Munro defines the transmission error te (transmission error) as follows: the deviation between the actual position of the driven gear (corresponding to any given position of the driving gear) and the theoretical position of the driven gear (if both gears are ideal and do not deform). Gear transmission error mainly comes from geometric deviation, shell support deformation and gear dynamic effect. Among them, the geometric deviation mainly comes from the manufacturing and actual assembly of gears, which leads to the spatial deviation of tooth profile, pitch line and tooth surface.
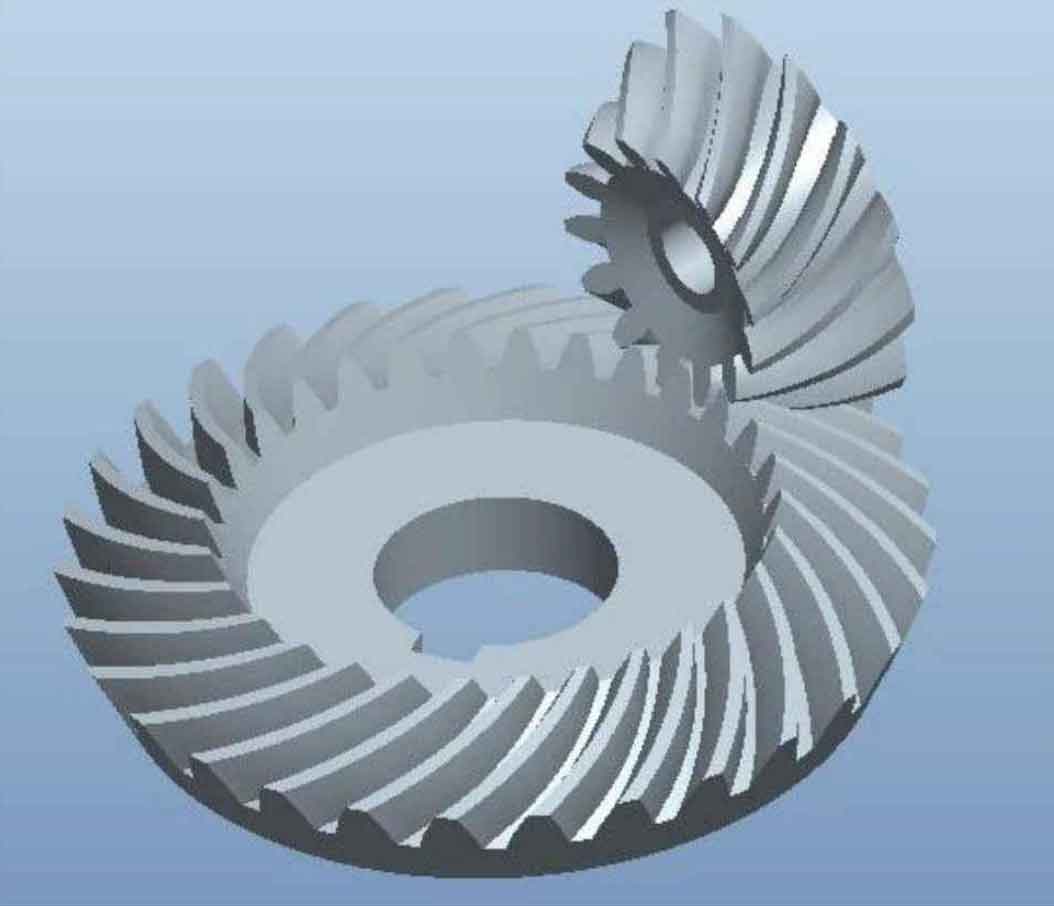
In foreign countries, the current research on the transmission error of hypoid gears mainly focuses on two aspects,
(1) No load TCA (tool contact analysis) analysis, through TCA optimization tool and machine tool setting parameters to process more accurate tooth surface profile, so that the gear pair meshing to achieve the ideal transmission error and contact mode. No load TCA predicts gear transmission error and contact based on gear geometry, without considering the elastic deformation of gear blank. In 2010, Kawasaki et al. Verified the accuracy of no-load TCA by predicting and measuring transmission error (TE) and contact mode.
(2) Stress and load analysis to obtain the load transmission error, namely LTCA (load tooth contact analysis) analysis. LTCA considers the actual load of the gear, which is closer to the actual operating condition of the gear. The load transmission error can be obtained through the load LTCA analysis. Many researchers have established load LTCA analysis methods. For example, Simon V predicted the gear meshing transmission error based on the finite element method in 2001, and compared the simulation results with the test results to verify the accuracy of the simulation.
In China, many scholars have studied the transmission errors of spiral bevel gears or hypoid gears, and there are many research results based on transmission errors. In 2002, Fang Zongde and others proposed a method to optimize the geometric transmission error amplitude of spiral bevel gears to reduce gear vibration and noise under light load conditions.
In 2003, Wei Bingyang and others first analyzed the no-load contact and loaded contact of spiral bevel gears to obtain the transmission error of gears under different loads, and then optimized the transmission error to reduce the transmission fluctuation of gears. In 2009, Cao Xuemei et al. Used the finite element method to obtain the gear bearing transmission error. In 2012, Tang Jinyuan et al. Proposed using the finite element method to analyze the contact of spur gear, and obtained the transmission parameters such as the transmission coincidence degree, transmission error and load distribution coefficient of face gear.
In 2014, Wang Zhonghou and others established an analysis model of spiral bevel gear transmission error by using the finite element method, and compared the difference between gear static transmission error and dynamic transmission error under load conditions. In 2016, based on the finite element method, Zhou Chi and others compared and analyzed the influence of different loads on the transmission error and time-varying meshing stiffness of hypoid gears.
In 2017, using the local synthesis method, according to the processing principle of HGT Gleason hypoid gear, and taking the minimum amplitude of load-bearing transmission error as the optimization goal, Uranus et al. Used genetic algorithm to optimize the processing parameters.