According to the three body theory of fretting wear, the formation and evolution of wear debris are produced simultaneously and continuously.
(1) Generation of wear debris:
① The micro convex surface of the contact surface has adhesion, plastic deformation and work hardening;
② The work hardening makes the material brittle and forms a white layer. With the deformation of the micro convex body, the white layer is broken, and the micro convex body peels and falls into wear debris;
③ The migration process is mainly affected by the size, shape and mechanical parameters (such as amplitude, frequency, load, etc.).
(2) Evolution of debris:
① At first, the wear debris showed slight oxidation, which was still the metal color, and the size of the wear debris was in the order of micrometer (about 1 μ m);
② In the process of crushing and transferring, the wear debris were oxidized further, and the color of the wear debris was gray brown, and the size of the wear debris was about 0.1 μ M;
③ The results of X-ray diffraction show that the wear debris is composed of Fe2O3, Fe3O4 and other oxides.
The fretting wear on the contact surface of the object is mainly affected by the transformation process of the wear debris and the formation of the wear debris bed (the third body bed), while the formation of the wear debris bed or the elimination effect of the third body is mainly determined by the test conditions of fretting wear and the shape of the sample. Generally, the third body bed between two objects reduces the adhesion of the contact surface, which can effectively protect the friction surface, and then reduce the fretting wear between objects. However, during the test, if there is periodic pause on the friction surface, the debris will be excluded from the contact surface, and the wear on the contact surface will increase accordingly.
The three body theory can be used to explain the change process of the fretting friction coefficient of metal materials with the number of cycles
① If the oxide film on the contact surface is worn off, the friction coefficient of the friction surface will be reduced;
② When the interaction between the second body and the first body is strengthened, the friction contact surface will adhere, the friction coefficient of the friction surface will increase correspondingly, and the change of metal material structure (such as work hardening) will change correspondingly;
③ Because of the protection of the third body, the adhesive wear is restrained and the friction coefficient of the contact surface is reduced;
④ The wear debris on the contact surface reaches a dynamic equilibrium process of continuous formation and removal, which makes the fretting wear of materials enter a stable stage.
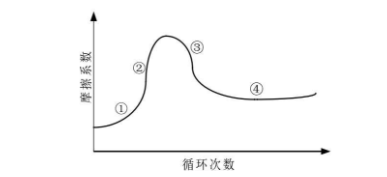