The calculation process of the modification parameter calculation method mainly includes four steps: the first step is to obtain the actual meshing state of each gear pair during operation through system dynamics simulation, which is used as the input condition of tooth surface modification. In the second step, taking the actual meshing state as the input, using the fine contact algorithm, considering the stress concentration at the edge of the tooth, and taking the minimum stress on the tooth surface as the objective, the tooth direction drum repair is carried out. In the third step, the actual meshing state and the amount of tooth profile modification are taken as the input, and the minimum fluctuation of static transmission error is taken as the objective to carry out the tooth profile modification. In the fourth step, the modification parameters are replaced back to the system dynamics equation and simulated, and the actual meshing state and modification parameters of each gear pair are updated continuously until the modification parameters converge.
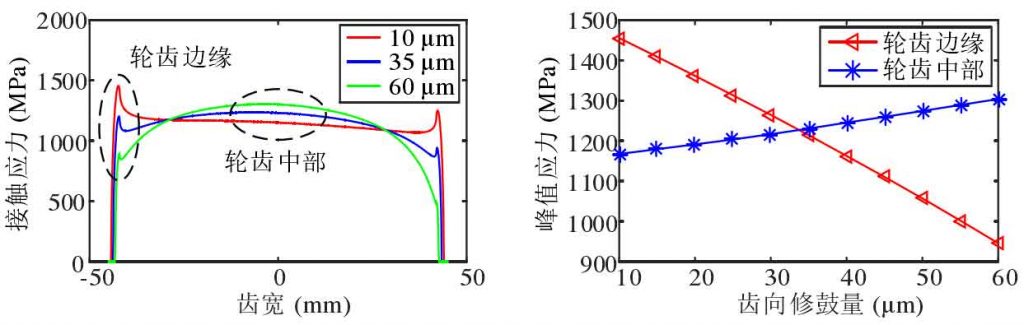
Taking gear pair 2 of cutting part as an example, this paper expounds the determination method of the best tooth direction drum repair amount. Firstly, the peak value of meshing tooth alignment error and the peak value of dynamic tooth force calculated in the first step are taken as input parameters to calculate the contact stress at the two pitch circles of the gear pair. Then, the stress concentration at the edge of the gear tooth decreases gradually with the increase of the amount of tooth direction modification, while the contact stress at the middle of the gear tooth increases gradually, as shown in figure (a). The variation of the peak stress at the edge and middle of the tooth with the amount of tooth direction bulging is shown in figure (b). The abscissa of the intersection of the two curves (33.3 μ m) is the best amount of tooth direction bulging of gear pair 2 in this meshing state.