength-to-weight ratio of the gears. By using less material without compromising strength, forged gears are lighter and more efficient, contributing to overall system performance.
- Resistance to Corrosion and Heat: Gear forgings made from corrosion-resistant alloys or stainless steels exhibit excellent resistance to rust, oxidation, and other forms of corrosion. They can also withstand high temperatures without losing their mechanical properties, making them suitable for applications in extreme environments.
- Customization and Versatility: Gear forgings provide flexibility in terms of design and customization. They can be tailored to specific requirements, accommodating a wide range of gear sizes, shapes, and complexities. This adaptability enables manufacturers to produce gears that precisely match the application’s needs, optimizing performance and efficiency.
- Cost-Effectiveness: While gear forgings may involve higher initial costs due to tooling and equipment requirements, their long-term cost-effectiveness is undeniable. The extended service life, reduced maintenance, and minimal gear failures contribute to significant cost savings over the gear’s lifetime.
- Industry Applications: Gear forgings are widely used in industries such as automotive, aerospace, defense, heavy machinery, and power generation. They are found in critical applications like gearboxes, transmissions, drivetrains, and other high-load systems where reliability and performance are paramount.
The superiority of gear forgings lies in their exceptional strength, durability, and performance. These attributes, combined with consistent quality, customization options, and cost-effectiveness, make gear forgings the preferred choice for demanding applications. When reliability and longevity are crucial, gear forgings provide the assurance of superior gear manufacturing.