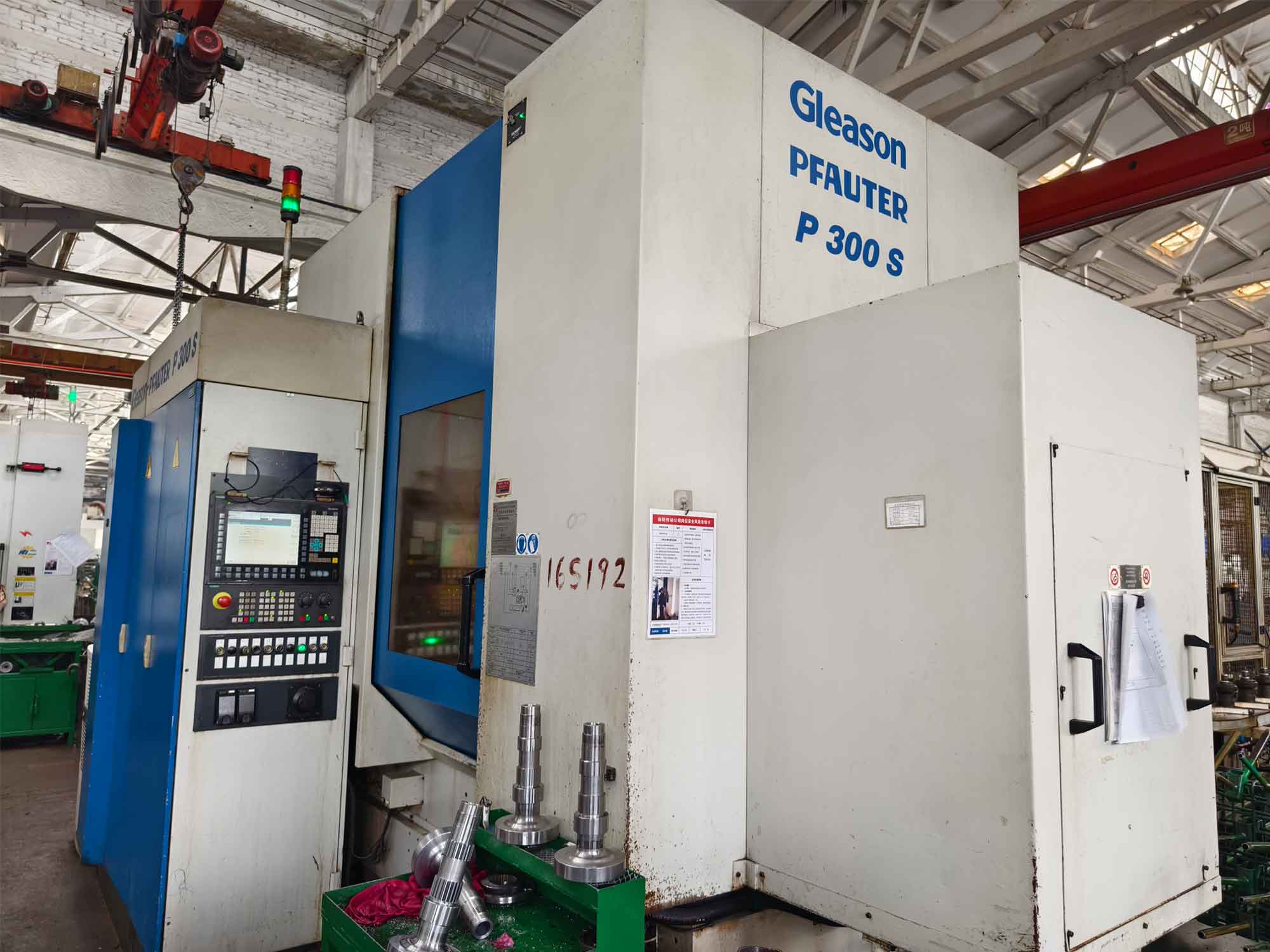
The gear manufacturing industry in 2024 is seeing significant advancements and innovations, primarily influenced by the evolving demands of various sectors including automotive, aerospace, and renewable energy systems. Here are some of the top innovations and trends shaping the industry this year:
- Digital Twins and Big Data: There is an increasing application of digital twins and big data analytics within gear manufacturing. These technologies enable real-time monitoring and optimization, leading to enhanced efficiency and reduced downtime in gear manufacturing processes.
- Automation and Advanced Robotics: Automation continues to be a central theme, with more gear manufacturers integrating advanced robotics to increase precision and reduce cycle times. This is especially prevalent in applications demanding high precision, such as in aerospace and defense sectors.
- Electrification and E-Mobility: The shift towards electric vehicles (EVs) and the broader trend of electrification are significantly impacting gear manufacturing. Gear manufacturers are focusing on producing specialized gears that are compatible with EV transmissions and powertrains. This includes the development of lightweight and compact gears to meet the specific requirements of electric and hybrid vehicles.
- Skiving Techniques: Gear skiving has become a critical technique due to its efficiency and the quality of the finish it offers. It allows for the machining of internal gears and the creation of high-quality external gears, which are particularly useful in the production of automotive and industrial gears.
- Sustainability and Renewable Energy: There is a growing emphasis on sustainability within the industry. Gear manufacturers are increasingly involved in producing components for renewable energy systems, such as wind turbines, where precision and durability of gears are paramount.
- Enhanced Surface Finishing Technologies: Technologies like gear grinding and honing are increasingly used to meet stringent quality requirements. These methods are essential for reducing noise, vibration, and harshness (NVH), which is particularly important in the automotive sector as it transitions more towards EVs.
- 3D Printing and Additive Manufacturing: The adoption of 3D printing technologies is transforming gear manufacturing by enabling the production of complex gear geometries that are difficult or impossible to achieve with traditional methods. This innovation allows for more customization and flexibility in design and has the potential to reduce waste and overall production costs.
- High Precision Metrology: The increasing demand for precision has led to the integration of advanced metrology tools within the gear manufacturing process. These tools ensure that gears meet strict dimensional tolerances and performance standards required in high-tech applications, such as aerospace and high-performance automotive industries.
- Integration of Industry 4.0: Smart gear manufacturing practices under Industry 4.0 are becoming more prevalent, integrating IoT, machine learning, and artificial intelligence into the production lines. This leads to smarter, more connected manufacturing environments that can predict maintenance needs and optimize production processes in real-time.
- Material Innovations: There is ongoing research and development into new materials that can withstand more extreme conditions and offer better performance. Innovations include the use of advanced composites and lightweight alloys, which are crucial for industries like aerospace and automotive where weight reduction is essential for efficiency and performance.
- Customization at Scale: Gear manufacturers are leveraging flexible manufacturing systems that can handle small batch sizes economically, allowing for greater customization. This trend is driven by specific customer needs across different industries, including specialized machinery and luxury automotive manufacturing.
These innovations reflect a broader trend towards more efficient, sustainable, and precise gear manufacturing processes, driven by advancements in technology and changes in consumer and industrial demand. The focus is not only on enhancing the product quality but also on making the production processes more agile and less resource-intensive. As the industry continues to evolve, these trends are likely to expand further, leading to more innovative solutions in gear manufacturing.