Troubleshooting common issues in helical gear systems is essential for maintaining their efficiency, reliability, and longevity. Despite their advantages in terms of smooth operation and load capacity, helical gear can encounter several problems that may affect their performance. Here are some of the most common issues encountered in helical gear systems, along with strategies for diagnosis and resolution:
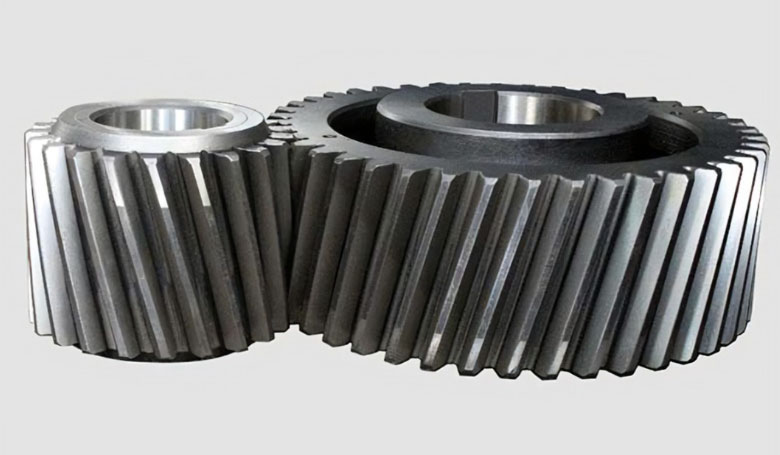
1. Gear Noise and Vibration
- Causes: Incorrect meshing due to manufacturing errors, improper installation, or wear; insufficient lubrication; misalignment of helical gear axes.
- Troubleshooting: Check for alignment accuracy and adjust as necessary. Inspect helical gear teeth for wear or damage and ensure that the lubrication system is functioning correctly. Consider using helical gear with a modified tooth profile or a different helix angle to reduce noise.
2. Premature Wear
- Causes: Excessive load; poor lubrication; abrasive contaminants in the lubricant; material defects.
- Troubleshooting: Verify that the helical gear system is not overloaded beyond its designed capacity. Analyze lubricant quality and replace or filter to remove contaminants. Inspect helical gear for material flaws or insufficient heat treatment and consider upgrading to a more suitable material or surface coating.
3. Overheating
- Causes: High friction due to inadequate lubrication or excessive loading; misalignment; high ambient temperatures.
- Troubleshooting: Ensure proper lubrication, including the type and amount of lubricant. Check for and correct any misalignment issues. If the environment contributes to overheating, consider additional cooling measures such as external fans or heat exchangers.
4. Tooth Breakage
- Causes: Material defects; improper tooth geometry; excessive load; shock loading; fatigue failure.
- Troubleshooting: Inspect broken teeth for signs of fatigue, such as crack initiation points. Review the application’s loading conditions to ensure they are within the helical gear’s design limits. Consider using helical gear made from materials with higher toughness or implementing design changes to distribute loads more evenly.
5. Axial Thrust Issues
- Causes: Helical gear design inherently produces axial forces. These forces can be problematic if the bearings or helical gear housing are not designed to accommodate them.
- Troubleshooting: Check that bearings and helical gear housing are appropriate for the axial loads present. Adjusting the helix angle or using double-helical (herringbone) gears can balance out axial forces.
6. Lubrication Failure
- Causes: Using the wrong type or grade of lubricant; lubricant degradation; insufficient lubricant supply.
- Troubleshooting: Confirm the correct lubricant specifications for the helical gear system and operating conditions. Check lubricant delivery systems for blockages or malfunctions and ensure regular maintenance schedules are followed to replace or filter the lubricant.
7. Misalignment
- Causes: Poor installation; settling or shifting of foundations; thermal expansion; bearing wear.
- Troubleshooting: Use precision alignment tools to check and adjust the alignment of helical gear shafts. Regularly inspect and replace worn bearings and consider the effects of thermal expansion in the design and operation of the helical gear system.
8. Corrosion and Environmental Damage
- Causes: Exposure to corrosive substances or extreme environments; lack of protective coatings or seals.
- Troubleshooting: Implement protective measures such as corrosion-resistant coatings, seals, and environmental enclosures. Regularly inspect helical gear systems for signs of corrosion and clean or replace affected components as necessary.
Effective troubleshooting of helical gear systems requires a systematic approach to identify the root causes of issues and implement corrective measures. Regular maintenance, along with monitoring and analysis of helical gear performance, can prevent many common problems and ensure reliable operation over the long term.