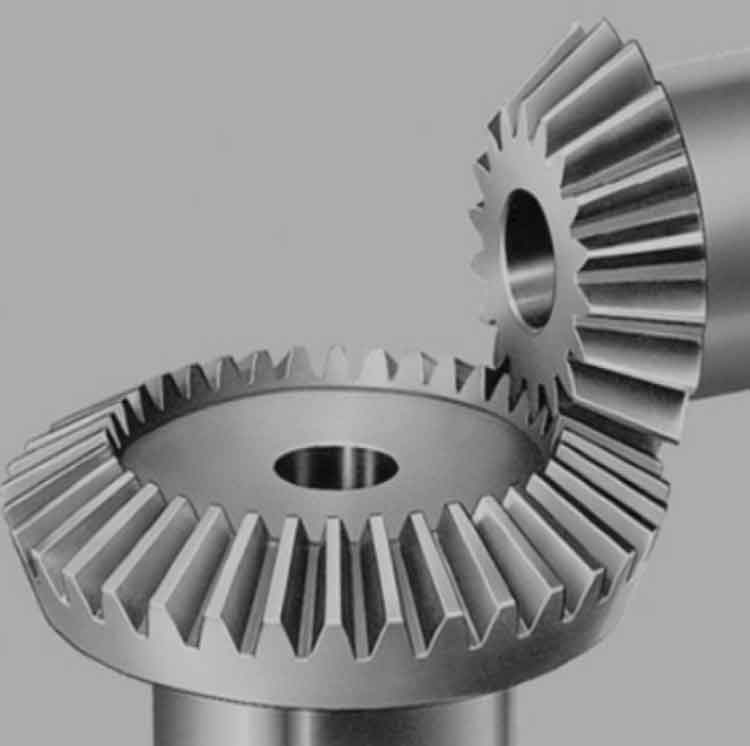
Thermal analysis of straight bevel gear systems is crucial to ensuring their performance and reliability under varying operating conditions. Gears in industrial applications, including straight bevel gears, are subjected to high loads and speeds, resulting in heat generation due to friction and mechanical losses. Thermal analysis helps engineers understand and manage the heat generated during gear operation, preventing overheating and potential failures. Here’s how thermal analysis is performed for straight bevel gear systems:
1. Finite Element Analysis (FEA):
- FEA is utilized to simulate the thermal behavior of the gear system.
- Engineers create a detailed 3D model of the gear system, including gears, shafts, housings, and lubrication elements.
- FEA software calculates the heat distribution and temperature rise under various operating conditions.
2. Contact and Friction Analysis:
- Contact analysis helps understand the points of contact and sliding between gear teeth during meshing.
- Friction analysis assesses the frictional losses, which contribute to heat generation.
- Both analyses provide valuable insights into the areas of high thermal stress and potential overheating.
3. Thermocouples and Temperature Sensors:
- Thermocouples and temperature sensors are placed at critical locations within the gear system to measure real-time temperatures during operation.
- These measurements help validate the thermal analysis results and identify any discrepancies.
4. Lubrication Analysis:
- Lubrication analysis evaluates the effectiveness of the lubricant in dissipating heat and reducing friction between gear surfaces.
- Proper lubrication is essential to minimize wear, reduce heat generation, and extend gear life.
5. Material Selection:
- The choice of gear materials can significantly impact thermal performance.
- Heat-resistant materials with good thermal conductivity and low coefficient of friction are preferred for high-temperature applications.
6. Heat Dissipation and Cooling Strategies:
- Based on the thermal analysis results, engineers may implement heat dissipation and cooling strategies to manage excessive heat.
- These strategies may include improved gear housing design, enhanced airflow, or the use of cooling channels.
7. Dynamic Analysis:
- Dynamic analysis helps understand the gear system’s behavior during transient conditions, such as start-up and high-speed operations, where additional heat may be generated.
8. Reliability Assessment:
- Thermal analysis results are used to assess the gear system’s reliability and determine if any design modifications or cooling measures are required.
By conducting thermal analysis, engineers can ensure that straight bevel gear systems remain within safe operating temperature limits and achieve optimal performance. Managing heat generation and dissipation is essential to prevent gear failure, improve gear life, and maintain the efficiency of industrial machinery that relies on straight bevel gears.