Case hardening is a widely used heat treatment process to enhance the surface hardness and wear resistance of components. However, it can sometimes be accompanied by various defects that can compromise the integrity and functionality of the heat-treated parts. Troubleshooting these heat treatment defects is crucial to identify the root causes and implement corrective measures. This article explores common heat treatment defects encountered during case hardening and provides troubleshooting strategies to address these issues effectively.
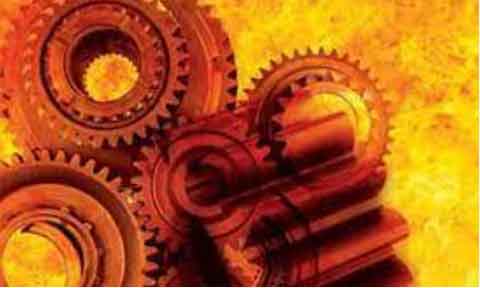
1.Excessive Case Depth:
- Cause: Excessive case depth occurs when the carbon or nitrogen diffusion extends beyond the desired depth, resulting in a thicker hardened layer.
- Troubleshooting Strategies:
- Review the carbon or nitrogen potential in the atmosphere or the composition of the case hardening medium.
- Analyze the process parameters such as time, temperature, and quenching technique to ensure they are within the specified range.
- Consider adjusting the process parameters or altering the composition of the case hardening medium to achieve the desired case depth.
2.Insufficient Case Depth:
- Cause: Insufficient case depth occurs when the carbon or nitrogen diffusion is insufficient, resulting in a thinner hardened layer than required.
- Troubleshooting Strategies:
- Review the carbon or nitrogen potential in the atmosphere or the composition of the case hardening medium.
- Analyze the process parameters such as time, temperature, and quenching technique to ensure they are within the specified range.
- Consider increasing the process time, temperature, or carbon/nitrogen potential to achieve the desired case depth.
3.Case Decarburization:
- Cause: Case decarburization happens when the carbon content near the surface of the component is reduced during the case hardening process, resulting in decreased hardness and compromised properties.
- Troubleshooting Strategies:
- Ensure proper control of the case hardening atmosphere to prevent excessive oxidation and decarburization.
- Review the heating and cooling rates to minimize the exposure of the component surface to oxygen.
- Consider using protective gases or modifying the atmosphere to prevent decarburization.
4.Quench Cracking:
- Cause: Quench cracking occurs due to rapid and non-uniform cooling, resulting in high thermal stresses that exceed the material’s strength and lead to crack formation.
- Troubleshooting Strategies:
- Review the quenching media, its temperature, and agitation to ensure appropriate cooling rates and minimize thermal gradients.
- Evaluate the part geometry, thickness, and section variation to prevent localized stress concentrations.
- Consider implementing controlled cooling techniques, such as interrupted quenching or tempering, to relieve residual stresses and minimize the risk of quench cracking.
5.Distortion:
- Cause: Distortion refers to the undesired shape changes or warping of the heat-treated components, resulting from uneven heating or cooling.
- Troubleshooting Strategies:
- Review the fixturing or support methods to ensure even heat distribution and minimize uneven cooling.
- Analyze the heating and cooling rates, as well as the part geometry, to identify potential causes of distortion.
- Consider implementing stress relief steps, such as post-heat treatment machining or controlled cooling, to minimize distortion.
6.Surface Irregularities:
- Cause: Surface irregularities, such as pitting, scaling, or roughness, can occur due to inadequate cleaning, improper surface preparation, or excessive oxidation during case hardening.
- Troubleshooting Strategies:
- Ensure thorough cleaning of the component surface before case hardening to remove contaminants and foreign materials.
- Review the surface preparation techniques, including grinding or polishing, to achieve the desired surface finish.
- Optimize the case hardening atmosphere or the composition of the case hardening medium to minimize oxidation and scaling.
Troubleshooting heat treatment defects encountered during case hardening requires a systematic approach to identify the root causes and implement corrective measures. By reviewing process parameters, analyzing the case hardening atmosphere, optimizing quenching techniques, and considering factors such as fixturing and part geometry, manufacturers can effectively troubleshoot and resolve these defects. Continuous improvement, process monitoring, and adherence to heat treatment specifications are essential for achieving high-quality case-hardened components.