Gear pair is the core component of gear transmission system, and time-varying meshing stiffness is the main excitation source of gear transmission system, which directly affects the transmission efficiency of gear transmission system. At the same time, during the meshing process of gear pair, the pulse cyclic stress on the root of gear teeth is large. Once the cyclic stress exceeds the stress limit of gear material, cracks will be generated at the root of gear teeth, and the cracks will gradually expand with the operation of gear pair until the remaining part of the gear can not bear the load, which seriously affects the smooth operation of the gear transmission system. Therefore, in this chapter, the energy method is used to calculate the time-varying meshing stiffness of a pair of involute spur gears. The dynamic model of the gear pair is established based on Lagrange equation to reveal the variation law of the time-varying meshing stiffness of the gear pair with root crack. The influence of the time-varying meshing stiffness excitation and the gear crack on the vibration characteristics of the gear pair is analyzed Vibration analysis of typical faults of the dynamic system lays the foundation.
During the operation of the gear pair, the single and double teeth are alternately meshed, and the elastic deformation between the teeth presents periodic changes: there is only one pair of teeth in the single tooth meshing area to bear the load, the meshing elastic deformation is large, and the corresponding meshing stiffness is small; in the double tooth meshing area, two pairs of teeth engage in meshing, and the two pairs of teeth share the load, so the meshing elastic deformation is small and the corresponding meshing stiffness is large 。 When meshing with a single tooth, the stiffness of the meshing area changes with the value of 1, as shown in the figure.
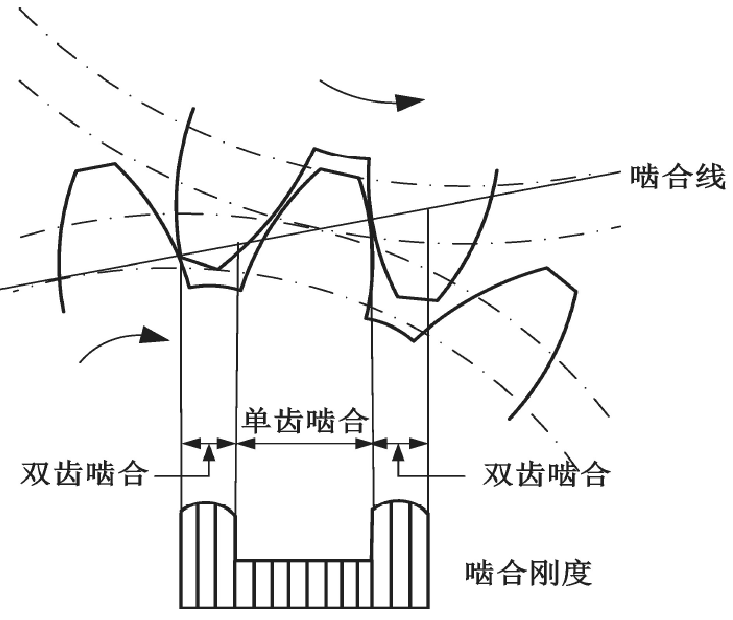
There are mainly formula method, numerical method and simplified square wave method to solve the time-varying meshing stiffness of gear pair. The formula methods include werber formula method, energy method, approximate formula method and Ishikawa formula method, Numerical methods include finite element method, regression method and boundary element method. The simplified square wave method is generally used in various standards. The amplitude of square wave is calculated according to formula method, and then simplified to a square wave function according to certain standards, such as iso6336-1996, gb3480-1997, etc.
Compared with other calculation methods, the energy method proposed by Yang and Lin in 1987 is widely used by scholars at home and abroad because of its clear physical meaning and simple solution. The energy stored in the process of gear transmission due to force deformation includes bending deformation energy, Hertz contact deformation energy and radial compression deformation energy. In 2004, TIA] added shear potential energy to the calculation of time-varying meshing stiffness of gears by energy method, which makes the calculation results of energy method more accurate. In the same year, sainsot et al. Found that the gear matrix will also produce certain deformation when the gear is under load. They have derived the calculation formula of the gear matrix under load deformation. Therefore, the Hertz contact stiffness, bending stiffness, shear stiffness, radial compression stiffness and matrix flexible deformation stiffness are obtained by energy method, and the time-varying meshing stiffness is synthesized, which lays a theoretical foundation for dynamic modeling and analysis of gear pair.