Gear hobbing is a complex machining process, and several challenges may arise during the production of gears. Here are some common challenges encountered in gear hobbing and possible solutions:
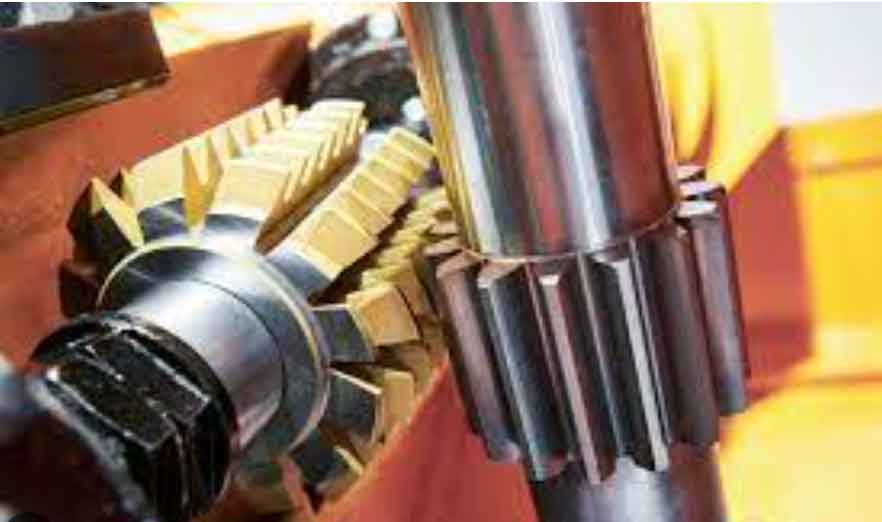
- Chipped or Worn Hob Teeth:
- Cause: Excessive hob wear or inadequate tool material.
- Solution: Use high-quality and wear-resistant hob cutters. Regularly inspect and replace worn hob cutters.
- Poor Surface Finish:
- Cause: Incorrect cutting parameters or inadequate tool sharpness.
- Solution: Optimize cutting parameters (speed, feed, and depth of cut) for the specific material and gear type. Ensure the hob cutter is sharp and in good condition.
- Inconsistent Gear Tooth Profiles:
- Cause: Misalignment of the hob cutter or workpiece, improper setup, or machine misalignment.
- Solution: Ensure proper alignment of the hob cutter and workpiece. Check and adjust machine alignments regularly.
- Chatter Marks on Gears:
- Cause: Vibration during the hobbing process.
- Solution: Increase machine rigidity, optimize cutting parameters, and ensure proper workpiece clamping.
- Gear Runout:
- Cause: Misalignment or eccentricity of the hob cutter or workpiece.
- Solution: Align the hob cutter and workpiece precisely, and check for any eccentricity.
- Tooth Overcut or Undercut:
- Cause: Incorrect settings of the hobbing machine or wrong hobbing technique.
- Solution: Adjust the hobbing machine settings and use the appropriate hobbing technique for the specific gear type.
- Chip Clogging:
- Cause: Insufficient chip removal or improper coolant flow.
- Solution: Ensure adequate chip evacuation and use proper coolant flow to prevent chip clogging.
- Machine Overload:
- Cause: Trying to remove too much material at once.
- Solution: Optimize the cutting parameters to avoid overloading the hobbing machine.
- Tool Breakage:
- Cause: Excessive cutting forces or improper hob cutter selection.
- Solution: Optimize cutting parameters and use a robust hob cutter suitable for the gear material and size.
- Workpiece Hardness Variation:
- Cause: Inconsistent material hardness.
- Solution: Ensure uniform material hardness in the workpieces by maintaining proper heat treatment processes.
- Workpiece Distortion:
- Cause: Improper workpiece clamping or material stress.
- Solution: Use proper workpiece clamping techniques and consider stress-relieving processes for the workpiece material.
- Galling or Burring:
- Cause: Insufficient lubrication or improper hob cutter setup.
- Solution: Use appropriate lubrication and ensure proper hob cutter setup to prevent galling and burring.
Implementing these solutions can help address common challenges in gear hobbing and ensure a smooth and efficient gear production process. Regular maintenance and monitoring of the hobbing machine and tooling are also essential to prevent issues and maintain consistent gear quality.
Pages: 1 2