Gear is the core component in the field of power transmission. It is widely used in automobile, aerospace, ship and other transmission links. It has the advantages of compact structure, high transmission efficiency and high transmission power. The common gear processing technology includes gear grinding, hobbing, gear shaping, gear grinding, etc. In different fields or transmission links, different processes are used. Taking aerospace as an example, gear grinding technology is used in any part, so the cost is high. The research object of this paper is the main reducer of drive axle, especially in the field of heavy truck. Under the pressure of cost, gear milling and gear lapping technology are widely used in the industry, which has the defects of poor precision and large machining error. In this regard, combined with the specific structure of the axle main reducer, the vibration characteristics of the main reducer system with typical machining errors are analyzed in detail.
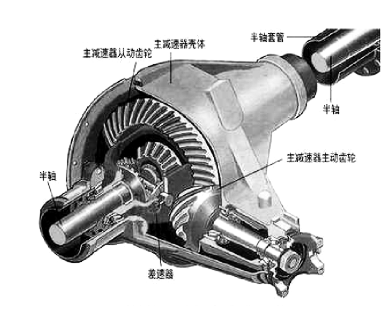
The main reducer system structure of single stage drive axle is shown in Figure 1, which is mainly composed of spiral bevel gear pair, differential, half shaft gear and other transmission components and main reducer housing. Because of its structure, bevel gear pair as the most important transmission component, in the process of transmitting the speed and torque of engine and gearbox, the meshing excitation caused by tooth contact is the most important factor affecting the NVH performance of drive axle.
Firstly, the structure of axle main reducer is introduced systematically, and it is pointed out that bevel gear pair is the key component affecting NVH performance of axle. Secondly, the typical machining errors which have great influence on the NVH performance of bevel gear pair are introduced in detail, and the causes are explained clearly. Furthermore, the influence of typical machining errors on the vibration characteristics of bevel gears is analyzed and discussed in detail. Finally, the research provides guidance for the machining, design and NVH performance control of bevel gear pair.